Examining real-world case studies of heat treatment defects and their solutions provides valuable insights into the challenges faced in the heat treatment process and the strategies employed to overcome them. By understanding these cases, manufacturers can learn from past experiences and implement effective solutions to prevent or address similar defects in their own heat treatment operations. This article presents several case studies on heat treatment defects and the lessons learned from each, along with the corresponding solutions.
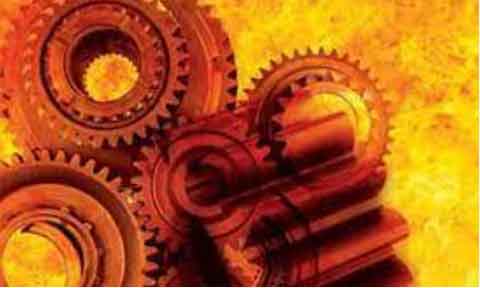
- Quench Cracking in Steel Components
- Description: A manufacturer was experiencing quench cracking in heat-treated steel components, leading to high rejection rates and compromised component integrity.
- Lessons Learned:
- The choice of quenching media and its cooling rate is critical in preventing quench cracking.
- The steel composition and hardenability must be carefully matched with the appropriate quenching medium to achieve the desired hardness without inducing excessive stresses.
- Solution:
- Conducted a thorough analysis of steel composition and adjusted the alloying elements to improve hardenability.
- Implemented an optimized quenching process using a specialized polymer quenchant with controlled agitation to achieve the desired cooling rate and minimize thermal stresses.
- Decarburization in Automotive Gear Components
- Description: An automotive gear manufacturer encountered decarburization issues on the surface of heat-treated gear components, resulting in reduced surface hardness and compromised gear performance.
- Lessons Learned:
- Proper atmosphere control during heat treatment is crucial to prevent decarburization.
- Controlling the carbon potential in the heat treatment furnace atmosphere is essential to maintain the desired carbon content on the surface of the components.
- Solution:
- Implemented tighter control over the atmosphere in the heat treatment furnace, ensuring a carbon-rich environment to prevent decarburization.
- Conducted regular atmosphere analysis and adjusted the gas composition as necessary to maintain the desired carbon potential.
- Distortion in Aluminum Heat-Treated Components
- Description: A manufacturer of aluminum components experienced distortion and dimensional inaccuracies after heat treatment, leading to fitment issues and scrap rates.
- Lessons Learned:
- Thermal management and fixture design play a critical role in minimizing distortion.
- Understanding the thermal properties and coefficient of thermal expansion (CTE) of the material is crucial in designing effective heat treatment fixtures.
- Solution:
- Implemented improved fixture design to minimize thermal stresses and distortion during the heat treatment process.
- Conducted a detailed analysis of the material’s CTE and adjusted the heating and cooling rates to minimize temperature gradients and reduce distortion.
- Surface Discoloration and Staining in Stainless Steel Components
- Description: A stainless steel component manufacturer faced surface discoloration and staining issues during heat treatment, resulting in aesthetic defects and potential corrosion susceptibility.
- Lessons Learned:
- Proper surface cleaning and protective atmosphere are critical in preventing surface discoloration and staining.
- Surface contamination, such as oils, greases, or residual grinding compounds, can lead to undesired reactions during heat treatment.
- Solution:
- Implemented a rigorous cleaning process to ensure the removal of surface contaminants before heat treatment.
- Utilized a controlled protective atmosphere, such as hydrogen or cracked ammonia, to prevent oxidation and surface discoloration during heat treatment.
Analyzing case studies of heat treatment defects and their solutions provides valuable insights into the challenges faced by manufacturers and the strategies employed to overcome those challenges. Lessons learned from these cases highlight the importance of factors such as quenching media selection, atmosphere control, thermal management, surface cleaning, and proper fixture design in achieving successful heat treatment outcomes. By applying these lessons, manufacturers can enhance their heat treatment processes, minimize defects, and ensure the production of high-quality heat-treated components.