High-volume gear manufacturing presents a unique set of challenges, driven by the demands for efficiency, consistency, quality, and cost-effectiveness. Addressing these challenges requires innovative approaches and the integration of advanced technologies. Here’s an overview of the primary challenges faced in high-volume gear manufacturing and the solutions that can be employed to overcome them.
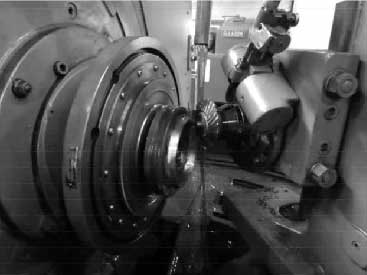
Challenges in High-Volume Gear Manufacturing
1. Maintaining Quality and Precision
In high-volume production, maintaining consistent quality and precision across all gear units can be difficult due to wear and tear on tools, variations in material properties, and process inconsistencies.
2. Efficiency and Throughput
Maximizing the production rate while minimizing waste and downtime is crucial for profitability. Balancing speed and quality often poses a significant challenge.
3. Material Management
Efficient management of materials, including procurement, storage, and waste reduction, is critical in high-volume manufacturing to control costs and ensure a smooth production flow.
4. Equipment Wear and Maintenance
Frequent equipment use leads to wear and tear, necessitating regular maintenance and, occasionally, downtime, which can disrupt production schedules.
5. Labor Costs and Skill Shortages
High-volume manufacturing often requires a substantial workforce. Labor costs can be significant, and there is also the challenge of finding skilled workers in a competitive job market.
Solutions for High-Volume Gear Manufacturing
1. Automation and Robotics
Integrating automation and robotics into the production line can significantly enhance efficiency and consistency. Automated machinery can operate around the clock, reducing labor costs and human error, and ensuring uniform quality across all products.
2. Advanced Quality Control Systems
Implementing advanced quality control systems, such as AI-powered inspection and real-time monitoring, can help in detecting and correcting deviations early in the production process, ensuring high-quality output.
3. Smart Material Management
Adopting smart inventory and material management systems, powered by IoT (Internet of Things) and AI, can optimize the supply chain, reduce waste, and ensure materials are available when needed, without excess.
4. Predictive Maintenance
Using predictive maintenance tools, which analyze data from machine sensors to predict equipment failures before they happen, can significantly reduce downtime and maintenance costs, ensuring continuous production flow.
5. Training and Upskilling
Investing in the training and upskilling of workers to operate advanced machinery and adopt new technologies is crucial. This not only addresses the skill shortage but also improves productivity and job satisfaction.
6. Lean Manufacturing Principles
Implementing lean manufacturing principles can streamline operations, reduce waste, and improve overall efficiency. This includes optimizing workflows, reducing inventory levels, and focusing on value-adding activities.
7. Customized Machinery and Tooling
Designing and utilizing customized machinery and tooling that are tailored to the specific requirements of high-volume gear production can enhance both efficiency and quality. Specialized equipment can reduce cycle times and improve the durability of tools.
Conclusion
High-volume gear manufacturing faces significant challenges that demand strategic solutions. By embracing automation, advanced quality control, smart material management, predictive maintenance, and continuous worker training, manufacturers can overcome these hurdles. Implementing these solutions not only addresses the immediate challenges but also positions manufacturers for sustainable growth and competitiveness in the global market.