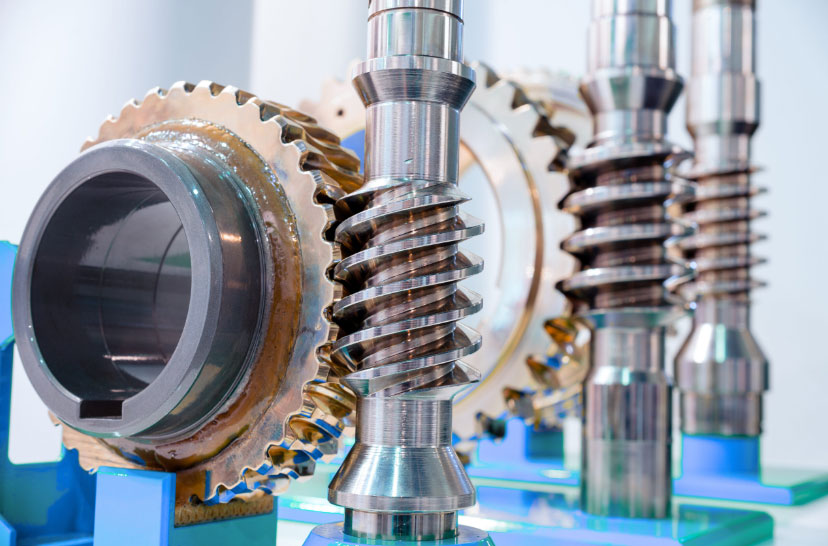
Quality control in the production of worm gear is essential due to their critical role in applications requiring precise and efficient power transmission at various angles and reductions. The unique challenges posed by worm gear manufacturing require specialized solutions to ensure high quality and performance. Here are some of the main challenges and corresponding solutions in the quality control of worm gear production:
Challenges in Worm Gear Quality Control:
- Complex Geometries and Tight Tolerances:
- Challenge: Worm gear involve complex surface geometries and must meet tight tolerances to ensure efficient meshing and operation. Precision in the helical threading of the worm and worm gear’s teeth profile is crucial.
- Solution: Employ advanced CNC machining centers that provide high precision and consistency. Utilize CAD/CAM systems to design and simulate worm gear profiles and threading to ensure they meet specifications before actual production.
- Material Selection and Consistency:
- Challenge: Selecting the right materials that can withstand the load, wear, and thermal conditions in worm gear operations is critical. Inconsistent material properties can lead to premature wear or failure.
- Solution: Implement stringent incoming material inspection processes and work closely with certified suppliers to ensure material quality. Conduct material tests such as hardness and composition analysis routinely.
- Surface Roughness and Finishing:
- Challenge: Worm gears require excellent surface finish to minimize friction and wear between the worm and the wheel. Any imperfections can reduce efficiency and worm gear’s lifespan.
- Solution: Use precision grinding and polishing processes post-machining to achieve the desired surface finish. Regularly calibrate finishing equipment to maintain consistency in surface treatment processes.
- Heat Treatment Variability:
- Challenge: Achieving uniform and correct heat treatment across worm gears is challenging but essential for ensuring their durability and performance.
- Solution: Standardize heat treatment processes and monitor them closely using temperature and time control technologies. Employ techniques such as case hardening or nitriding, tailored to the specific gear material and operational requirements.
- Alignment and Assembly Issues:
- Challenge: Incorrect alignment of worm and wheel can lead to inefficient operation and increased wear. Ensuring that worm gear align properly during assembly is challenging.
- Solution: Design custom jigs and fixtures to maintain alignment during assembly. Use laser alignment tools and other precision measuring instruments to check alignment before final assembly.
Solutions to Enhance Quality Control:
- Advanced Metrology Tools:
- Solution: Implement state-of-the-art metrology equipment, such as coordinate measuring machines (CMMs) and worm gear testers that provide detailed insights into worm gear geometry, pitch, and surface deviations.
- Statistical Process Control (SPC):
- Solution: Use SPC techniques to monitor and control manufacturing processes. Collect and analyze data to identify trends or deviations in real-time, allowing for immediate corrective actions.
- Automated Inspection Systems:
- Solution: Integrate automated optical inspection systems in the production line to identify surface defects and geometrical inaccuracies on the fly, ensuring high throughput without compromising on quality.
- Employee Training and Engagement:
- Solution: Regular training programs for operators on the latest gear manufacturing techniques and quality control procedures. Encourage a culture of quality and continuous improvement across the organization.
- Quality Certifications and Compliance:
- Solution: Obtain and maintain quality certifications like ISO 9001 to standardize quality procedures. These certifications not only bolster quality assurance processes but also enhance customer trust and marketability.
By addressing these challenges with targeted solutions, manufacturers can ensure the production of high-quality worm gear, leading to enhanced reliability, performance, and customer satisfaction in their applications.