Quality assurance in the manufacturing of spiral bevel gear involves a complex set of challenges due to the precision required in their design, production, and application. Here’s a detailed exploration of the main challenges in ensuring the quality of spiral bevel gear:
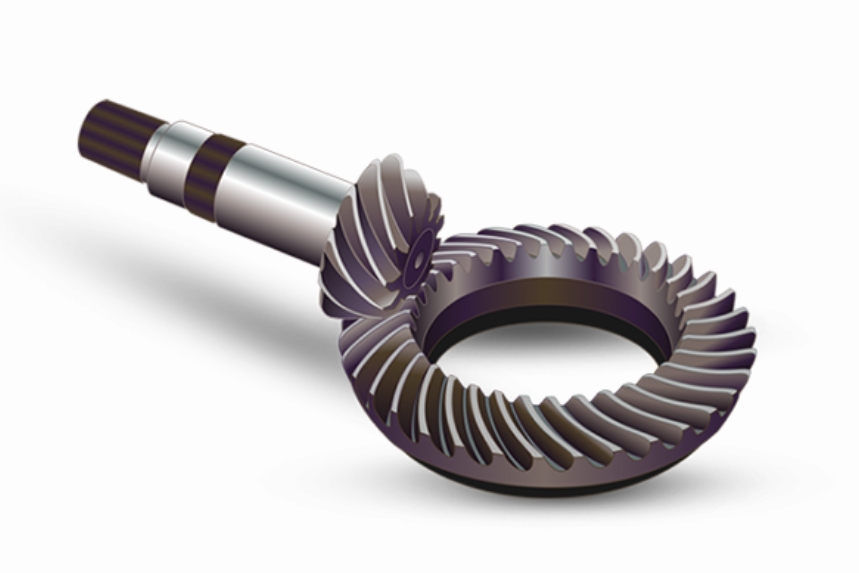
1. Complex Geometries and Precise Tolerances
- Precision Requirements: Spiral bevel gear must meet very tight tolerances to function correctly in applications that require precise angular motion and torque transmission. Achieving and consistently maintaining these tolerances during high-volume production is a significant challenge.
- Complex Profiles: The curved teeth and complex profiles of spiral bevel gear make them difficult to manufacture and inspect. Any deviation in tooth geometry can lead to noise, increased wear, and failure in service.
2. Material and Metallurgical Issues
- Material Consistency: Variability in material properties can affect the performance and durability of spiral bevel gear. Ensuring consistent material quality from suppliers and throughout the gear manufacturing process is crucial.
- Heat Treatment Variability: Heat treatments such as carburizing or case hardening are critical for achieving the required hardness and durability of spiral bevel gear. However, controlling these processes to achieve consistent results across batches can be challenging due to variations in furnace temperature, atmosphere composition, and timing.
3. Surface Finish and Microstructural Defects
- Surface Imperfections: Surface finish plays a critical role in the performance of spiral bevel gear, affecting noise, vibration, and wear characteristics. Achieving a high-quality surface finish while maintaining other geometric tolerances is challenging.
- Internal Defects: Microstructural defects such as inclusions, voids, or improper grain flow can lead to premature failure. Detecting these defects requires sophisticated non-destructive testing methods, which can be costly and time-consuming.
4. Accurate Measurement and Inspection
- Complex Inspection: Measuring the complex geometries of spiral bevel gear, particularly the tooth depth and angle, requires advanced metrology equipment and expertise. The inspection process can be time-intensive, adding to production costs.
- Consistency in Quality Checks: Ensuring that all gears pass through rigorous quality checks and that these checks are consistently applied can be a logistical challenge, especially when dealing with large volumes.
5. Tool Wear and Machine Calibration
- Tool Deterioration: The precision machining of spiral bevel gear puts significant wear on cutting tools. Managing tool life and predicting tool replacement intervals are necessary to maintain quality.
- Machine Maintenance: Regular calibration and maintenance of spiral bevel gear cutting and grinding machines are essential. Any drift in machine settings can lead to significant deviations in spiral bevel gear quality.
6. Assembly and Integration Testing
- Inter-component Compatibility: Spiral bevel gear often fail not due to individual defects but due to incompatibility with paired gears or misalignment in assemblies. Testing how individual spiral bevel gear perform in assembled conditions is critical but challenging.
- Functional Testing: Performing full functional tests of spiral bevel gear sets under load conditions that simulate actual operating environments is essential but can be resource-intensive.
7. Regulatory and Standard Compliance
- Compliance with Standards: Adhering to international standards (such as ISO, AGMA, etc.) requires continuous monitoring and adaptation of production processes, which can be challenging to maintain over time and across different product lines.
8. Skilled Workforce
- Expertise and Training: Maintaining a skilled workforce that understands the intricacies of spiral bevel gear manufacturing and can perform complex setups and quality assurance procedures is increasingly difficult, especially with the evolving technology landscape.
Addressing these challenges requires a systematic approach to quality assurance, investment in advanced manufacturing and inspection technologies, continuous training for employees, and a strong collaboration with material suppliers. By overcoming these challenges, manufacturers can ensure the production of high-quality spiral bevel gear that meet the demanding requirements of their applications.