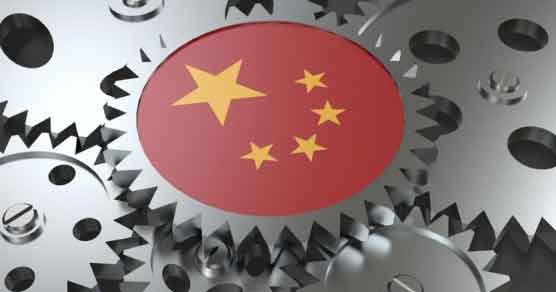
China has been at the forefront of manufacturing and has made significant strides in adopting Industry 4.0 technologies to enhance productivity in the gear manufacturing industry. Industry 4.0, also known as the Fourth Industrial Revolution, refers to the integration of digital technologies into manufacturing processes to create a more connected and automated environment.
In the context of gear manufacturing, Industry 4.0 brings various advancements that improve productivity, efficiency, and quality. Let’s explore some of the ways China gear manufacturers are embracing Industry 4.0:
- Automation and Robotics: China gear manufacturers are increasingly utilizing automation and robotics to streamline production processes. Automated systems can handle repetitive tasks, such as gear cutting, grinding, and assembly, with high precision and efficiency. By reducing manual labor, manufacturers can improve productivity, reduce errors, and enhance overall product quality.
- Internet of Things (IoT) and Connectivity: IoT plays a crucial role in Industry 4.0, enabling devices and machines to communicate and share data in real-time. Gear manufacturers in China are leveraging IoT technologies to create a connected ecosystem where machines, sensors, and control systems work together seamlessly. This connectivity enables real-time monitoring, predictive maintenance, and data-driven decision-making to optimize production processes.
- Big Data and Analytics: China gear manufacturers are harnessing the power of big data and analytics to gain valuable insights into their manufacturing operations. By collecting and analyzing data from various sources, such as machine sensors, production systems, and quality control processes, manufacturers can identify patterns, optimize production parameters, and make informed decisions to enhance productivity and minimize downtime.
- Artificial Intelligence (AI) and Machine Learning: AI and machine learning algorithms are being employed by China gear manufacturers to optimize production planning, quality control, and predictive maintenance. These technologies can analyze large volumes of data to detect anomalies, identify potential failures, and optimize manufacturing parameters. By continuously learning from data, AI systems can improve production efficiency and reduce costs over time.
- Additive Manufacturing: Also known as 3D printing, additive manufacturing is revolutionizing the gear manufacturing industry. China manufacturers are adopting this technology to produce complex gear designs with high precision and efficiency. Additive manufacturing allows for rapid prototyping, customization, and the creation of lightweight and durable gear components, which can contribute to increased productivity and reduced material waste.
- Collaborative Manufacturing: Industry 4.0 encourages collaboration among various stakeholders in the manufacturing ecosystem. China gear manufacturers are embracing collaborative manufacturing approaches, such as supply chain integration and digital platforms, to enhance coordination, information sharing, and overall productivity. This collaboration helps streamline processes, reduce lead times, and ensure seamless production flow.
Overall, China gear manufacturers are actively embracing Industry 4.0 technologies to enhance productivity, improve product quality, and maintain their competitive edge in the global market. By adopting automation, IoT, big data analytics, AI, additive manufacturing, and collaborative approaches, China gear manufacturers are well-positioned to meet the demands of the modern manufacturing landscape.