In the field of mechanical engineering, the design and calculation of gears play a crucial role in the performance and reliability of various machinery. This article focuses on the clone design and calculation of modified helical cylindrical gears, exploring the key factors and methods involved in this process.
The use of modified gears is common in many applications, especially when dealing with small gears with a modulus of 1 mm and a number of teeth less than 12, or in cases where specific requirements such as avoiding undercutting, improving tooth strength, or matching center distances are needed. Worms and worm gears also often utilize modified versions to enhance their performance.
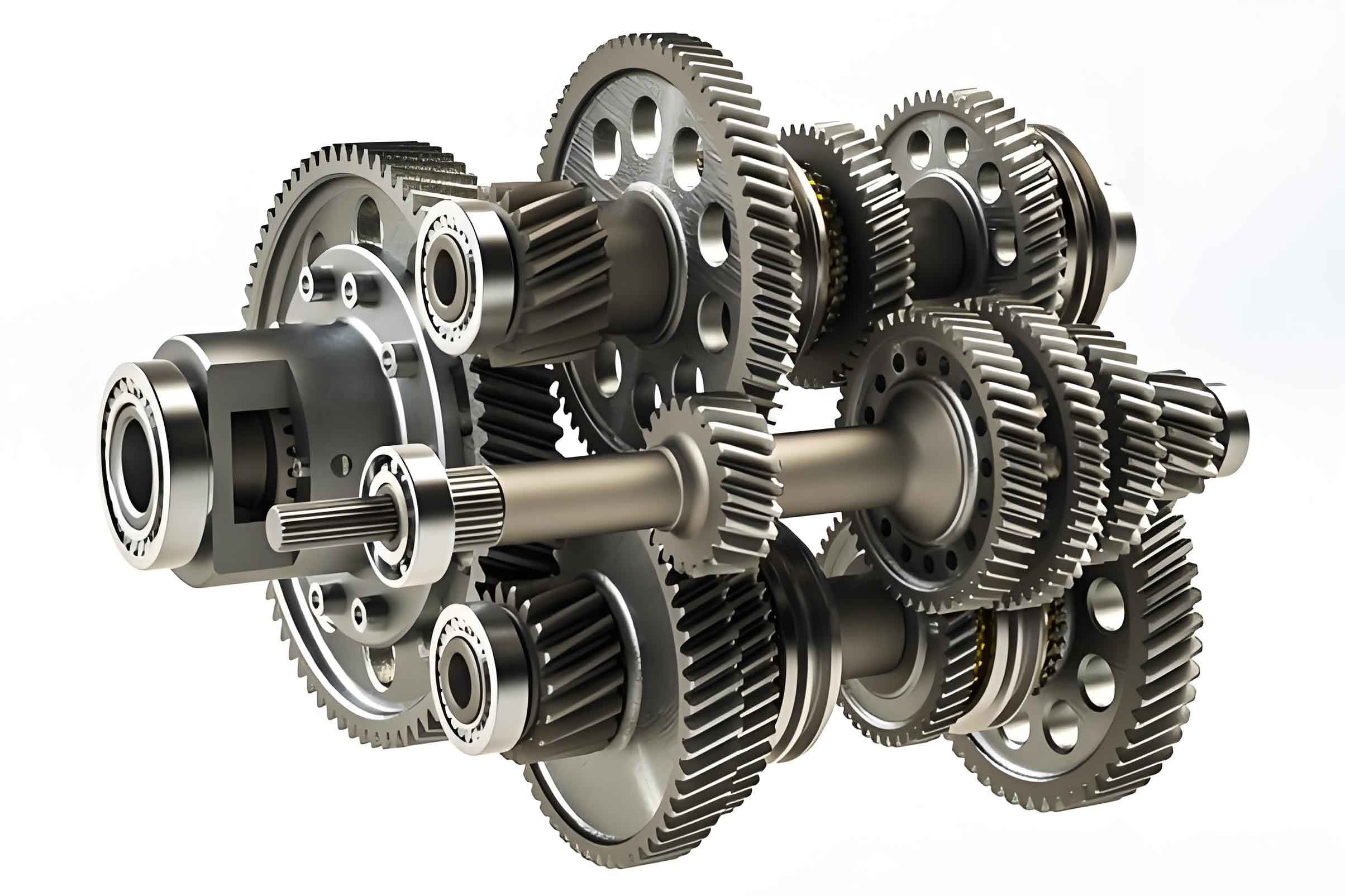
Let’s take the example of an electric vehicle glass lifter to illustrate the importance of modified gears. The structure and working principle of the electric vehicle glass lifter are as follows: a DC motor drives a worm shaft, which has two left and right worm teeth at the upper end. When the worm shaft rotates in the forward direction (clockwise), the right worm tooth engages with the worm gear of the right tooth-worm double coupling to transmit motion, while the left worm tooth is disengaged. Conversely, when the worm shaft rotates in the reverse direction (counterclockwise), the left worm tooth engages, and the right worm tooth is disengaged. The right and left gears, both helical cylindrical gears with 8 teeth each, engage with the large gear (with 42 teeth) to control the rotation of the window glass. The helical teeth of these gears engage and disengage gradually, providing a smoother transmission.
To determine whether the gears in the electric vehicle glass lifter are modified, we need to observe and measure them. The minimum number of teeth for a gear during machining is limited to avoid undercutting, which weakens the tooth strength and reduces the quality of gear transmission. For example, for an external spur gear with a pressure angle of 20° and a tooth height coefficient of 1, when the module is greater than 1, the minimum number of teeth without undercutting is 17. When the module is less than or equal to 1, the minimum number of teeth without undercutting is 14, and the actual minimum number of teeth can be 12. Since the left and right gears in the glass lifter have only 8 teeth, they must be modified gears to avoid undercutting.
By comparing the measured values of the tooth top circle diameter and the center distance of the gears with the theoretical values of non-modified gears, we can further confirm the use of modified gears. For instance, the actual tooth top circle diameter of the left and right gears (Φ11.86 mm) is significantly larger than the non-modified theoretical value (Φ10.88 mm), and the actual center distance between the left and right gears and the large gear (27.8 mm) is also larger than the non-modified center distance (26.96 mm). This indicates that the left, right gears, and the large gear all employ the modified method.
There are various types of modified methods for cylindrical helical gears, and selecting the appropriate one is crucial to achieve the desired objectives. For example, there are height modification and angle modification for cylindrical helical gear meshing. When the height meshing center distance (A) is equal to the non-modified meshing center distance (A0), and the modification coefficients (ξ1 and ξ2) satisfy ξ1 = ξ2 and ξ∑ = ξ1 + ξ2 = 0, one gear has a positive modification (ξ1 > 0), and the other has a negative modification (ξ2 < 0). However, in the case of the car lifter, A = 27.8 mm, A0 = 26.96 mm, and A ≠ A0, so this type of modification method is not applicable. Angle modification can be divided into positive angle modification and negative angle modification, each with three sub-cases, distinguished by the values of the modification coefficients (ξ) of the two meshing gears.
To calculate the geometric dimensions of the modified helical cylindrical gears, we need to consider several factors. For example, when calculating the minimum modification coefficient (ξmin) to avoid undercutting or allow for slight undercutting, we need to ensure that the modification coefficient does not reduce the expected meshing coefficient or shorten the effective part of the tooth profile. When f = 1 and αon = 20°, the minimum modification coefficient without undercutting is ξmin = (17 – Z1) / 17 = 0.529, and the minimum modification coefficient allowing for slight undercutting is ξmin = (14 – Z1) / 17 = 0.353.
Another factor to consider is the maximum modification coefficient (ξmax) to avoid tooth tip sharpening. When f = 1, αon = 20°, and Z = 8, ξmax = 0.565 and ξmin = 0.255. However, the modification coefficient should satisfy ξmax ≥ ξ ≥ ξmin. If the selected modification coefficient exceeds ξmax, it is necessary to check the value of the tooth top width (Sw) and determine whether the selected ξ value is allowed based on the specific situation.
The calculation of the geometric parameters of the modified helical cylindrical gears includes the calculation of the normal total modification coefficient (ξn∑) and the selection of the normal modification coefficients (ξn1 and ξn2) for the left, right gears, and the large gear. Based on these calculations, we can determine the values of parameters such as the pitch circle diameter, addendum circle diameter, base circle diameter, tooth addendum height, tooth dedendum height, tooth full height, number of teeth in span, and common normal length.
For example, in the case of non-modified helical cylindrical gears, with known conditions such as Z1 = 8, Z2 = 42, mon = 1 mm, αon = 20°, βf = 22°, fon = 1, and Con = 0.25, we can calculate the following parameters:
Parameter | Value |
---|---|
End face module (ms) | 1.0785347 mm |
End face tooth profile angle (αos) | 21°25’57” ≈ 21°26′ |
Tooth addendum height (hw) | 1 mm |
Tooth full height (h) | 2.25 mm |
Pitch circle diameter (df1) | 8.6282776 mm |
Pitch circle diameter (df2) | 45.298457 mm |
Non-modified meshing center distance (A0) | 26.963368 mm |
End face (pitch circle) meshing angle (αs) | 25°28′ |
For angle-modified helical cylindrical gears, given a measured meshing center distance of A = 27.8 mm and a calculated non-modified center distance of A0 = 26.96 mm, we can calculate the following parameters:
Parameter | Value |
---|---|
Normal total modification coefficient (ξn∑) | Approximately 0.914 |
End face center distance variation coefficient (λs) | 0.7757117 |
Normal center distance variation coefficient (λn) | 0.836632 |
Normal tooth addendum height reduction coefficient (σn) | 0.0767768 |
Tooth addendum height (hw1) | Approximately 1.54 mm |
Tooth addendum height (hw2) | Approximately 1.22 mm |
Tooth top circle diameter (dw1) | Approximately 11.7 mm |
Tooth top circle diameter (dw2) | Approximately 47.8 mm |
Tooth full height (h1 and h2) | 2.17 mm |
Dedendum height (hi1) | Approximately 0.636 mm |
Dedendum height (hi2) | Approximately 0.95 mm |
End face meshing module (mbs) | 1.112 |
Pitch circle diameter (d1) | 8.896 mm |
Pitch circle diameter (d2) | 46.704 mm |
Base circle spiral angle (βi) | 20°36’38” |
Base circle diameter (dj1) | 8.03 mm |
Base circle diameter (dj2) | 42.17 mm |
Tooth top circle end face pressure angle (αwsl) | 46.623947° |
Tooth top circle end face pressure angle (αws2) | 27.974741° |
Number of teeth in span (Z1 = 8) | 2 |
Number of teeth in span (Z2 = 42) | 7 |
Oblique tooth common normal length (L1) | Approximately 4.937 mm |
Oblique tooth common normal length (L2) | Approximately 20.175 mm |
The design of the modified helical cylindrical gears relies on the mapping data of the samples and the calculation based on the center distance data of the installation holes of the large gear and the left and right tooth-worm double couplings in the gear box and gear cover, as well as the module, number of teeth, and major diameter data of the sample gears. For example, the design of the large modified gear and the left (right) modified gear is shown in Figure 3, where the dimensions and parameters are determined based on these considerations.
In conclusion, for gears with a number of teeth less than 17 and a module less than or equal to 1, or for small module gears with a number of teeth less than 14, the modified method must be used for calculation, design, and manufacturing to avoid undercutting. For the cloning of such products, it is necessary to conduct actual measurements, compare and calculate, determine their nature and modification type, and perform quantitative calculations of various geometric dimensions before proceeding with product drawing design and mold design and manufacturing. Otherwise, it will lead to rework and unnecessary economic losses.
Furthermore, the development of advanced manufacturing technologies and the pursuit of high-performance machinery require continuous innovation and optimization in the design and calculation of gears. Manufacturers and engineers need to stay updated with the latest research and technological advancements to ensure the reliability, efficiency, and precision of mechanical systems. This includes exploring new materials, manufacturing processes, and design methodologies to meet the increasing demands of various industries.
In the future, we can expect further advancements in the field of modified gear design and calculation, leading to more efficient and reliable mechanical transmissions. The integration of digital technologies, such as computer-aided design (CAD) and finite element analysis (FEA), will enable more accurate modeling and simulation of gear performance, facilitating the optimization of gear geometries and parameters. Additionally, the development of new materials with improved mechanical properties will provide more options for gear designers to enhance the strength, durability, and performance of gears.
Moreover, the increasing emphasis on sustainability and energy efficiency will also drive the research and development of more energy-efficient gear systems. This may involve the design of gears with lower friction losses, improved lubrication systems, or the integration of gears with other components to achieve better overall system performance.
In summary, the clone design and calculation of modified helical cylindrical gears is a complex but essential aspect of mechanical engineering. By understanding the principles and methods involved, and continuously striving for innovation and improvement, we can ensure the development of high-quality mechanical products that meet the diverse needs of various industries.