In order to compare the time-varying meshing stiffness results obtained by the three calculation methods of material mechanics method, finite element method and improved LTCA method, the three calculation results shown in the figure are compared and analyzed.
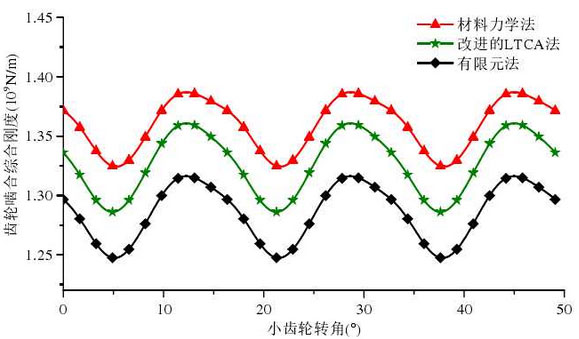
It can be seen from the figure that the value of time-varying meshing stiffness calculated based on the material mechanics method is the largest, the result based on the finite element method is the smallest, and the result based on the improved LTCA method is between the two. This is due to the fact that the material mechanics method only considers the deformation of gear teeth without considering the torsional deformation of gear matrix and shaft, resulting in the smaller deformation, so the meshing stiffness value is too large; the finite element method adopts quasi-static method, the gear has a certain speed in the simulation process, which will produce vivid load, but when calculating the mesh stiffness, the normal force still uses the static load, so the meshing stiffness is calculated The mesh stiffness obtained by the improved LTCA method is between the first two methods.
The formation principle of dynamic excitation of time-varying meshing stiffness is described. The calculation methods of time-varying meshing stiffness based on material mechanics method and finite element method are introduced. The calculation method of time-varying meshing stiffness based on improved LTCA method is proposed. Then, taking the input gear pair of an electric vehicle reducer as an example, the time-varying meshing stiffness curve of the gear pair is calculated. Finally, by comparing the results of the three methods, the time-varying mesh stiffness results based on the improved LTCA method are determined.