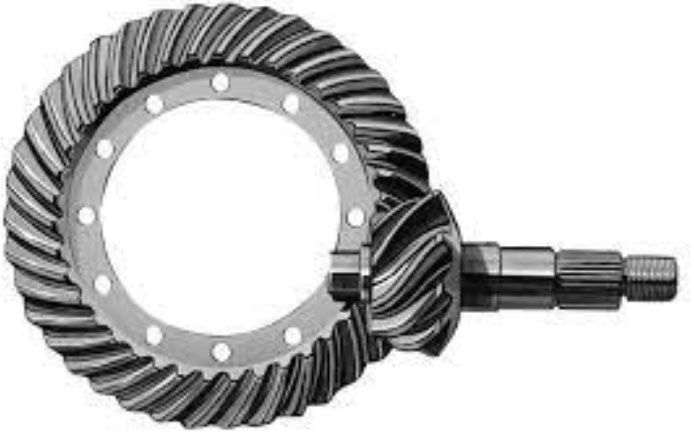
When selecting between hypoid gears and spiral bevel gears, it’s important to consider the specific requirements of the application and the advantages each gear type offers. Let’s compare hypoid gears and spiral bevel gears based on various factors:
1. Offset Design:
- Hypoid Gears: Hypoid gears have an axial offset between the pinion and gear axes, allowing for a larger pinion diameter and increased torque capacity.
- Spiral Bevel Gears: Spiral bevel gears have their pinion and gear axes intersecting at a 90-degree angle, providing a compact and efficient design.
2. Torque Transmission:
- Hypoid Gears: Hypoid gears can transmit higher torque loads due to their larger pinion diameter and offset design, making them suitable for heavy-duty applications.
- Spiral Bevel Gears: Spiral bevel gears also offer good torque transmission capability but may have slightly lower torque capacity compared to hypoid gears.
3. Noise and Vibration:
- Hypoid Gears: Hypoid gears generally provide smoother tooth engagement, resulting in quieter operation compared to traditional spiral bevel gears.
- Spiral Bevel Gears: Spiral bevel gears can produce more noise and vibration during operation, which may require additional noise reduction techniques in certain applications.
4. Efficiency:
- Hypoid Gears: Hypoid gears tend to have higher mechanical efficiency compared to worm gears but may have slightly lower efficiency compared to spiral bevel gears.
- Spiral Bevel Gears: Spiral bevel gears offer good efficiency, making them suitable for a wide range of applications.
5. Gear Meshing:
- Hypoid Gears: The sliding contact between hypoid gear teeth can result in higher contact stresses and require careful lubrication and cooling to minimize wear.
- Spiral Bevel Gears: Spiral bevel gears have rolling contact between teeth, which generally reduces wear and allows for smoother gear meshing.
6. Application Suitability:
- Hypoid Gears: Hypoid gears are well-suited for automotive differentials, heavy machinery, and other applications requiring higher torque capacity and right-angle transmission.
- Spiral Bevel Gears: Spiral bevel gears are commonly used in right-angle drives, marine applications, industrial machinery, and other systems requiring compact and efficient power transmission.
7. Manufacturing Complexity:
- Hypoid Gears: Hypoid gears are more complex to manufacture due to their offset design and sliding contact, which may result in higher production costs.
- Spiral Bevel Gears: Spiral bevel gears are more straightforward to manufacture, making them a cost-effective choice for various applications.
Hypoid gears offer advantages in terms of higher torque capacity, smoother operation, and quieter performance, making them suitable for heavy-duty and automotive applications. On the other hand, spiral bevel gears provide compact and efficient power transmission with good torque capabilities and are commonly used in various industrial and marine applications.
Ultimately, the choice between hypoid gears and spiral bevel gears depends on the specific requirements, load capacity, noise considerations, and cost constraints of the intended application. Working with gear design experts and considering the unique demands of the system will help determine the best gear type for optimal performance and longevity.