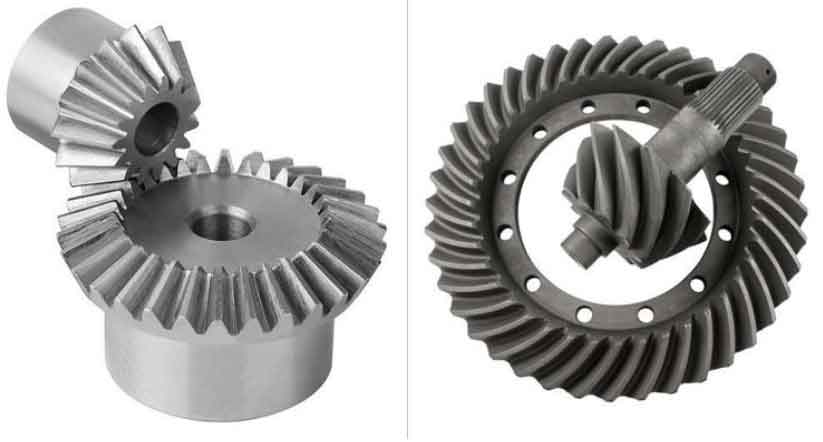
Comparing straight bevel gears to spiral bevel gears involves considering their respective advantages and disadvantages in various applications. Both types of gears are used for power transmission between intersecting shafts at right angles, but they have distinct design features and performance characteristics. Let’s examine the pros and cons of each:
Straight Bevel Gears:
Pros:
- Simplicity: Straight bevel gears have a simple design with straight teeth, making them easier and more cost-effective to manufacture and maintain.
- Efficiency: Straight bevel gears offer relatively high efficiency in power transmission, especially for low to moderate speeds and loads.
- Load Distribution: They distribute loads over a larger tooth surface area compared to spiral bevel gears, contributing to good load-carrying capacity.
- Compactness: Straight bevel gears are more compact than spiral bevel gears, which can be advantageous in certain space-constrained applications.
- Low Axial Thrust: Straight bevel gears generate lower axial thrust, requiring less thrust management in the system.
Cons:
- Noise and Vibration: Straight bevel gears can produce higher noise and vibration levels during operation due to their instantaneous tooth engagement.
- Limited Speed Range: They may have limitations at high speeds due to potential tooth deflection and increased noise levels.
- Lower Load Capacity: Compared to spiral bevel gears, straight bevel gears have lower load capacity and may not be as suitable for high-load applications.
Spiral Bevel Gears:
Pros:
- Smooth Operation: Spiral bevel gears have a gradual tooth engagement, resulting in smoother and quieter operation compared to straight bevel gears.
- Higher Load Capacity: Spiral bevel gears can handle higher loads and transmit torque more efficiently due to their inclined tooth design.
- High-Speed Capability: They perform well at high speeds due to reduced noise, vibration, and tooth deflection issues.
- Better Heat Dissipation: Spiral bevel gears offer improved heat dissipation due to their larger tooth surface area, making them suitable for high-power applications.
- Stronger Tooth Contact: They provide stronger tooth contact and increased resistance to tooth shear forces.
Cons:
- Complexity: Spiral bevel gears have a more complex design with curved teeth, making them more challenging to manufacture and potentially more expensive.
- Manufacturing Costs: The complexity and precision required in manufacturing can lead to higher production costs.
- Axial Thrust: Spiral bevel gears generate axial thrust that needs to be managed in the system design.
Choosing Between Straight Bevel and Spiral Bevel Gears:
- For applications where simplicity, cost-effectiveness, and moderate loads are crucial, straight bevel gears may be preferred.
- For applications requiring smooth and quiet operation, high load capacity, and high-speed capability, spiral bevel gears are often the better choice.
- The specific requirements of each application, including load, speed, space constraints, noise sensitivity, and budget considerations, will determine the most suitable gear type.
In summary, straight bevel gears are more straightforward and economical but may produce more noise and have lower load capacity. Spiral bevel gears offer smoother operation, higher load capacity, and better heat dissipation but come with increased complexity and manufacturing costs. The selection of the appropriate gear type depends on the specific needs and performance requirements of the application.