1. Composition of measurement system
In order to meet the industrial production environment, the helical gear angle measurement system should be combined with the end face measurement system. An industrial device for on-line measurement of helical gear end face is shown in Fig. 1.
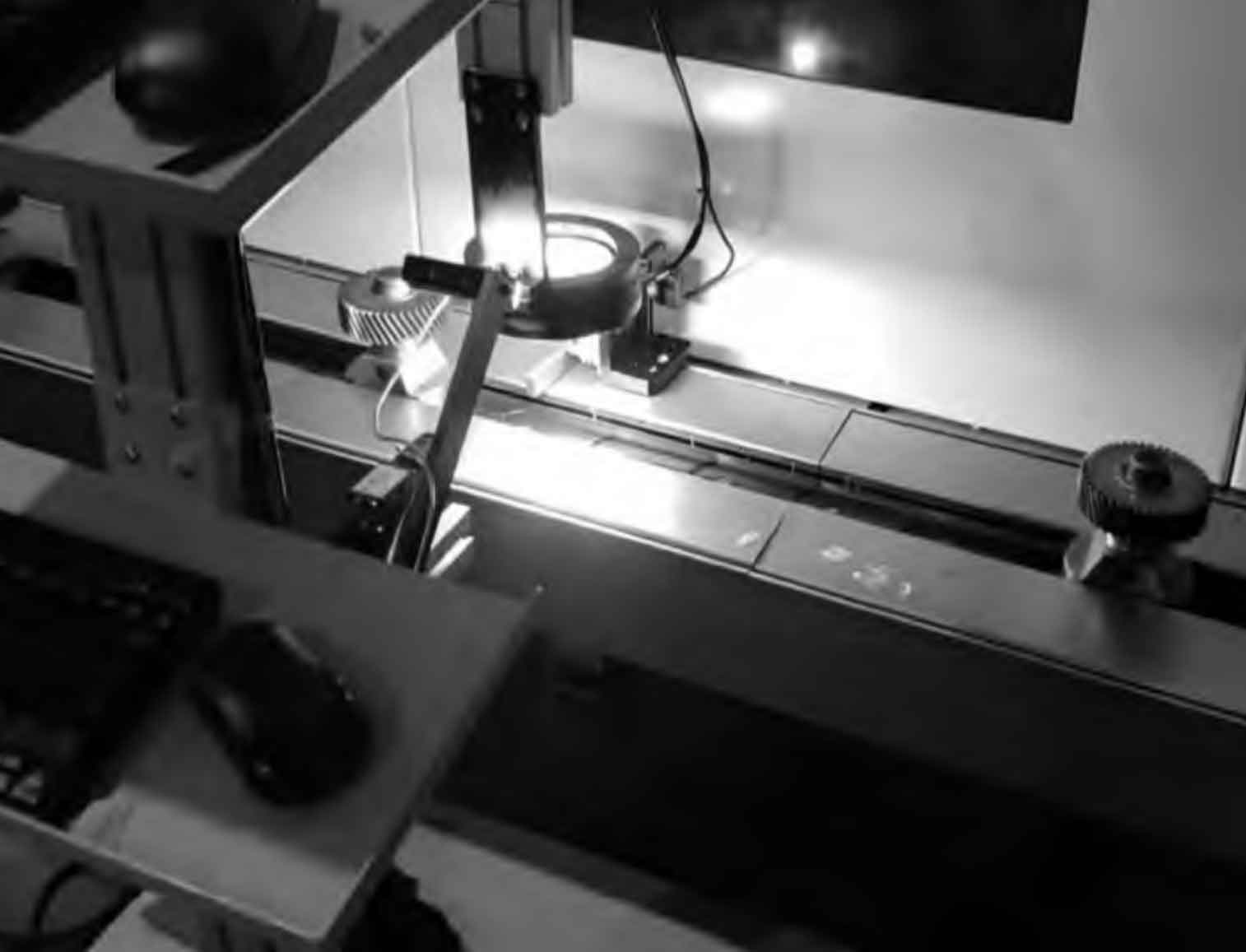
The device can measure the end face parameters of a helical gear every 2 s. The author’s measurement system mainly includes ring light source 1, strip light source 2, 2 × 106 pixel CCD camera, CMOS camera, lens 1, dual telecentric lens 2, camera bracket and computer. The measurement system is shown in Fig. 2.
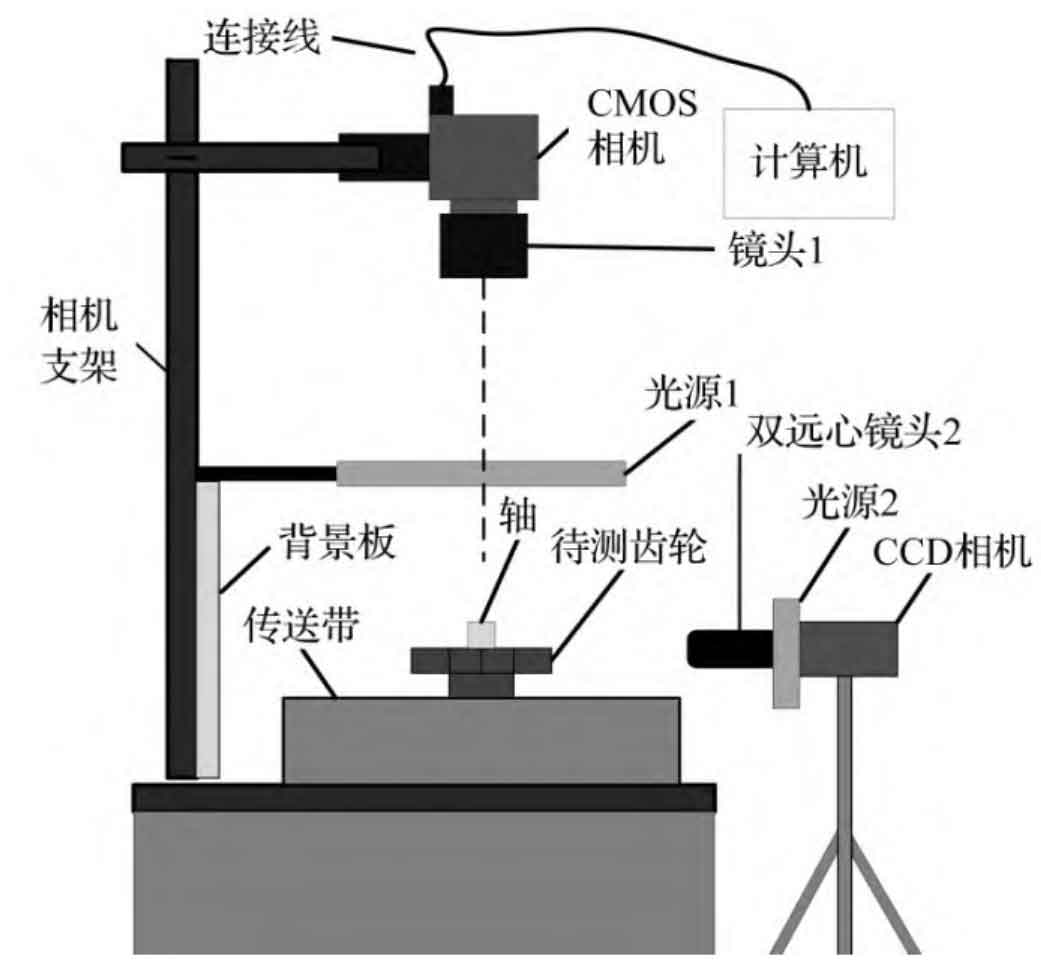
The CPU of the computer is AMD r5-4600h. The LED side strip light source and the upper light source are combined for illumination, which can increase the contrast of the helical gear side tooth line edge. The CCD camera is fixed relative to the horizontal plane to collect the side image of the helical gear placed horizontally. The CCD camera needs to use two levels to adjust the pitch angle and left and right tilt angles of the camera respectively. The depth of field of the dual telecentric lens is 18 mm. The double telecentric lens has the characteristics of wide depth of field, low distortion and no perspective error.
2. Workflow
The work flow of measurement mainly includes three parts: system installation and debugging, image preprocessing, gear rotation direction and helical gear angle determination. The installation and debugging of the measurement system mainly includes the installation and assembly error correction of the light source, bracket, camera and workpiece fixing device; Image preprocessing mainly includes camera calibration, distortion correction, ROI extraction and image graying; The determination of gear rotation direction and helical gear angle includes edge detection, morphological processing, curve fitting and other operations, and finally the helical gear rotation direction and helical angle are obtained β Value of.