The hardness results of carburized layer of heat treated 2.3cr-0.9si-0.3mo steel were measured in the conversion gas reduction furnace and the drop type oxidation furnace, as shown in Figure 1. The surface hardness of the carburized sample is as low as 60HV after reduction by conversion gas. In addition, the hardness and depth of the hardened layer are greater than that of the sample in the drop type oxidation furnace.
As shown in Fig. 1 (a) and (b), the morphology and distribution of surface oxides show significant differences in carburizing equipment. Fig. 1 (a) is the SEM analysis result of low magnification of the carburized gear surface in the conversion gas reduction furnace. The gear surface has discontinuous particle shape, and the overall distribution is uniform. On the other hand, as shown in Fig. 1 (b), the surface of the heat-treated gear in the trickling oxidation furnace is uniformly covered by a smooth film. Due to the different characteristics of equipment, the difference of surface reaction during carburizing can also be clearly confirmed in the section.
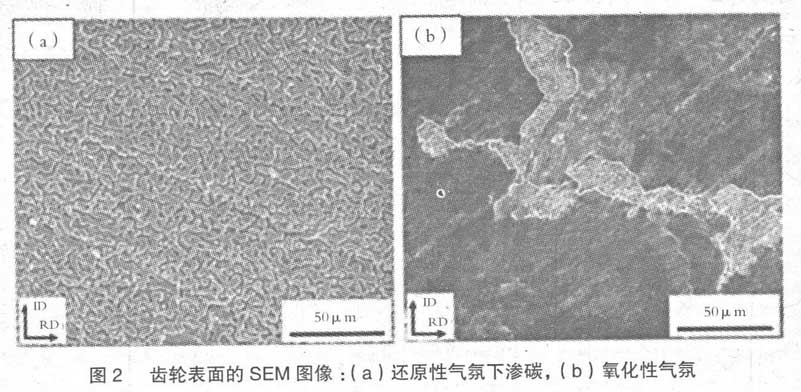
Fig. 2 (a) is the analysis result of gear cross section after carburizing treatment in conversion gas reduction furnace. In Fig. 1 (a), the thickness of granular surface structure confirmed by surface analysis is about 3 μ m, and the spherical oxide with size less than 1 μ m is distributed below the surface, with depth of about 3 μ M. intergranular oxidation is uniformly distributed as a whole, with depth of 10 μ M. On the contrary, when carburizing with drop type oxidation furnace, intercrystalline oxidation does not occur, but oxide film with thickness of about 3 μ m is formed on the surface, as shown in Fig. 2 (b). In addition, although spherical oxides are distributed in the area about 1 μ m below the surface, the number of them is less than that of the carburized samples in the conversion gas reduction furnace.
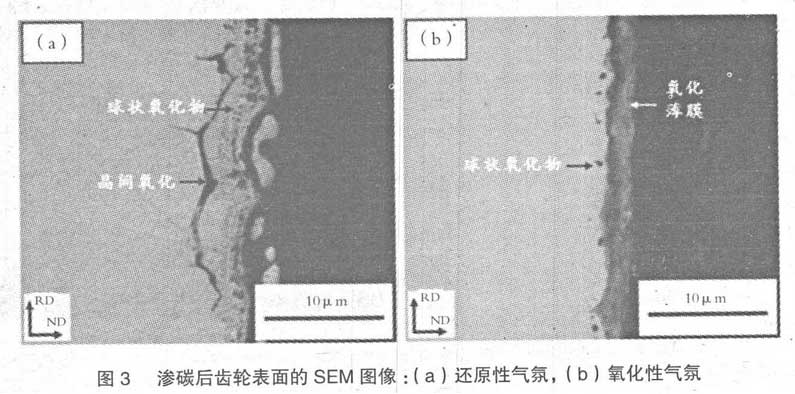
In order to compare the oxidation characteristics of the samples confirmed by SEM, TEM analysis was carried out. Fig. 3 is the analysis results of TEM and EDS for the section of 2.3cr0.9si-0.3mo Steel Carburized in the reduction furnace of conversion gas. Firstly, the discontinuous granular structure uniformly distributed on the surface is identified as non oxidized Fe. Most of the spherical oxides observed in the 3 μ m region below the surface are Si oxides of tens to hundreds of nanometers, while CR oxides have an irregular shape (Fe, Cr) 3O4 spinel structure of about 1 μ M. In addition, the intergranular oxide confirmed in the depth of 3-10 μ m is composed of Si oxide. This may be due to the fact that the oxygen contained in the atmosphere gas is easy to diffuse along the grain boundary during carburizing, and it preferentially reacts with Si, which has the highest oxygen affinity.
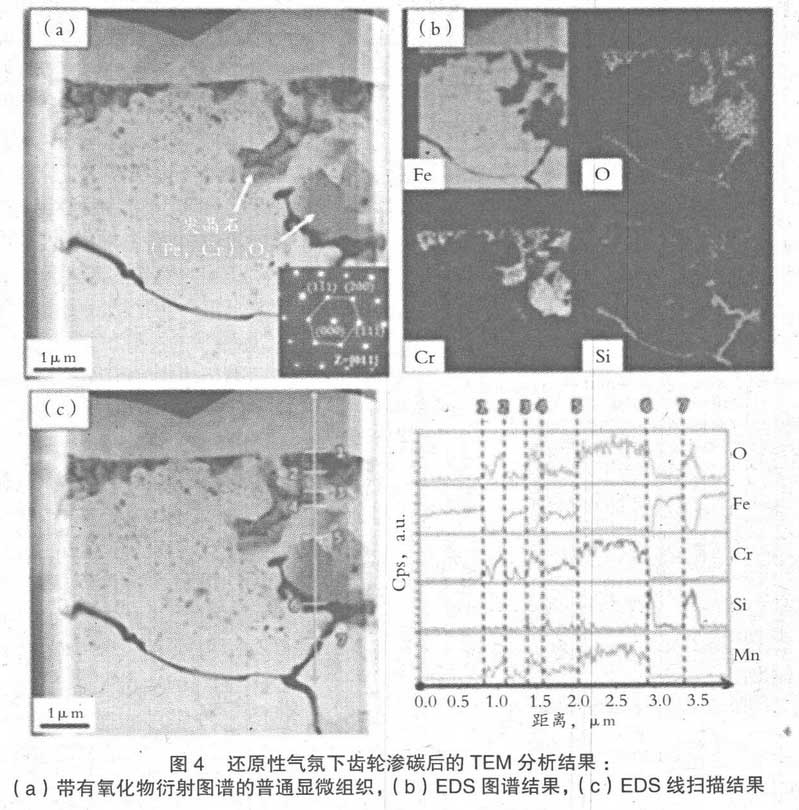
On the other hand, as shown in Fig. 5, most of the oxides are formed on the surface in the form of thin film. The composition and diffraction pattern analysis of the oxide film with a thickness of about 3 μ m show that the order from the outside is Fe2O3 (hematite) – Fe3O4 (magnetite) – (Fe, Cr) 3O4 (spinel). In addition, Si oxide is mainly spherical oxide inside the gear, but it is uniformly distributed in the spinel magnetite layer of the film. Under different temperature / atmosphere, the oxidation / reduction behavior between gas and metal elements during carburizing heat treatment was studied. During carburizing, the gases forming the atmosphere in the furnace have different reactivity with metal elements, which can be roughly divided into oxidizing O2, CO2, H2O and reducing H2 and Co. the following reactions can take place. Generally, the gases involved in the reaction are determined by means of Ellingham diagram, and whether the oxidation / reduction reaction has taken place is confirmed.
M+1/2O2→MO (4)
M+H2O→MO+H2(5)
M+CO2→MO+CO (6)
Generally speaking, in the early stage of the process, the oxidation caused by O2 and H2O preferentially reacts with elements with strong oxidation tendency, such as Cr, Mn, Si, etc. through selective oxidation, thus forming oxides. Therefore, in this study, due to the small difference between the gas measurement results and the equipment, by analyzing the oxidation behavior of Fe under the action of CO / CO2, rather than the selective oxidation of Cr / Si and O2 / H2O at the initial stage of the reaction, we can compare the Fe oxidation / reduction reaction on the surface of the heat-treated samples in the two equipment.
The reference values of CO / CO2 for oxidation / reduction of Fe and Fe oxides, as well as the measured values under different equipment and atmospheres, confirmed with the help of erlingham diagram, are shown in Table 3. For the oxidation / reduction reaction of Fe, if the measured partial pressure ratio of CO / CO2 is less than the equilibrium value (CO ↓ or CO2 ↑), the oxidation reaction becomes active on the right side. On the contrary, if the partial pressure ratio of CO / CO2 is greater than the equilibrium value (CO ↑ or CO2 ↓), the reduction reaction will become active if it is on the left side.
Therefore, the partial pressure ratio of CO / CO2 in the reduction furnace is 1.16e + 2, which is less than 1.08e + 7 and 1.01e + 6 of Fe FeO and Fe3O4 reaction, but more than 1.01e + 2 of fe3o4-fe2o3 reaction. Therefore, in the equipment atmosphere of conversion gas, during carburizing, Fe undergoes oxidation process and finally forms Fe3O4, namely magnetite. It is worth mentioning that, unlike the Fe oxidation process of “Fe → FeO → Fe3O4”, Cr containing alloy steel forms Cr2O3 instead of inhibiting the formation of FeO, so as to stabilize (Fe, Cr) 3O4, which is basically consistent with the characteristics of surface oxidation film observed in this study.
On the other hand, the Co / CO2 partial pressure ratio of the trickling furnace is 0.43e + 2, which is equivalent to the stable region of Fe2O3. Therefore, in the early stage of the reaction, the (FeCr) 3O4 preferentially formed on the surface of the gas component in the atmosphere is continuously oxidized by CO2, which makes Fe in the most stable state, i.e. the transformation to Fe2O3 (hematite). In this oxidation process, CO2 with larger molecular weight will not enter the interior of the material, but will diffuse to the gas oxide interface through Fe2 / 3 + / – Cr3 + cations contained in Fe / Cr or surrounding oxides, thus forming a surface film. In addition, although the Oxidation Reactivity of Cr is stronger than that of Fe, the internal diffusion or replacement speed of Cr oxide is slower than that of Fe. Therefore, Cr mainly exists in the film, i.e., in the form of (Fe, Cr) 3O4 on the sample surface film interface. With the continuous diffusion of Fe, the oxide layer of fe3o4-fe2o3 was formed to the outside of spinel. Finally, the layer structure of Cr (Fe, Cr) 3O4 (spinel) – Fe3O4 (magnetite) – Fe2O3 (hematite) was formed in the film. In addition, the O2 / H2O molecules in the furnace atmosphere must also diffuse through the surface film to contact with Cr / Si inside the material. Therefore, compared with the heat-treated samples in the conversion gas reduction furnace, the selective oxidation reaction speed is reduced and the number of spherical oxides inside is reduced.
The oxidation / reduction of 2.3cr-0.9si-0.3mo steel in carburizing process was compared and analyzed in two heat treatment equipments with different CO / CO2 partial pressure ratio. The analysis shows that due to the high content of Cr in the material, the oxidation reaction in the carburizing process is accelerated in both equipment, and the formation of spinel structure (Fe, Cr) 3O4 oxide is confirmed. Especially in the drop type oxidation furnace, Fe2O3 is stable due to the low partial pressure of CO / CO2. It can be confirmed that the (Fe, Cr) 3O4 spinel formed in the early stage is oxidized continuously, and finally the surface oxidation film of fe2o3-fe3o4 (Fe, Cr) 3O4 layered structure is formed.
On the other hand, due to the high partial pressure of CO / CO2, Fe3O4 maintains the state of (Fe, Cr) 3O4 in a stable reformer gas reduction furnace. On the contrary, O2 / H2O diffuses into the material, and selective oxidation makes the intercrystalline oxidation of Cr / Si spherical oxide and SiO2 clear.