Adjust the synchronous speed of the motor so that the speed of the motor under rated load can be increased from 500 R / min to 1100 R / min within 70 s. In order to eliminate the influence of external excitation on the simulation results, the roller load used in this section is a constant load, that is, the load fluctuation coefficient is 0.
Fig. 1 is the time domain curve of the dynamic meshing force of gear pair 1 in the process of speed increase. It can be seen that the fluctuation amplitude changes with the cutting motor speed. In order to compare the change of the dynamic meshing force before and after the coupling rocker box, the envelope of the dynamic meshing force of each gear pair in the speed-up process is extracted, as shown in Figure 2 As shown in the figure, three main phenomena can be observed: 1) in the non resonant region, there is no obvious difference in the envelope amplitude before and after the coupling rocker box; 2) in the resonant region, the resonance speed decreases obviously after the coupling rocker box; 3) in the same transmission system, the common vibration speed of different gear pairs is different.
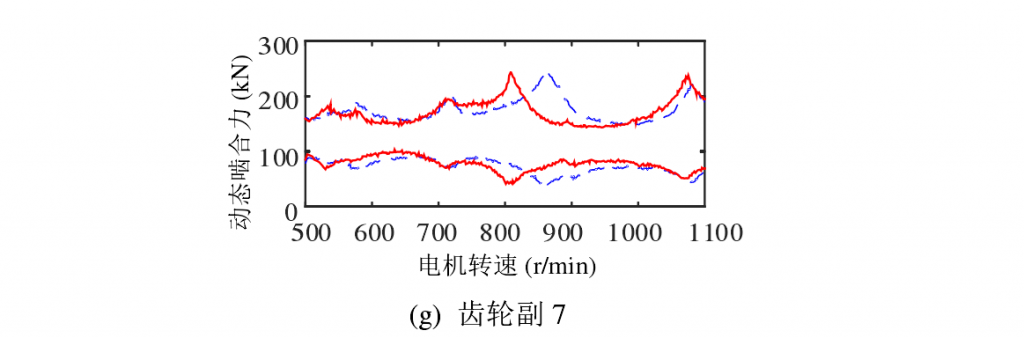
(Blue:without the housing; Red:with the housing)
First, in the non resonance region, the fluctuation amplitude of the dynamic meshing force of each gear pair before and after the coupling rocker box is not obvious. This is because the torsional vibration of gear is the direct cause of dynamic meshing force, and the connecting bearing of multi-stage gear transmission and rocker arm box has no constraint in the torsional direction. It should be noted that even in the resonance region, there is little difference in the amplitude of the dynamic engagement force between the front and back of the coupling rocker box, which is roughly equivalent to the translation of the resonance peak on the abscissa.
Second, in the resonance region, the resonance speed decreases obviously after coupling the rocker box. Before coupling the rocker box, the gear pair 3 ~ 7 has a resonance speed of 861 R / min; after coupling the rocker box, the resonance speed of gear pair 3 ~ 7 is reduced to 810 R / min. This is because the natural frequency of the torsional vibration mode of the transmission subsystem will be reduced after coupling the rocker box, so the resonance speed in the process of speed up will also be reduced. Figure 3 shows the dynamic meshing force of gear pair 4 when the cutting motor is about 810 R / min. at this speed, the meshing frequency of gear pair 4 is 156.4 Hz, which is close to the 11th natural frequency 164 Hz of the coupling system, thus causing torsional resonance of the transmission subsystem of the coupling system. Spectrum analysis shows that the main frequency component of dynamic engagement force is 157 Hz. It should be noted that the resonance frequency screened by the acceleration process is slightly less than the natural frequency of the coupled system modal analysis, which is due to the tooth surface separation in the dynamic simulation process, which will lead to the reduction of the natural frequency of the system. Figure 4 shows the dynamic meshing force of gear pair 4 when the cutting motor is about 861 R / min. at this speed, the meshing frequency of gear pair 4 is 166.3 Hz, which is close to the 9th natural frequency of multistage gear drive (uncoupled rocker box) of 169 Hz, thus causing torsional resonance of multistage gear drive. Spectrum analysis shows that the main frequency component of the dynamic engagement force is 166 Hz. Similarly, due to the effect of tooth surface separation, the resonant frequency identified by the acceleration process is slightly less than the natural frequency of modal analysis of multi-stage gear transmission.
Thirdly, in the same transmission system, the resonance speed of different gear pairs is different. As shown in Figure 2, the dynamic meshing force of gear pair 3 ~ 7 has obvious resonance peak when the cutting motor speed is 810 R / min, while the dynamic meshing force of gear pair 1 ~ 2 has no obvious resonance peak at this speed (the resonance peak of gear pair 2 appears at 1074.0 R / min). According to the meshing frequency analysis in the previous section, when the cutting motor speed is 810 R / min, the 11th mode of the coupling system is excited. As shown in Figure 5, the strain energy of the 11th mode is mainly distributed in the rocker box, gear shaft and meshing pair, and the strain energy of meshing pair is mainly distributed in gear pair 3 ~ 7, which indicates that gear pair 3 ~ 7 is the resonant component of this mode. Therefore, when the torsional resonance of gear pair 3 ~ 7 is around 810 R / min, gear pair 1 ~ 2 of the same transmission system does not show obvious resonance. It shows that the resonance component is as important as the resonance speed, and the selection of monitoring points affects the judgment of whether the transmission system is resonant or not.