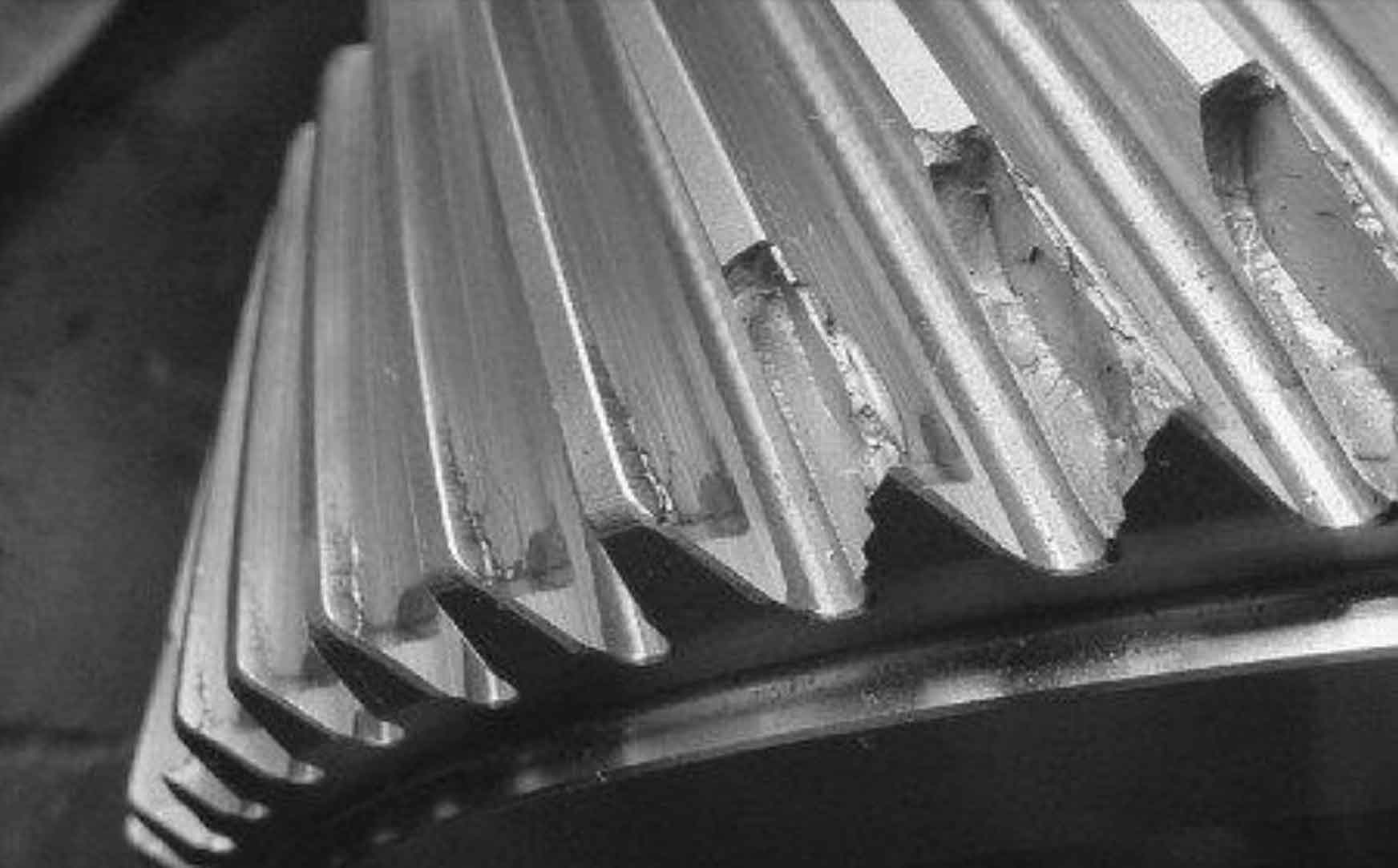
L. Cular and other scholars proposed a theoretical model for predicting the bending fatigue life of carburized helical gears steel based on the strain life method for low cycle fatigue and high cycle fatigue. Using the mixed rule to obtain the average cyclic stress-strain curve of carburized specimens. A method was proposed to convert axial fatigue data into bending fatigue data using Neuber’s rule and correction factors.
Based on the experimental results of two samples with different carburization depths in the literature, the analytical model was preliminarily validated. There is a good correlation between the predicted data of the two types of specimens and the experimental data, with almost all data points falling within a 3-fold range. A prediction model for predicting the bending fatigue failure location and required number of cycles of surface hardening helical gears was proposed. The elastic-plastic material behavior was corrected for the linear elastic stress and strain in the single tooth bending fatigue test. Determine the fatigue performance of each layer through the hardness method. Based on the multi axis fatigue criterion, the fatigue failure location and corresponding fatigue life were predicted. The predicted fatigue life, failure location, and fatigue transition from surface to subsurface are in good agreement with experimental results. Subsequently, a prediction model for the bending fatigue failure location and number of cycles of surface hardening helical gears was proposed based on finite element analysis. Import the linear elastic stress and strain obtained from finite element simulation into the fatigue model. The observed bending fatigue life of the tooth root zone was estimated based on the multi-layer method, hardness method, and strain life method. Due to non proportional loading, the critical plane method is adopted. The prediction results were validated for accuracy through experiments.
S. Rajesh and other scholars proposed a method for predicting the bending fatigue life of new transmission gears. Based on a new type of tooth thickness factor for rack and pinion cutters, an analytical equation was developed for helical gears, and the principal stress and strain at the critical root fillet of the helical gears teeth were estimated through finite element analysis. Using the fatigue module in COMSOL Multiphysics software, the bending fatigue life is determined using the strain life method based on Smith Watson Topper and Neuber rules, as well as the fatigue usage factor based on the Findley criterion. Taking a new type of helical gears as the research object, the effects of helical tooth angle, pressure angle, number of teeth, transmission ratio, tooth top height, and tooth top correction coefficient on bending fatigue life were calculated for different tooth thickness factors of rack cutters. Finally, through the study of the above parameters, the optimal tooth thickness factor between the helical gears and the small gear was obtained to achieve a balanced bending fatigue life, which helps to improve the power transmission capacity of the helical gears transmission.
Scholars such as Franco Concil have questioned the assumption that the correction coefficient fkorr for single tooth bending fatigue tests can be independent of the material, geometric shape, and loading conditions of helical gears. They have proposed a calculation method for the fkorr coefficient by combining numerical simulation with multi axis fatigue criteria. The method was validated using helical gears with different geometric shapes and material properties, and the results showed that fkorr varied with the geometric characteristics of the helical gears, material fatigue strength, and the load ratio set in the single tooth bending fatigue test. Next, single tooth bending fatigue tests were conducted on two types of helical gears geometries, and different fractured helical gears samples were measured (crack location and direction) as a reference. A numerical simulation was conducted on the single tooth bending fatigue test structure through finite element analysis. The comparison between numerical simulation results and experimental results shows that Findley, Matake, McDiarmid, Papadopoulos, and Susmel fatigue criteria are consistent in determining the most critical point, and the Findley criterion is the most accurate for determining the direction of early crack propagation.
L. Bonaiti and other scholars studied the effects of different load conditions on single tooth bending fatigue tests and meshing helical gears. These studies indicate that in order to make the results of single tooth bending fatigue tests applicable to the design of meshing helical gears, differences in load path ratios result in a reduction of approximately 10% in the ultimate force of surface hardened helical gears obtained through single tooth bending fatigue tests. If it is also necessary to consider the impact of different load ratios R, a higher reduction rate of about 17% is required. A statistical method has been proposed to more accurately estimate the bending fatigue limit, which is used to analyze single tooth bending fatigue test data and reference it to helical gears specimens in meshing state. Use maximum likelihood estimation and extreme value statistics to estimate the SN curve of helical gears with a failure probability of 1%. Starting from the assumption that the failure of helical gears caused by root bending fatigue is determined by their weakest teeth, and based on the cumulative distribution function of teeth, the bending fatigue life of helical gears is estimated through extreme value statistics, thus forming the SN curve of helical gears.
Seyit M Demet and Ali S Ersoyoglu designed symmetric and asymmetric root curve gears based on the fatigue performance of AISI 4140 material angle spur gears, utilizing the circular rounded corner profile in the root region. We manufactured asymmetric spur gears designed by applying small changes in pressure angle, and studied their fatigue strength performance under bending stress through single tooth bending fatigue tests. It was found that the use of asymmetric gears can improve fatigue life, while the formation of tooth surface damage has a negative impact on the fatigue performance of gears.
Isaac J. Hong and other scholars have developed an experimental method to evaluate the high cycle tooth bending fatigue life of gears under two loading conditions. A unique sample for tooth bending fatigue and an adaptive diagnostic method for testing termination were designed, while quantifying tooth root strain under high-speed conditions. The effectiveness of the proposed method was verified through gear bending fatigue tests. Afterwards, the study compared the high cycle gear bending fatigue life of spur gears under completely reverse and fully released load conditions. Two sets of rotational gear tooth bending fatigue tests were conducted. Perform statistical analysis to regress the stress life (S-N) curves under two loading conditions. These curves indicate that, compared to gears under fully released loads, gears have a shorter bending life under completely reverse loads at the same maximum root stress. Determine the allowable maximum root stress ratio between the gear components of a P-type planetary gear set, so that each gear in the gear set has the same bending fatigue life, ensuring the longest lifespan of the planetary gear set.
A Karthik Pandian and other scholars conducted bending fatigue tests on symmetric and asymmetric nylon 66 helical gears using an internally developed test bench. The bending fatigue strength of helical gears was determined through experiments, and the influence of load sharing caused by deflection on the bending fatigue life of asymmetric structures was studied. Quasi static simulation was conducted in ABAQUS/Standard to calculate stress distribution and tooth deformation. Finally, the damage morphology of the gear teeth was studied using stereo microscopy and field emission scanning electron microscopy (FESEM). Research has shown that asymmetric tooth profiles enhance bending fatigue strength and can be used in the design of polymer helical gears to prevent bending fatigue failure. In order to investigate the effect of metal and polymer combined with helical gears on the bending fatigue performance of asymmetric polymer helical gears, simulation and experimental methods were used to evaluate the effect of steel and PA66 paired helical gears on the bending fatigue performance of symmetric and asymmetric PA66 helical gears. The results showed that the working temperature of the polymer polymer helical gears pair was higher than that of the steel polymer helical gears pair, which reduced the bending fatigue strength. The bending fatigue performance of the polymer polymer helical gears pair depends on the operating temperature, while the bending fatigue characteristics of the steel polymer pair at the tooth root depend on the maximum bending stress.
Kresimir Vuckovic and other scholars have proposed a bending fatigue life prediction model suitable for surface hardening spur gears. The prediction model includes a gear finite element model and a fatigue failure model, which explain the actual stress-strain state at the tooth root by considering local elastic-plastic corrections. Obtaining the actual bending stress-strain state through elastic-plastic correction based on Neuber rule, and using strain life( ε– N) The method estimates fatigue life, taking into account the influence of adjacent teeth, and proposes a correction factor CATE to correct the bending fatigue life prediction model.
Damijan Zorko and other scholars have conducted a comprehensive study on the tooth bending strength of spur gears (S gears) with progressive bending contact paths. Different material combinations of transmission gears and driven gears were analyzed within a meaningful load range, such as polymer/polymer, steel/polymer, and steel/steel. The discovery of gear profile, material combination of driving and driven gears, and transmitted load are the main parameters affecting the bending stress of gear teeth. Based on the results, shape factors considering the above effects were introduced, and an S-gear root strength calculation model was proposed, and accuracy was verified using finite element method.
Mikiya Yamaoka and other scholars conducted hardness tests, residual stress measurements, and bending fatigue tests on carburized helical gears with large helix angles. By comparing the experimental results, the effects of helix angle, meshing position, and carburization on the bending fatigue strength of helical gears were quantified. It was found that the surface carburization of large helix angle helical gears may form an excessive hardening layer near the wide end of the sharp tooth, which has an adverse effect on the bending fatigue strength.
Eduardo Conrado and other scholars tested the bending fatigue strength of two surface hardened and three nitrided helical gear steels through single tooth bending fatigue tests to determine the effect of steel and thermochemical treatment combination on the bending fatigue strength. Accurate X-ray measurements were conducted to determine the residual stress changes caused by different combinations of steel and thermochemical treatment. The correlation between the experimental results and residual stress indicates that both carburization and nitriding can generate favorable residual stress conditions, which have a significant impact on the bending fatigue strength. Through comparison, it is concluded that the bending fatigue performance of nitrided helical gears has a high competitiveness.