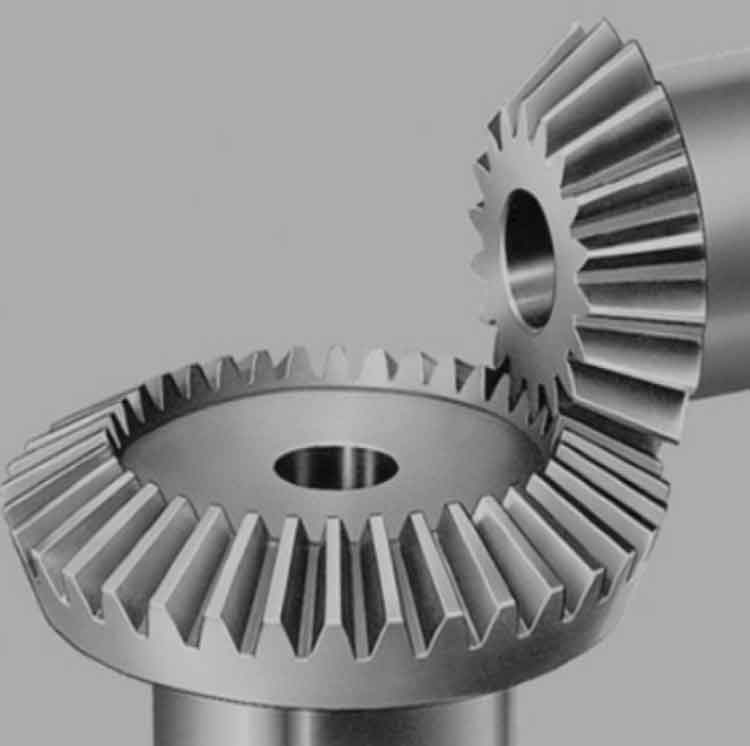
Customizing straight bevel gears for specialized industrial needs involves tailoring the gear design and manufacturing process to meet specific application requirements. By understanding the unique demands of the industrial application, engineers can optimize the gear’s performance, durability, and efficiency. Here’s a step-by-step guide on how to customize straight bevel gears for specialized industrial needs:
1. Requirements Analysis:
- Understand the specific industrial application’s requirements, including torque, speed, operating conditions, and space constraints.
- Identify any unique challenges or environmental factors that may affect gear performance.
2. Gear Design and Engineering:
- Use computer-aided design (CAD) software to create a customized gear design that aligns with the application’s requirements.
- Tailor gear parameters, such as pitch diameter, number of teeth, pressure angle, and module, to meet the specific needs.
3. Material Selection:
- Choose the appropriate material based on the application’s demands, such as high-strength alloy steel, stainless steel, or other specialty materials.
- Consider factors like hardness, wear resistance, and heat treatment capabilities.
4. Gear Cutting and Manufacturing:
- Select the most suitable gear cutting method based on the gear’s size and complexity, such as gear hobbing, gear shaping, or gear milling.
- Utilize CNC machining and precision manufacturing techniques to ensure accurate gear tooth profiles and surface finish.
5. Tooth Profile Optimization:
- Analyze tooth contact patterns and adjust the tooth profile if needed to improve load distribution and minimize noise.
- Implement profile modifications, such as crowning or tip relief, for enhanced performance.
6. Heat Treatment and Surface Finishing:
- Apply appropriate heat treatment processes to achieve the desired hardness and mechanical properties.
- Perform surface finishing, such as grinding or lapping, to ensure smooth tooth surfaces and reduce friction.
7. Lubrication and Sealing:
- Consider the gear’s lubrication requirements and choose suitable lubricants to reduce wear and friction.
- If required, incorporate effective sealing to protect the gear from contaminants and ensure reliable operation.
8. Testing and Quality Control:
- Conduct thorough testing and inspections to validate gear performance and verify that it meets the specified requirements.
- Implement quality control measures throughout the manufacturing process to ensure consistency and reliability.
9. Application-Specific Customizations:
- Implement any additional customizations or features specific to the industrial application, such as mounting provisions or integrated bearings.
10. Continuous Improvement:
- After deployment, monitor gear performance and gather feedback to identify opportunities for further optimization and continuous improvement.
Customizing straight bevel gears for specialized industrial needs involves collaboration between gear designers, manufacturing experts, and application engineers. By tailoring gear specifications and manufacturing processes to the unique requirements, custom bevel gears can provide enhanced performance, durability, and reliability in demanding industrial applications.