Hypoid gears are a specific type of gears widely used in various applications, especially in the automotive and mechanical power transmission industries. They offer unique design characteristics and advantages over other gear types, making them suitable for specific applications. In this explanation, we will delve into the design principles, features, and applications of hypoid gears.
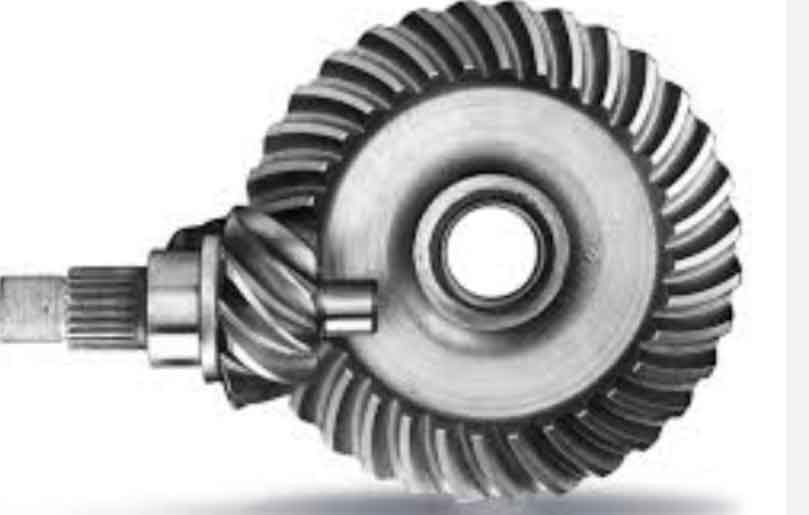
1.Gear Design:
Hypoid gears are a type of spiral bevel gears, which are similar to straight bevel gears but have the pinion offset from the gear’s axis. This offset creates a hypoid shape, resulting in the distinctive curved teeth. The pinion and gear have different curvatures, enabling smooth and efficient power transmission with high torque capacity.
2.Tooth Geometry:
The teeth of hypoid gears have both radial and axial curvatures. The radial curvature corresponds to the pitch cone diameter, while the axial curvature determines the gear’s offset from the axis. These curvatures enable gradual tooth engagement and minimize sliding friction, resulting in reduced noise, vibration, and wear.
3.Contact Pattern:
The contact pattern of hypoid gears differs from that of other gear types. It is characterized by a larger contact area, which provides increased load-carrying capacity and improved durability. The contact pattern is influenced by factors such as gear tooth geometry, backlash, and lubrication.
4.Torque Transfer:
Hypoid gears are particularly suitable for transmitting high torque between non-intersecting and non-parallel shafts. The offset design allows the gear axes to intersect, enabling power transmission in applications where space limitations or shaft misalignment is a concern.
5.Efficiency:
Hypoid gears typically have lower efficiency compared to parallel shaft gears due to the sliding friction between the gear teeth. However, advancements in design, manufacturing, and lubrication have significantly improved their efficiency over the years.
6.Noise and Vibration:
The offset design of hypoid gears results in sliding action between the teeth, which can generate more noise and vibration compared to parallel shaft gears. Nevertheless, careful design and manufacturing techniques can minimize these effects, making hypoid gears suitable for noise-sensitive applications.
7.Lubrication:
Proper lubrication is critical for the performance and durability of hypoid gears. Due to the sliding motion, hypoid gears require lubricants with high film strength and anti-scuffing properties to reduce friction and prevent wear. Gear oils specifically formulated for hypoid gears are commonly used.
Applications:
Hypoid gears find applications in various industries, including:
- Automotive: They are extensively used in vehicle drivetrains, especially in rear-wheel-drive and four-wheel-drive systems. Hypoid gears efficiently transmit power between the engine and the wheels, accommodating the offset between the propeller shaft and the rear axle.
- Industrial Machinery: Hypoid gears are employed in heavy-duty machinery, such as construction equipment, mining machinery, and agricultural machinery, to transfer power between non-parallel and non-intersecting shafts.
- Power Transmission: They are utilized in gearboxes and speed reducers, where the input and output shafts require torque transfer at an angle. Hypoid gears provide a compact and efficient solution for transmitting power in these applications.
- Robotics: Hypoid gears can be found in robotic systems that require high torque transmission between non-parallel shafts, such as robotic arms or joint mechanisms.
Hypoid gears are a specialized type of spiral bevel gears designed for high torque applications with non-parallel and non-intersecting shafts. Their unique tooth geometry, contact pattern, and offset design enable efficient power transmission and high torque capacity. While they may generate more noise and have slightly lower efficiency compared to parallel shaft gears, proper design, manufacturing, and lubrication techniques can mitigate these concerns. Hypoid gears have widespread applications in automotive, industrial,