Abstract
This article focuses on the design and analysis of helical gear modification in an aero gearbox using KISSsoft software. By selecting appropriate modification methods, the meshing performance and contact characteristics of the gears before and after modification were thoroughly investigated. The primary parameters analyzed include tooth strength, transmission error, tooth surface load distribution, and sliding ratio. The results demonstrate that proper modification of inclined gears can significantly enhance the endurance capacity, improve meshing performance, and mitigate issues such as excessive loading at the tooth tip and root, as well as load mutations. Consequently, the overall meshing quality is enhanced. Furthermore, a comparative analysis with the actual gear contact patterns validates the reliability and effectiveness of KISSsoft’s analysis results.
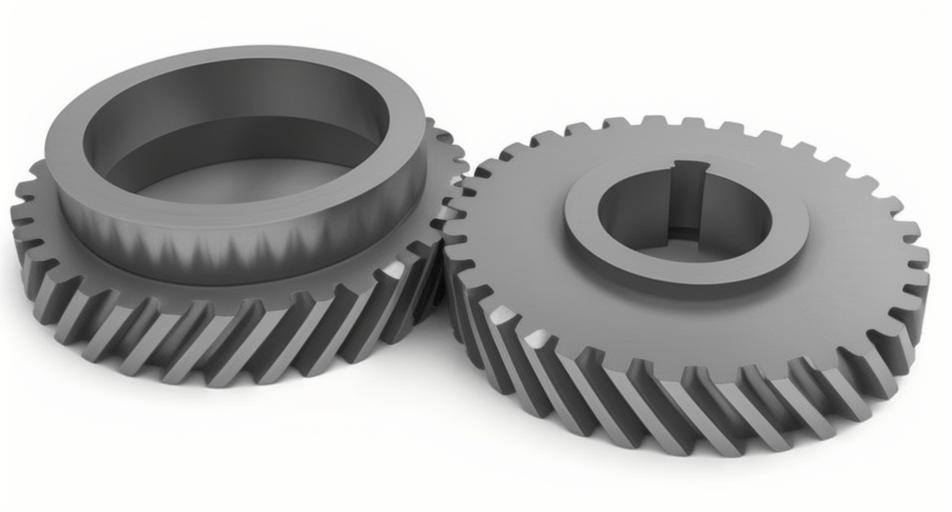
Introduction
Aeronautical gear transmissions are evolving towards higher speeds and heavier loads, making them a crucial component in various power systems. Consequently, the meshing performance of gears has garnered significant attention, leading to the emergence and widespread adoption of numerous optimization techniques in gear transmission design. Over half a century of rapid advancements, tooth modification has emerged as a core technology for reducing gear vibrations and enhancing transmission smoothness, particularly in high-speed systems such as aerospace vehicles, engines, and helicopter gearboxes.
Tooth modification primarily encompasses two forms: tooth profile modification and tooth lead modification. The former involves removing the interfering portions during gear contact, which can be achieved by modifying the tooth tips of both gears or selectively modifying one gear’s tooth tips and roots. This approach mitigates the impact of base pitch errors and elastic deformations under load, thus reducing meshing-in and meshing-out shocks and improving lubrication conditions. Meanwhile, tooth lead modification addresses uneven load distribution across the tooth width, eliminating the phenomenon of edge contact and enhancing gear load capacity.
With the rapid advancements in computer technology, KISSsoft, a specialized software for transmission system design and analysis, has been extensively employed by designers and researchers to optimize gear designs and conduct related analyses. KISSsoft’s robust computational simulation capabilities and parametric optimization functions in the field of gear design facilitate cost savings and shortened development cycles for gearbox components, including helical gears in aero gearboxes.
This article presents an in-depth analysis of helical gear modification in an aero gearbox using KISSsoft software. The findings confirm that appropriate gear modification can enhance load-bearing capacity and improve meshing performance, which are validated through comparisons with actual gear contact patterns.
1. Evaluation Metrics for Gear Modification Optimization
1.1 Tooth Strength
The failure modes of gears primarily include pitting corrosion, tooth fracture, tooth surface wear, and plastic deformation. Enhancing the reliability of aero gearbox transmissions necessitates rigorous stress analysis and strength verification to ensure the gears meet lifespan requirements. Specifically, tooth surface contact strength, which prevents pitting corrosion, is a crucial indicator of a gear pair’s suitability for extended use. Pitting corrosion occurs due to fatigue in the gear material under cyclic contact stresses, particularly in well-lubricated enclosed gears, as seen in aero gearboxes. The tooth root bending strength, reflecting a gear’s resistance to bending, signifies the maximum stress the gear can withstand under bending loads without fracturing or reaching the specified bending moment.
1.2 Transmission Error
Transmission errors arise due to manufacturing and assembly inaccuracies, as well as elastic deformations under load, causing the driven gear to rotate asynchronously with the driving gear. This asynchronous rotation is defined as the transmission error, with its peak-to-peak value inversely correlated with the smoothness of the transmission process. Therefore, a smaller peak-to-peak transmission error indicates more stable transmission.
1.3 Tooth Surface Load Distribution
The tooth stress curve illustrates the load distribution across the gear pair during meshing. In gear transmission systems, manufacturing and installation errors, along with deformations under load, often result in uneven load distribution, stress concentrations, and load mutations, diminishing the gears’ load-bearing capacity. To satisfy the lifespan requirements, it is imperative to effectively control the load distribution on the tooth surface, eliminating load mutations, edge loading, and stress concentrations.
1.4 Sliding Ratio
The sliding ratio impacts the transient effects of elastohydrodynamic lubrication, is a critical factor in determining gear wear, and directly influences the magnitude and direction of the friction torque between gear pairs. To enhance the gear transmission system’s resistance to pitting corrosion and wear, while ensuring comparable wear rates across gear roots, the sliding ratio must be constrained. Ideally, a sliding ratio within -1 to 1 indicates optimal gear operation, while values between -2 to 2 indicate good operation.
2. Helical Gear Modification Analysis and Optimization with KISSsoft
In the field of aero-engine design, helical gears play a crucial role in ensuring smooth and reliable transmission, especially in high-speed and heavy-load applications. The proper modification of helical gears can significantly improve their performance, longevity, and overall system efficiency. This section discusses the utilization of KISSsoft software for analyzing and optimizing the modification of helical gears in an aerospace gearbox.
2.1 Advantages of Helical Gear Modification
Helical gears are preferred over spur gears in high-performance applications due to their better load-sharing capabilities and smoother operation. However, even helical gears experience issues such as load concentration, wear, and vibration under extreme conditions. Gear modification, particularly tooth profile and tooth lead modifications, addresses these issues by optimizing the gear geometry to mitigate contact stresses and uneven load distribution.
2.2 KISSsoft Software for Gear Design and Analysis
KISSsoft is a comprehensive software tool widely used for designing and analyzing gear systems. It offers powerful simulation capabilities and parameter optimization features, making it an ideal choice for engineers involved in aero-engine and transmission system design. By using KISSsoft, engineers can quickly assess the impact of different gear modifications on critical parameters such as tooth strength, transmission error, tooth surface load distribution, and sliding ratio.
2.3 Optimization Process Using KISSsoft
The optimization process begins by defining the basic parameters of the helical gear pair, including the number of teeth, module, pressure angle, helix angle, and gear width. Once the baseline configuration is established, KISSsoft simulates the gear’s performance under various loading conditions. This analysis reveals areas of potential improvement, such as high contact stresses or uneven load distribution.
2.4 Modification Strategy
Based on the simulation results, a modification strategy is devised. For tooth profile modification, KISSsoft utilizes standard formulas that consider factors like the end-face contact ratio, working conditions, and tooth stiffness. Similarly, tooth lead modifications are applied to optimize the load distribution along the tooth width, minimizing edge contact and improving overall performance.
2.5 Evaluation of Modification Results
After implementing the modifications, KISSsoft conducts a new simulation to assess their effectiveness. The key metrics evaluated include:
- Tooth Strength: Both tooth surface contact strength and tooth root bending strength are analyzed to ensure the gear meets the required durability standards.
- Transmission Error: A reduction in the transmission error indicates smoother and more reliable gear meshing, leading to reduced noise and vibration.
- Tooth Surface Load Distribution: Even load distribution across the tooth surface is crucial for avoiding edge contact, reducing wear, and improving fatigue resistance.
- Sliding Ratio: Constraining the sliding ratio within optimal ranges (-1 to 1 for best performance, -2 to 2 for good performance) ensures minimal wear and balanced friction torque between gear pairs.
2.6 Validation and Confirmation
Finally, the modified gear design is validated through experimental testing or by comparing the simulated contact patterns with actual gear meshing marks. The results obtained from KISSsoft have been proven to be reliable and effective, providing a solid foundation for making informed design decisions.
In conclusion, the use of KISSsoft software in helical gear modification design not only enhances the gears’ performance but also streamlines the design process, saving time and resources. By carefully optimizing the tooth profile and tooth lead modifications, engineers can significantly improve the durability, efficiency, and overall transmission quality of aerospace gearboxes.