Abstract:
This paper presents the design and analysis of a specialized fixture used for the meshing inspection of straight bevel gears. Straight bevel gears, being critical mechanical components, transmit torque through intermeshing tooth profiles. Unlike straight cylindrical gears, bevel gears offer flexibility in shaft angles, improved operational stability, and higher torque transmission capabilities. However, achieving optimal meshing between paired bevel gears necessitates rigorous pre-assembly inspection. This paper discusses the development of a custom-designed fixture that facilitates pre-assembly inspection of various meshing parameters such as backlash, tip clearance, contact patterns, and more. The fixture design, operation procedure, key parameters, and its application range are elaborated upon, along with a detailed analysis of the meshing behavior of straight bevel gears.
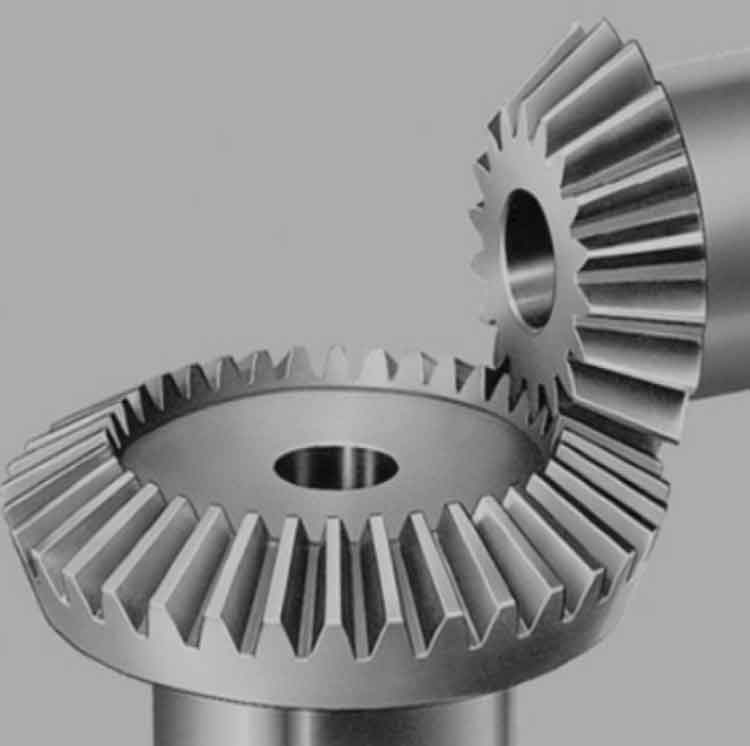
1. Introduction
Straight bevel gears are essential components in various mechanical systems, particularly those involving angular power transmission. Their ability to transmit torque at any angle between 0° and 90° makes them invaluable in numerous industrial applications. However, achieving proper meshing between paired bevel gears is crucial for ensuring smooth operation, efficiency, and longevity. Improper meshing can lead to increased wear, vibration, and even failure of the entire system.
Traditional single-piece inspection methods for bevel gears focus on parameters like tooth profile, common normal length, tooth thickness, and tooth height. However, critical meshing parameters such as backlash, tip clearance, and contact patterns can only be assessed accurately when the gears are paired and inspected as a unit. This paper discusses the design and analysis of a specialized fixture designed specifically for this purpose.
2. Product Introduction and Background
Our company, as one of the leading manufacturers of rubber and plastic machinery in China, produces various equipment, including mixers, twin-screw extruders, plate vulcanizers, and tire curing presses. The focus of this study is on the straight bevel gears used in the twin-screw extruder, specifically the 416 model. These gears feature 48 teeth, a pressure angle of 20°, a cone angle of 7°, and a module of 20 mm at the large end. The design common normal length is 338.14 mm, with an assembly backlash of 0.5 mm.
During the assembly process, it was observed that paired bevel gears often exhibited uneven backlashes at the large and small ends, leading to insufficient contact along the tooth width. This resulted in uneven wear and reduced operational efficiency. Consequently, the design of a specialized fixture for pre-assembly meshing inspection became imperative.
3. Fixture Design
The designed fixture aims to facilitate the inspection of straight bevel gears in a paired configuration, allowing for the assessment of critical meshing parameters. Figures 2 and 3 illustrate the three-dimensional and plan views of the fixture, respectively.
Table 1: Key Components of the Fixture
Component No. | Component Name | Description |
---|---|---|
1 | Base | Supports the entire fixture |
2 | Rails | Guides the movement of the support structure |
3 | Sliders | Facilitates linear movement along the rails |
4 | Mounting Plate | Provides a mounting surface for other components |
5 | Pin Shaft | Enables rotational adjustment of fixed blocks |
6 | Support Frame | Holds the bevel gears in place |
7 | Fixed Blocks | Supports and positions the bevel gears |
8 | Spacer Sleeves | Adjusts the distance between gears |
9 | Support Bolts | Adjusts the cone angle of the gears |
10 | Round Nuts | Secures the components in place |
11 | Spacer Rings | Maintains gear spacing |
12 | Tapered Roller Bearings | Supports the rotational motion of the gears |
13 | Thrust Roller Bearings | Supports axial loads |
14 | Mounting Shaft | Mounts and rotates the bevel gears |
15 | Keys | Prevents relative rotation between gears and shaft |
16 | Straight Bevel Gears | The gears under inspection |
4. Fixture Operation Procedure
The fixture operation involves a step-by-step process to ensure precise and repeatable meshing inspections. The following steps outline the procedure:
- Prepare the Fixture: Ensure the fixed blocks are in the horizontal position before installing the bevel gears.
- Install the Bevel Gears: Apply lubricant to the gear bores to facilitate easy installation and removal. Modify the mounting shaft diameter to ensure a clearance fit with the gear bore for smooth installation.
- Secure the Gears: Install the keys to prevent the gears from rotating freely on the mounting shaft.
- Check and Tighten Components: Verify the pre-tightening of the round nuts to secure the bearings and prevent any loosening during operation.
- Adjust the Cone Angle: Using the support bolts, rotate the fixed blocks around the pin shaft to achieve the desired cone angle, as per the gear design specifications.
- Align and Mesh the Gears: Slide the support frame along the rails to bring the bevel gears into mesh.
- Lock the Position: Secure the sliders to prevent any unintended movement during inspection.
- Operate the Gears: Use the hexagon socket on the mounting shaft end to manually rotate the gears and inspect the meshing parameters.
5. Key Parameters and Application Range
The designed fixture boasts a comprehensive set of technical specifications tailored to meet the diverse needs of straight bevel gear inspection.
Table 2: Key Parameters of the Fixture
Parameter | Value |
---|---|
Overall Dimensions | 2000 mm x 1020 mm x 1300 mm |
Applicable Gear Types | Straight cylindrical, straight bevel |
Adjustable Cone Angle Range | 0° to 20° |
Gear Diameter Range | 800 mm to 1200 mm |
Maximum Gear Weight Capacity | 5 tons per gear |
6. Meshing Analysis of Straight Bevel Gears
The meshing behavior of straight bevel gears is influenced by several factors, with cone distance and cone angle being the most significant.
6.1 Cone Distance
Cone distance determines the axial position of the paired gears, similar to the center distance in cylindrical gears. However, unlike cylindrical gears where centers are parallel, bevel gears have centers at an angle. Adjusting the cone distance can modify the backlash, with a smaller distance reducing backlash and vice versa, but only when the cone angles of the paired gears are identical.
6.2 Cone Angle
The cone angle determines the angle between the gear center and the tangent to the pitch circle, directly impacting the contact pattern area and hence the torque transmission efficiency. Four primary meshing scenarios can arise based on the cone angle:
- Ideal Meshing: Complete elimination of backlash, though practically unachievable due to manufacturing tolerances and risk of seizure.
- Parallel Meshing: Zero backlash at the meshing faces with controlled backlash at non-meshing faces, adjustable through spacer sleeve widths.
- Excessive Cone Angle: Smaller backlash at the small end and larger at the large end, leading to partial contact and accelerated wear.
- Insufficient Cone Angle: Larger backlash at the small end and smaller at the large end, again resulting in partial contact and premature wear.
7. Conclusion
The design and analysis of the straight bevel gear meshing fixture presented in this paper underscore the critical importance of pre-assembly inspection for optimal gear performance. By facilitating the paired inspection of bevel gears, the fixture enables accurate assessment of backlash, tip clearance, contact patterns, and other critical meshing parameters. The adjustable cone angle and comprehensive technical specifications ensure that the fixture caters to a wide range of gear sizes and types.
In conclusion, the designed fixture not only enhances the quality control process during gear assembly but also contributes to improved operational efficiency and extended gear lifespan. Future work could involve integrating automated inspection systems and advanced sensors to further streamline the process and enhance inspection accuracy.