According to the above tooth profile generation method, the tooth profile calculation software of eccentric modified gear is designed in Matlab environment.
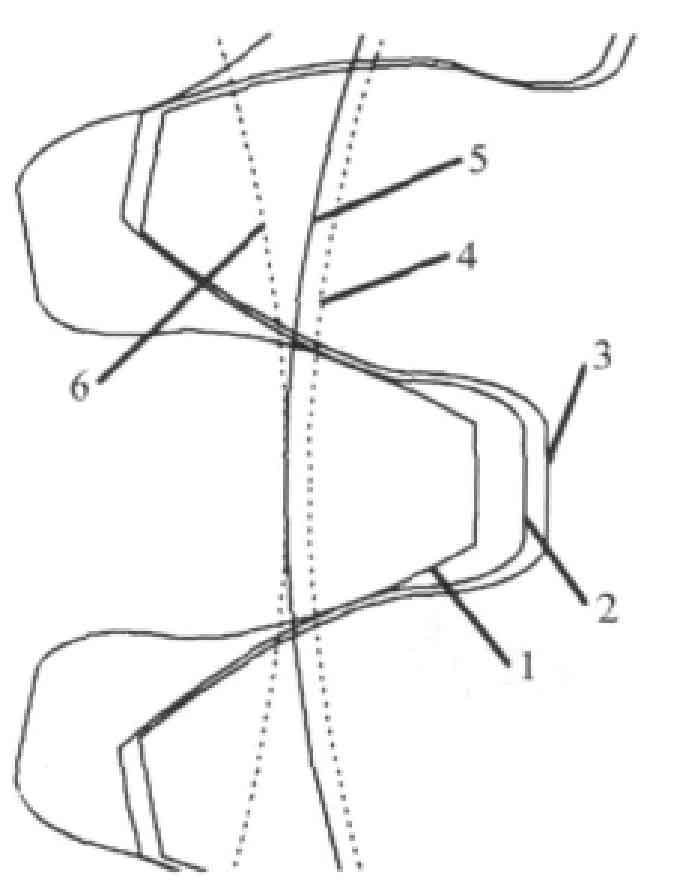
The program consists of interface display, undercut discrimination, gear parameter calculation, tooth profile envelope, intersection calculation, feature point sorting, data output and so on. Taking the gear in the eccentric displacement planetary system transplanting mechanism as an example, the correctness of the eccentric displacement gear design is verified. It is known that the number of teeth of eccentric gear z = 17, modulus M = 2.5 mm and eccentricity e = 3.5 mm. The axial distance a of eccentric gear and conjugate gear is 42.8 mm. The generated gear profile is shown in Figure 1.
Fig. 2 is a comparative enlarged view of eccentric gear meshing with eccentric gear and eccentric displacement gear respectively. As can be seen from the figure, there is side clearance when the two eccentric gears 1 and 3 mesh, while there is no side clearance when the eccentric gear 1 and the eccentric displacement gear 2 mesh. In the initial position, the pitch curves of the two eccentric gears are separated, and the pitch curves of the eccentric gear and the eccentric displacement gear are tangent. In the whole meshing process, the pitch curves of the two eccentric gears sometimes separate and sometimes intersect, and are only tangent at some specific points, which also proves that the assumption that the two pitch curves are always tangent and pure rolling is not tenable, so there is tooth side clearance when the two gears mesh. The pitch curve of eccentric gear and eccentric displacement gear is always tangent and pure rolling, meshing without tooth side clearance.
In order to ensure the formation of lubricating oil film between gear tooth surfaces and prevent the gear from jamming due to thermal expansion and deformation, there must be appropriate tooth side clearance during gear pair meshing. The tooth side clearance is guaranteed by manufacturing tolerance, and it is still designed according to meshing without tooth side clearance during design. In this example, the tooth side clearance of eccentric gear mechanism and eccentric displacement gear mechanism is shown in Figure 3. It can be seen that the tooth side clearance of the eccentric modified gear mechanism generated by the modification method is zero, and the meshing without tooth side clearance is realized.
By improving the material ratio, increasing the gear thickness and increasing the gear modulus, the strength problem of powder metallurgy gear is solved, the precision is reliable, and the cost is only 1% of that of wire cutting gear. Through the destructive test, the gearbox shell was damaged and the < 19 mm transmission shaft was twisted, and the gear did not have any problems.
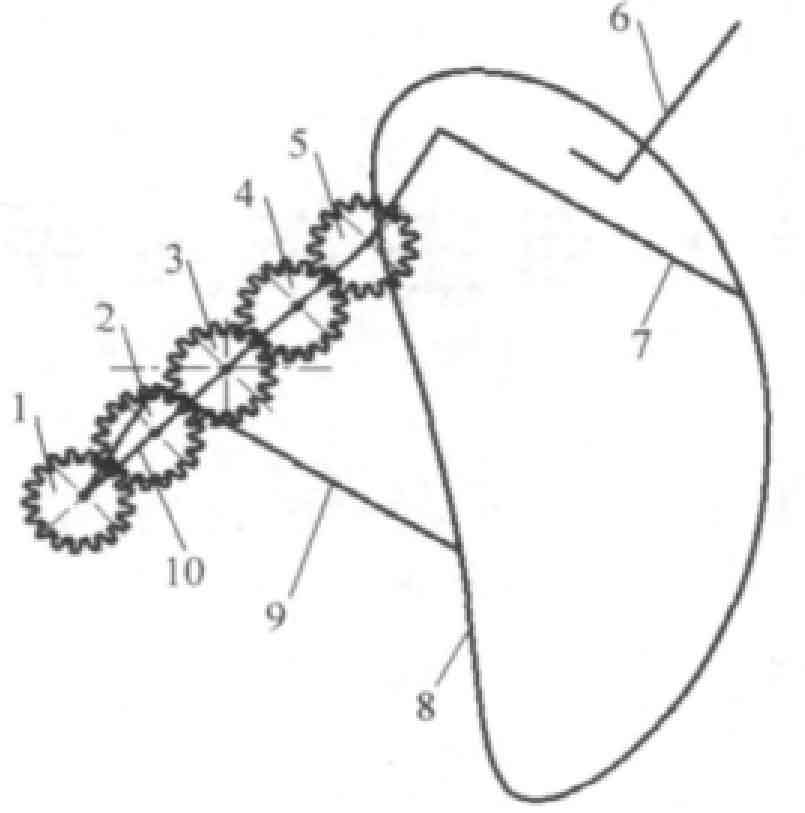
The rotary planetary system transplanting mechanism with eccentric displacement gear is shown in Fig. 4. The transplanting mechanism is composed of three eccentric gears 1, 3 and 5, two eccentric displacement gears 2 and 4, planetary carrier (gear box) 10 and planting arms 7 and 9. 1 and 5 are planetary gears, 3 are sun gears and 2 and 4 are intermediate gears. The non-uniform transmission is realized by meshing the eccentric gear with the eccentric displacement gear, and the appropriate eccentricity and center distance are selected to form the required non-uniform transmission ratio and rotation angle relationship, so as to obtain the “waist shaped” static track 8 that meets the working requirements of the high-speed transplanter. The mechanism is suitable for the requirements of seedling transplanting of different sizes at the same time.
The eccentric displacement gear planetary system transplanting mechanism is applied to the six row wide and narrow row riding transplanter, and the field test is carried out on the transplanter. The test prototype is shown in Fig. 5.
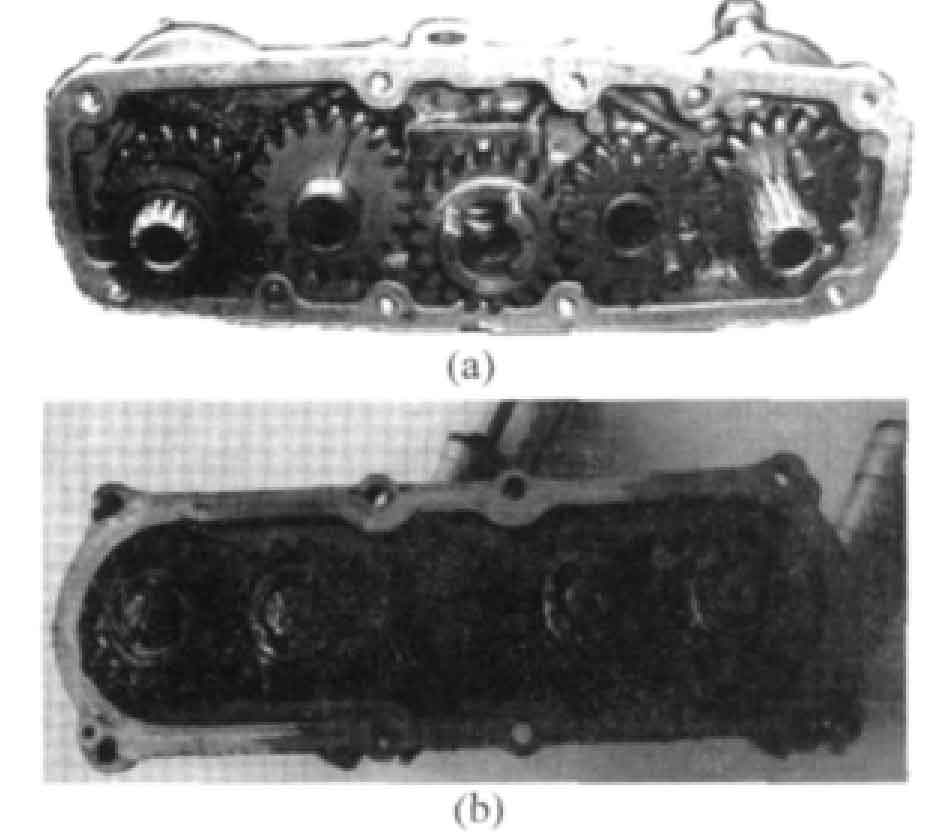
(b) eccentric displacement gear transplanting mechanism
Fig. 6 is a comparison diagram of the inserting and dropping mechanism. Fig. 6A shows the gear box of the Japanese eccentric gear insertion mechanism. The mechanism has 9 eccentric gears with the same radius and eccentricity. The planetary gear and intermediate gear are superimposed by two sheet gears and installed in dislocation. Two locating pins are fixed on two superimposed eccentric thin gears respectively, and the worm coil spring makes the meshing gears close. Fig. 6B shows the gear box of the eccentric displacement gear transplanting mechanism. The eccentric displacement gear transplanting mechanism used in this project only uses 5 gears, simplifying the mechanism.
The test site is Qixing branch of Jiansanjiang farm of Heilongjiang Agricultural Reclamation Bureau. The test plot covers an area of 0.7 Hm2, the mud broken field is flat, and the depth of mud foot is 170 mm. The seedling is raised with seedling tray, the soil is not loose, the seedling needle is coiled, the average height of seedlings is 150 mm, the leaf age is 3 ~ 4 leaves, the width of seedling tray is 300 mm, the soil layer is 19 ~ 21 mm thick, and the soil moisture content is 48%.