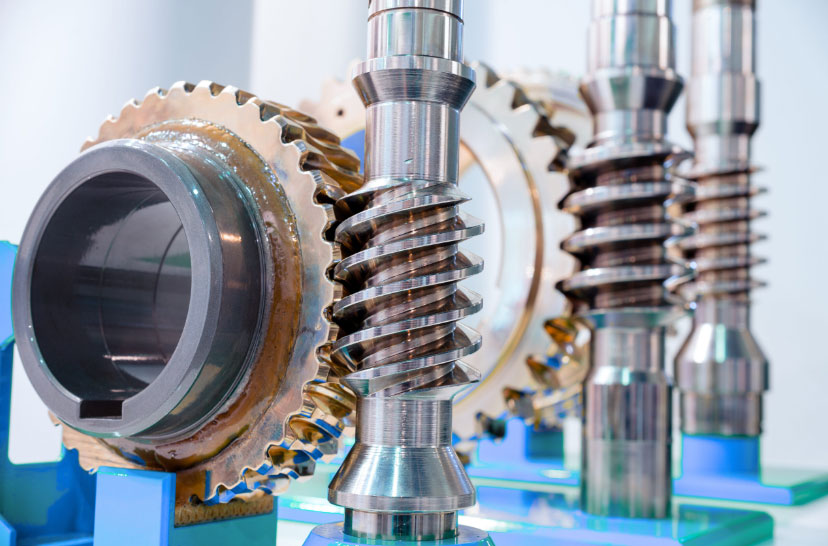
Designing custom worm gears for low-backlash and high-accuracy systems requires careful consideration of several factors, including gear geometry, materials, manufacturing processes, and lubrication. Achieving low backlash and high accuracy is essential for applications where precision motion control is critical, such as robotics, medical equipment, and aerospace systems. Here are some key design considerations to achieve low-backlash and high-accuracy custom worm gears:
1. Gear Geometry:
- Optimize the helix angle and lead angle to achieve smooth tooth engagement and minimize sliding friction. Higher helix angles can help reduce sliding friction and improve efficiency.
- Ensure proper center distance between the worm and gear to minimize meshing clearances and backlash.
2. Tooth Profile and Manufacturing:
- Use precision manufacturing techniques, such as CNC machining and gear grinding, to achieve accurate tooth profiles and tight tolerances.
- Implement advanced gear shaping or hobbing processes to produce high-quality teeth surfaces.
3. Material Selection:
- Choose high-quality and durable materials with excellent wear resistance and dimensional stability to reduce wear and prolong gear life.
- Opt for materials with low coefficient of thermal expansion to maintain accuracy over a wide temperature range.
4. Heat Treatment and Surface Finishing:
- Apply specialized heat treatment processes, such as carburizing or nitriding, to improve the gear’s surface hardness and wear resistance.
- Employ surface finishing techniques, such as polishing or superfinishing, to achieve smoother gear surfaces and reduce friction.
5. Lubrication and Lubricant Selection:
- Optimize the lubrication system for the specific application, considering factors like speed, load, temperature, and operating environment.
- Choose lubricants with high film strength and good adhesion to prevent metal-to-metal contact and minimize wear.
6. Preload and Adjustment Mechanisms:
- Consider incorporating preload mechanisms to reduce backlash and improve gear meshing accuracy.
- Design the gear system with adjustable features to compensate for wear and maintain precise motion control over time.
7. Rigorous Testing and Quality Control:
- Conduct extensive testing, including backlash measurement, noise analysis, and efficiency testing, to validate gear performance and accuracy.
- Implement strict quality control measures during manufacturing to ensure consistency and reliability.
8. Non-Circular Tooth Profiles (Optional):
- For specialized applications, consider non-circular tooth profiles to enable unique motion patterns or tasks. However, these designs may require more complex manufacturing and analysis.
By carefully considering these design factors and tailoring the worm gear to the specific requirements of the low-backlash and high-accuracy system, engineers can create custom worm gears that deliver precise motion control, reduced backlash, and high reliability, meeting the stringent demands of critical applications where precision is paramount.