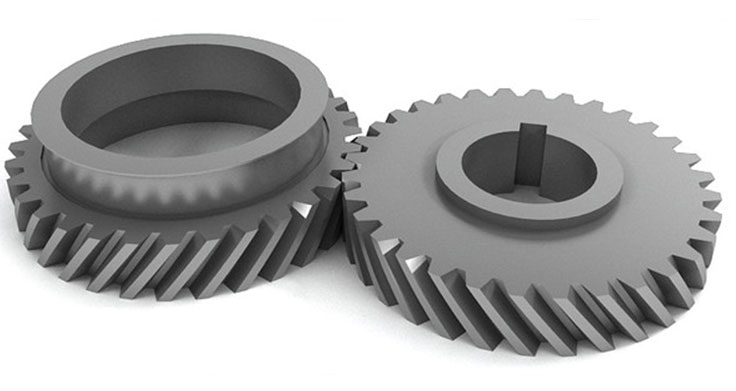
Designing helical gears for smooth and efficient power transmission involves considering various factors that affect gear performance. Here are some key design considerations to achieve smooth and efficient power transmission in helical gears:
1. Helix Angle Selection:
- The helix angle is a crucial design parameter that directly impacts gear performance. A higher helix angle allows for more teeth in contact at any given moment, distributing the load across a larger tooth surface. This results in smoother power transmission and reduced tooth contact stress.
2. Tooth Profile and Contact Ratio:
- The choice of tooth profile, such as involute or cycloidal, and the contact ratio influence the gear’s meshing behavior and load distribution. A well-designed tooth profile with an appropriate contact ratio ensures efficient power transmission while minimizing friction and wear.
3. Module and Pressure Angle:
- Selecting the proper module (gear size) and pressure angle is critical for the gear’s strength and load-carrying capacity. A higher module generally results in larger gear teeth and higher torque transmission capabilities.
4. Material Selection:
- Choose high-quality materials with excellent strength, fatigue resistance, and wear properties. The material should be capable of handling the applied loads and provide sufficient safety margins to avoid premature failure.
5. Lubrication and Surface Finish:
- Proper lubrication with the right type of lubricant is essential for reducing friction and wear. A smooth and consistent surface finish on gear teeth also contributes to efficient power transmission by reducing surface roughness and improving contact conditions.
6. Tooth Profile Modifications:
- Optimizing tooth profile modifications, such as crowning and tip relief, can help mitigate misalignments and improve meshing behavior, resulting in smoother and quieter gear operation.
7. Backlash Control:
- Properly controlling backlash ensures accurate motion transfer and reduces impact forces during gear meshing, contributing to smoother operation and reduced noise.
8. Noise Reduction:
- Minimizing gear noise is essential for smooth operation. Various noise reduction techniques, such as profile modifications, surface treatments, and gear coatings, can be employed to achieve quieter gear performance.
9. Proper Mounting and Alignment:
- Precise mounting and gear alignment are crucial to avoid uneven loading and premature wear. Ensuring accurate gear positioning enhances the efficiency of power transmission.
10. Finite Element Analysis (FEA):
- Utilize FEA simulations to analyze stress distribution, deformation, and load-carrying capacity of the gear design before manufacturing. This helps identify potential issues and optimize the gear’s performance before physical production.
11. Manufacturing Precision:
- High manufacturing precision, including accurate gear tooth profile, tooth spacing, and surface finish, is essential for achieving the intended gear performance.
12. Thermal Considerations:
- Account for the heat generated during gear meshing and the effect of thermal expansion on gear performance. Adequate cooling and material selection to withstand temperature fluctuations are important.
By considering these design factors and applying best practices, engineers can create helical gears that deliver smooth and efficient power transmission, resulting in reliable and high-performance gear systems for various industrial applications.