Designing spiral bevel gears involves several key considerations to ensure optimal performance. Here are some important factors to keep in mind:
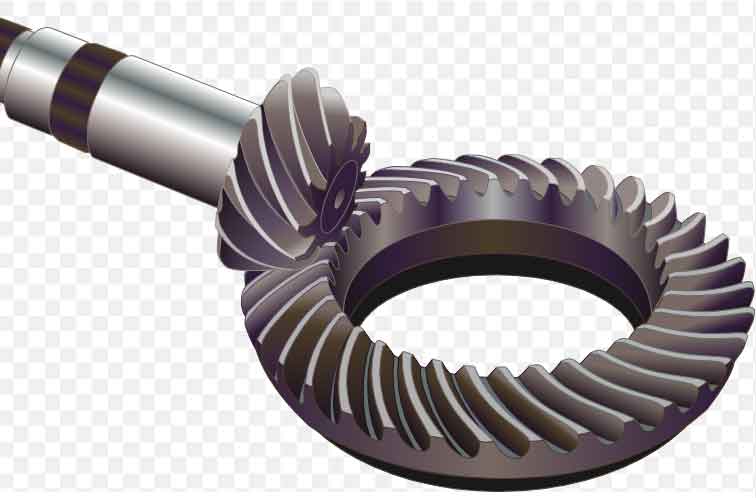
Gear Geometry:
The geometry of the spiral bevel gears is critical for their performance. It includes parameters such as the gear ratio, number of teeth, tooth profile, pitch diameter, and pressure angle. These parameters should be carefully selected based on the specific application requirements.
Tooth Profile:
The tooth profile is crucial for smooth and efficient power transmission. The profile should be designed to minimize tooth-to-tooth impact and ensure proper meshing. Common tooth profiles used for spiral bevel gears include the Gleason and Klingelnberg systems.
Contact Pattern:
Achieving a good contact pattern is essential for efficient load distribution and reduced noise and vibration. The contact pattern should ideally be located in the center of the gear tooth, and the contact area should be appropriately distributed to ensure uniform loading.
Axial Thrust:
Spiral bevel gears produce axial thrust due to the helical angle of their teeth. This thrust should be properly managed by incorporating thrust bearings or other means to prevent excessive axial loading on the gear shafts.
Strength and Durability:
The gears should be designed to withstand the expected loads and provide sufficient strength and durability. Factors such as material selection, heat treatment, and gear dimensions play a vital role in ensuring long-term performance.
Lubrication:
Proper lubrication is crucial for reducing friction, wear, and heat generation. Lubricant selection and a reliable lubrication system should be considered during the design phase to ensure adequate lubrication reaches the gear teeth.
Manufacturing Considerations:
The design should be compatible with the available manufacturing processes, such as gear cutting and machining methods. Close collaboration between designers and manufacturers is essential to ensure the feasibility and cost-effectiveness of the gear manufacturing process.
Noise and Vibration:
Spiral bevel gears can generate significant noise and vibration due to their tooth contact patterns. Design modifications, such as optimization of tooth contact, tooth profile modifications, and the use of noise-reducing features, can help minimize noise and vibration levels.
Tolerances and Quality Control:
Accurate tolerances should be specified for critical gear dimensions to ensure proper assembly and optimal performance. Quality control measures, including inspection and testing techniques, should be implemented to verify the gear’s dimensional accuracy and performance characteristics.
Application-Specific Factors:
Consideration should be given to the specific application requirements, such as operating speed, torque, temperature, and environmental conditions. These factors may influence material selection, heat treatment, lubrication, and other design parameters.
Overall, a successful spiral bevel gear design requires a comprehensive understanding of the gear’s intended application, coupled with careful consideration of the above factors. Collaboration between mechanical engineers, gear designers, and manufacturers is essential to optimize the performance, durability, and reliability of the gears.