The established three-dimensional digital models of the half shaft gear and planetary gear are introduced into the software of the gear measuring machine, and compared with the actually processed straight bevel gear standard wheel. A total of 45 tooth surface points near the pitch circle of the tooth surface are detected. The detection results show that the accuracy of the straight bevel gear standard wheel reaches grade 4 accuracy, and the maximum tooth surface deviation of the actually processed straight bevel gear standard wheel is 0.007 mm compared with the three-dimensional digital model, The machining accuracy required by the standard wheel of straight bevel gear is achieved.
In order to verify the contact area, vibration and noise, the straight bevel gear standard wheel was further tested on the roll inspection machine, as shown in Fig. 1.
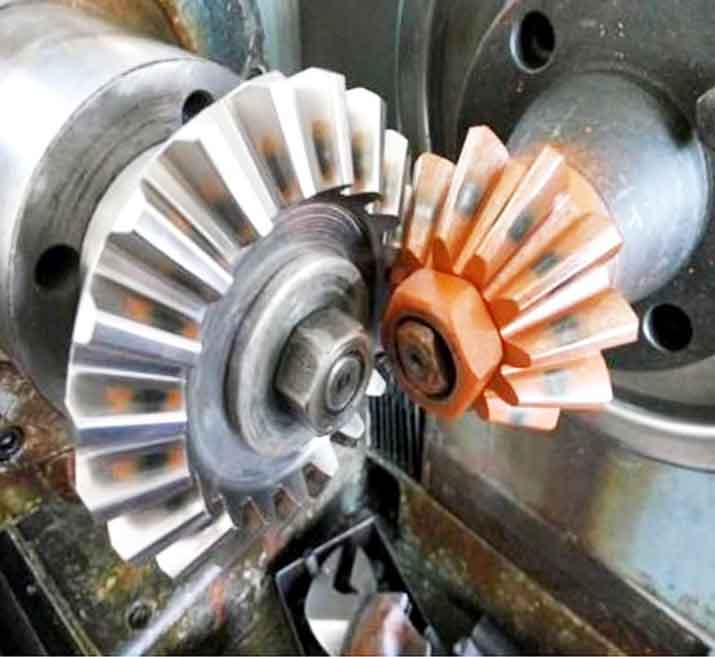
It can be seen from Fig. 1 that the actual roll inspection effect is close to the simulation effect of contact area in UG software in Fig. 2. Under no-load condition, the contact area is close to the small end, occupying about 50% of the length of the tooth, occupying about 60% of the length in the tooth height direction, and close to the high and middle part of the tooth. There is no edge contact, and the vibration and noise are good. It is the most ideal contact area. This proves the correctness of the established cold state mathematical model. The modeling method and contact zone simulation analysis method are universal in the straight bevel gear industry.
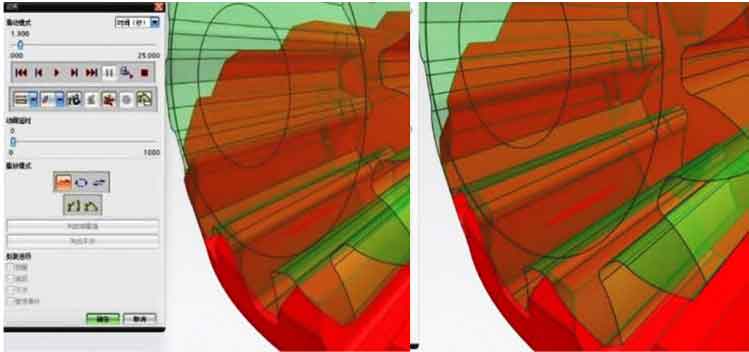