According to GB/T 9450-2005 “Determination and Verification of Hardened Case Depth of Carburizing and Quenching of Steel Parts”, the effective hardened case depth of uncracked tooth surface (concave surface) and cracked tooth surface (convex surface) pitch circle and tooth root part of tooth shape specimen are measured respectively.
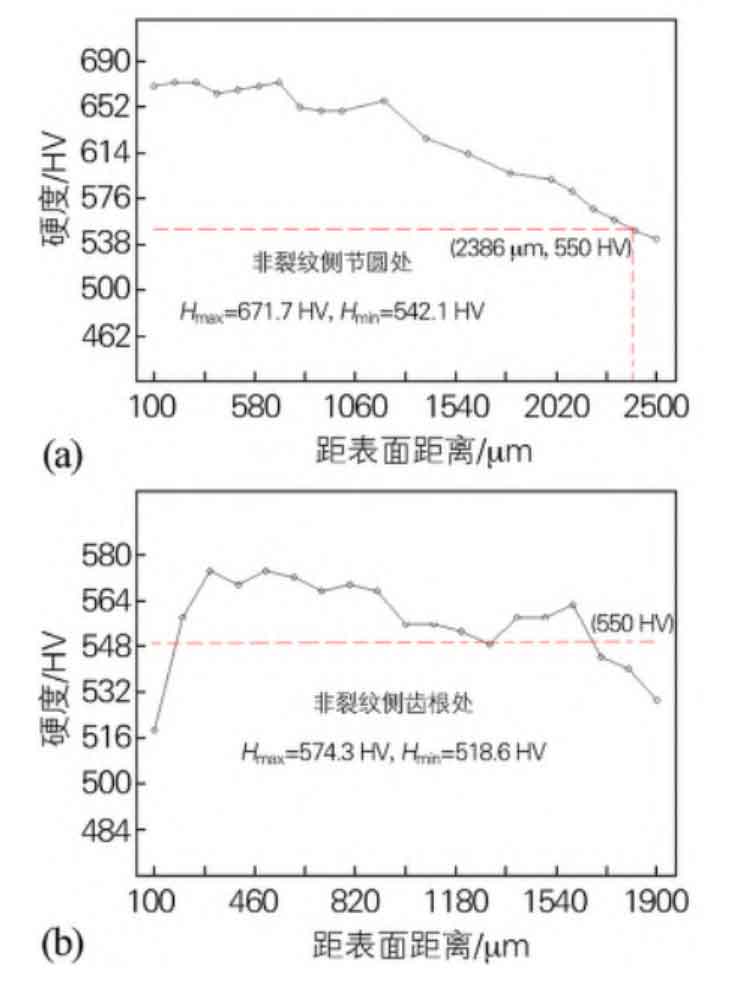
Figure 1 shows the hardness distribution curve at the pitch circle of the uncracked tooth surface (concave surface) and near the root of the tooth. It can be seen from Figure 1 (a) that the effective hardened layer depth after grinding at the pitch circle of the uncracked tooth surface is 2.386 mm, and the hardness at 0.1 mm from the surface is 668.6 HV (58.1 HRC). The surface hardness and effective hardened layer depth after grinding at the pitch circle meet the technical requirements of the drawing.
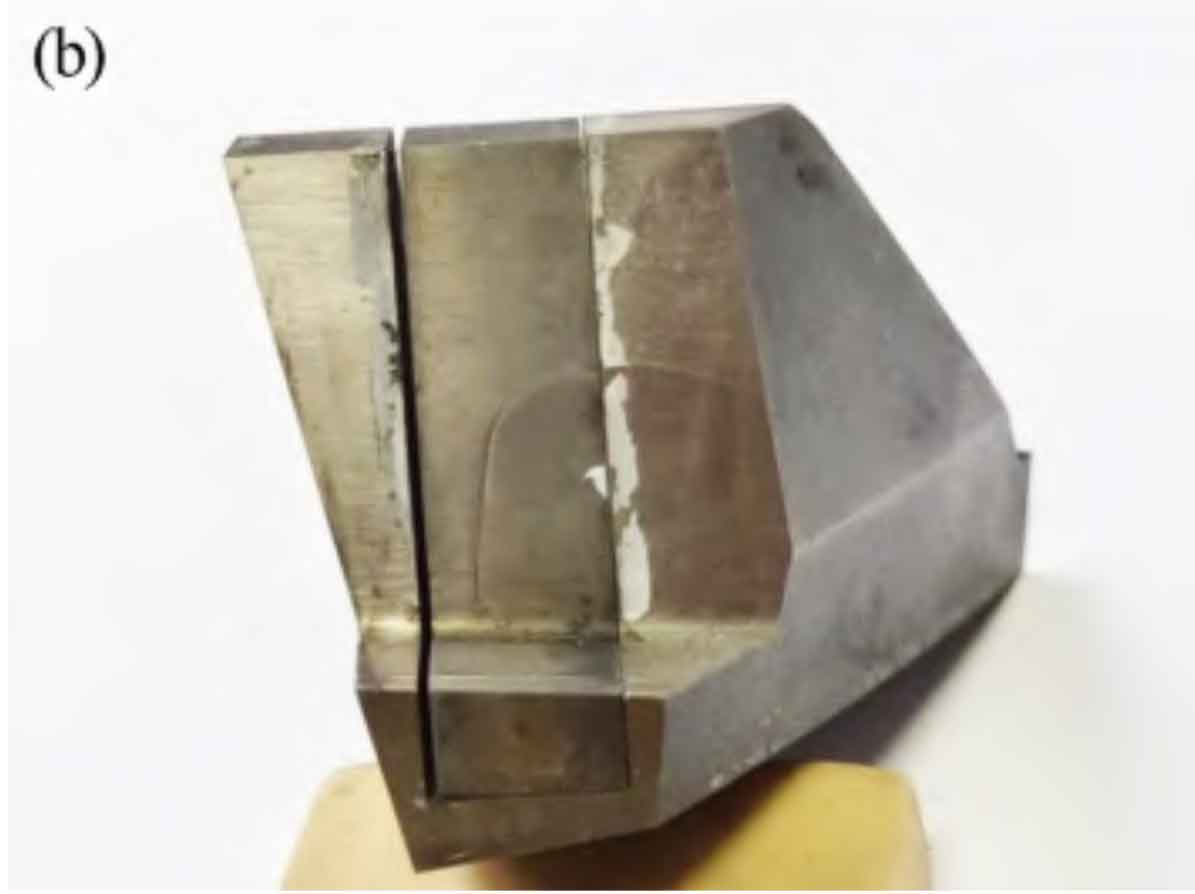
It can be seen from Figure 1 (b) that the hardness of the uncracked tooth surface 0.1 mm away from the surface near the tooth root is 518.6 HV, and there is an obvious “low head” phenomenon of hardness. The effective hardened layer depth is also significantly smaller than the pitch circle, only about 1.3 mm, which indicates that the tooth surface near the tooth root produces more grinding heat during grinding, which makes the tooth surface soften by heat tempering, the hardness decreases, and there is an obvious “low head” phenomenon of hardness, The effective hardened layer depth is too small.
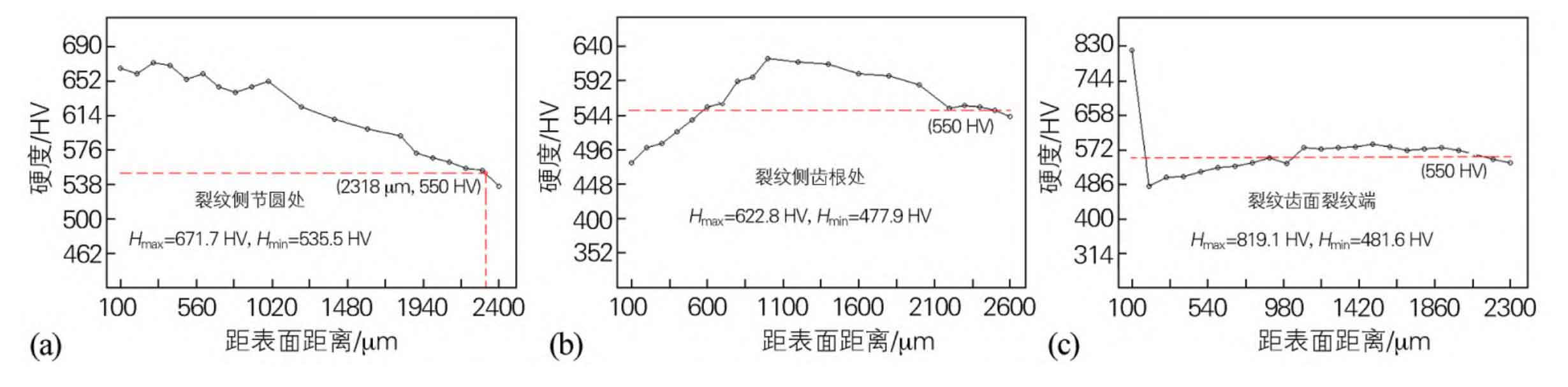
As shown in Figure 2, the left end of the arc-shaped crack on the cracked tooth surface (convex surface) of the tooth-shaped sample is vertically downward to the root of the tooth, and the lower end of the crack is about 3 mm away from the left end face, so the left end face of the tooth block in Figure 2 is called away from the crack; The arc-shaped crack extends to the right and upward, and the intersection of the right end face and the crack is called the crack. The effective hardened layer depth on the crack surface far from the crack and the crack is measured respectively, and compared with the uncracked tooth surface.
The hardness distribution curve of the convex surface of the tooth-shaped specimen away from the crack pitch circle is shown in Figure 3 (a). The effective hardened layer depth after grinding is 2.318 mm, and the hardness at the place 0.1 mm from the surface is 665.6 HV (58.0 HRC), which meets the technical requirements of the drawing.
See Figure 3 (b) for the hardness distribution curve of the convex surface of the tooth-shaped sample near the crack root. The hardness at 0.1 mm from the surface is only 477.9 HV, with obvious “low head” phenomenon of hardness, and the effective hardened layer depth is about 2.5 mm, which indicates that the tooth surface near the crack end near the tooth root produces more grinding heat when grinding the tooth, which makes the tooth surface heated and tempered, reduces the hardness, and presents obvious “low head” phenomenon of hardness, However, the effective hardened layer depth is still normal.
From Fig. 3 (c), it can be seen that the convex crack of the tooth-shaped sample is 0.1 mm away from the surface, and the hardness rises abnormally to 820 HV0.1 (63.8 HRC), with obvious hardness “rising” phenomenon, and then the hardness quickly drops to the lowest point of 486 HV, and then starts to rise slowly. The hardness rises and falls sharply within the range of 0.2 mm from the surface, and the effective hardening layer gradient at the crack shows obvious grinding burn characteristics.