①
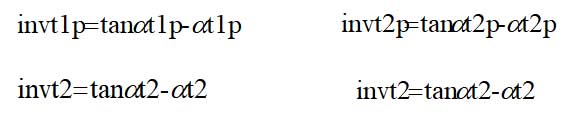
② Selection of normal face modification coefficient of pinion
Selection principles: (1) when the hardness of the gear surface is not high (hbs350), the transmission failure is often caused by the fracture of the gear teeth caused by the fatigue crack propagation of the gear roots. In this case, the selection of the modification coefficient should make the bending strength of the gear roots increase as much as possible, and make the two meshing gears have the similar bending strength as much as possible.
(2) The main failure mode of open gear transmission is grinding wear or tooth fracture. Therefore, it is necessary to select the positive displacement gear with the total displacement coefficient X Σ as large as possible, and distribute the displacement coefficient appropriately so that the maximum sliding rate at the root of the two wheels is equal, which can not only reduce the maximum sliding rate, improve its wear resistance, but also increase the thickness of the root and improve the bending strength of the teeth.
(3) The tooth surface of heavy load gear transmission is easy to produce gluing damage. In addition to choosing appropriate viscosity of lubricating oil or using active lubricating oil with additives, when using the modified gear, the engagement angle of the transmission should be increased as much as possible (i.e. the total modification coefficient X Σ should be increased), and the modification coefficients XL and X2 should be distributed appropriately to make the maximum sliding rate close to the same, which can not only increase the tooth surface In order to improve the scuffing resistance of gears, it can reduce the contact stress and the maximum sliding rate.
(4) In order to reduce the pressure on the tooth surface of the node, the displacement coefficient can be properly selected to make the node located in the meshing area of two pairs of teeth, so as to reduce the load on each pair of meshing teeth and improve the bearing capacity.
(5) The helical cylindrical gear transmission can adopt the high displacement or the angle displacement, but in fact, it mostly adopts the standard gear transmission. By using angle modification, the comprehensive curvature radius of the tooth surface can be increased, which is beneficial to improve the contact strength of the helical gear. However, when the modification coefficient is large, the contact line of the meshing gear teeth will be excessively shortened, and the bearing capacity will be reduced. Therefore, it is not effective to improve the load-carrying capacity of helical cylindrical gear by using angle displacement. Sometimes, in order to match the center distance, when using the modified gear, the modification coefficient can be determined by the method of selecting the modification coefficient of the straight tooth circular cylindrical gear according to its equivalent number of teeth zv (= Z / cos3 β).