In the 1950s, the former Bayer light metal company of West Germany took the lead in using the precision die forging method on the friction press to replace the original machining method to manufacture the bevel gear and obtained the patent right of this technology. The precision forged gear produced by this technology has a tooth surface roughness of R α 1.6, r near the tooth root α 3.2 the tooth root fillet is r0.6-0.8, and the tooth profile does not need to be cut. The tooth profile accuracy can reach din6 level of West German standard (equivalent to 8 level accuracy of Chinese gear standard), saving 20%-30% of materials and improving 15%-30% of mechanical properties. After that, various industrial countries have successively introduced this technology or developed new technologies by themselves. In the middle and late 1950s, the former Soviet Union has been able to forge fine forgings equivalent to coarse teeth on friction presses or hot die forging presses.
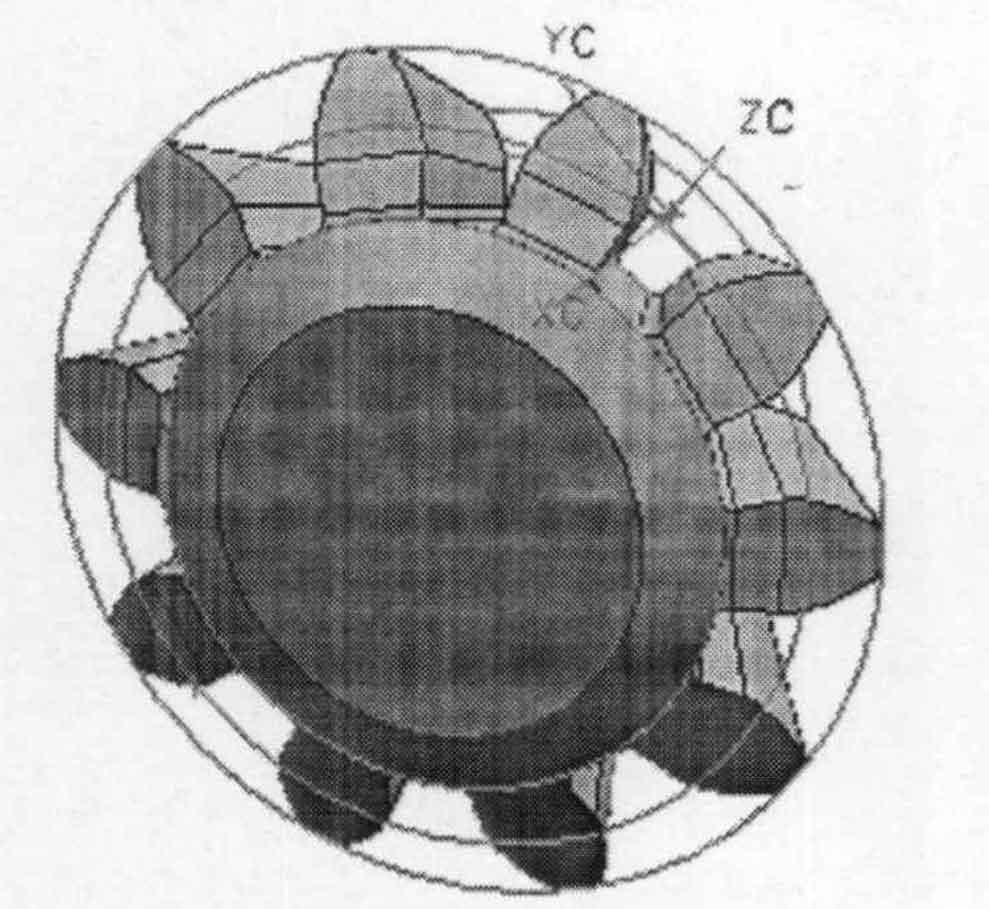
Japan and the United States not only introduced this technology, but also fully developed the gear precision forging process. In 1969, the United States successfully developed the precision forging process of active and passive spiral bevel gears for helicopters, and the precision forging spiral bevel gear technology has great advantages in improving the mechanical properties of gears and reducing production costs.
After Mitsubishi introduced the precision forging technology of Bayer light metal company in West Germany and used it in production, the precision forging driven spiral bevel gear technology developed by Mitsubishi was put into production in 1974. The maximum diameter of the produced gear is 180mm, and the precision reaches jis3-4 (equivalent to grade 8-9 of China’s gear precision standard). At the same time, Mitsubishi has developed warm precision forging and cold precision forging technology. When the annual output reaches more than 100000 pieces, precision forging saves more production costs than cutting process, and the larger the batch, the more economical it is.
Since the 1990s, the country has listed the precision forging gear technology as a key energy-saving material promotion project. With the strong support of national policies and the joint efforts of the whole industry, the precision forging gear technology has been developed in an all-round way. The output of precision forged gears has also risen sharply with the vigorous development of the automotive industry.