The die angle is one of the important process parameters in the design of tooth concave die. It is not only related to the quality of formed spur gear, but also has a great impact on the wear and service life of the die. In order to study the die angle α For the influence law of spur gear forming, the die entry angle is selected respectively α The numerical simulation is carried out at 25 °, 35 °, 45 °, 55 ° and 65 °, and the other process parameters are tooth top fillet r = 1.2mm, splitting angle thickness t = 2.5mm and sizing belt length L = 5mm.
Fig. 1 shows the effect of die angle on the forming quality of cold extruded spur gear. The amount of tooth tip collapse angle and end face convexity increase with the increase of die angle. That is, with the increase of die angle, the forming quality of cold extruded spur gear becomes worse.
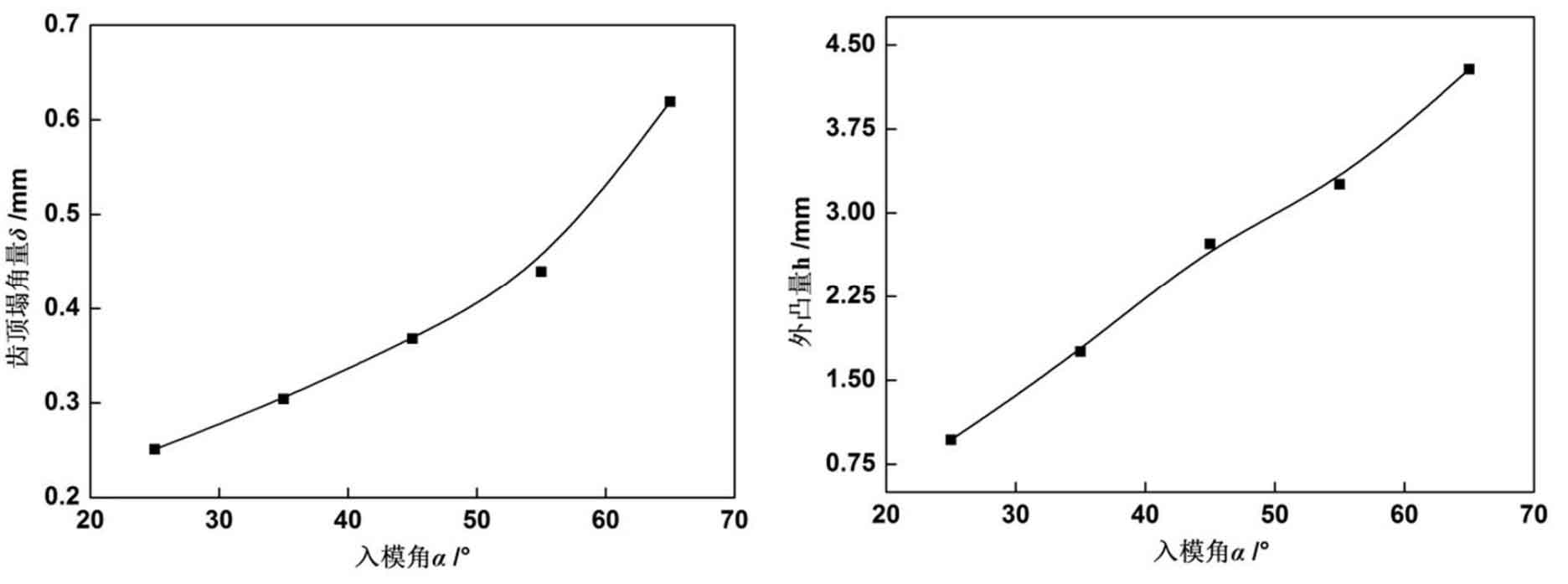
(b) External convexity with die angle α Change curve of
Fig. 2 and Fig. 3 show the die angle respectively α= Velocity distribution of cold extrusion forming of spur gear at 25 ° and 65 °. At the initial stage of billet splitting, as shown in Fig. 2 (a) and Fig. 3 (a), the velocity distribution of the end face is relatively uniform, and the difference of the die angle does not cause the difference of the inner and outer velocity of the end face. When the blank gradually enters the sizing belt after splitting, as shown in figures 2 (b) and 3 (b), the size of the injection angle will affect the flow velocity of the inner and outer layers of the metal. When the injection angle is 25 °, the flow of the inner and outer formed metal is more uniform; When the mold entry angle is 65 °, the flow velocity of the inner metal is significantly faster than that of the outer metal.
This is because the cold extrusion of spur gear is the forward extrusion of hollow parts with mandrel. The severe deformation area is mainly concentrated in the die inlet and sizing belt area of tooth die. Before or after the metal enters or leaves the deformation area, there is no plastic deformation and only rigid translation. In the deformation area, the metal is plastically deformed and moves along the axial direction of the toothed die to overcome the friction resistance. When the die entry angle increases, the splitting blank stroke of the toothed die increases. The friction resistance between the metal and the die makes the outer metal flow slowly, resulting in the increase of the end face protrusion with the increase of the die entry angle.
The inner and outer metal flows unevenly, and the faster inner metal has a radial pulling effect on the slower outer metal, so the amount of tooth top collapse angle also increases with the increase of die angle. The blank continues to go down with the punch and gradually separates from the deformation area, as shown in figures 2 (c) and 3 (c). At this time, there is no plastic deformation and only rigid translation, so the inner and outer metals flow at the same speed.
Fig. 46 shows the influence law of die angle on cold extrusion forming load, which refers to the forming load in the stable forming stage of cold extrusion. The forming load decreases with the increase of die angle. This is because in the stable forming stage of cold extrusion, the deformation degree remains unchanged. With the increase of die angle, the splitting extrusion shear power decreases, the friction power increases, and the decrease of shear power is greater than the increase of friction power. Therefore, increasing the die angle can reduce the forming load in the stable extrusion stage. Current die angle α= At 25 °, the maximum forming load is about 2413kn, and the molding angle is α= At 65 °, the maximum forming load is about 2060kn, and the forming load is reduced by 14.6%.
To sum up, when the die angle is small, the forming quality of spur gear is good, but the forming load is large, so the equipment with large forming tonnage needs to be selected; When the die angle is large, the forming load is reduced, but the forming quality is poor, and the long splitting stroke and large contact area will make the phosphorus saponification film on the blank surface thin or even crack, resulting in tooth surface strain and die sticking, which seriously affects the production efficiency and die service life.