During quenching and cooling, the workpiece will generate volume expansion and large thermal stress and structural stress. If the volume expansion and stress generated are uniform, the distortion will be easily controlled. However, there are many factors that will cause uneven cooling in production, such as:
(1) The shape of the gear workpiece is complex, the size and the wall thickness are not uniform, so it is difficult to reduce the temperature of each part of the workpiece uniformly under the same cooling condition;
(2) There are many workpieces loaded in one furnace, even many kinds of mixed loading, and the cooling between workpieces during quenching is more unlikely to be uniform;
(3) Uneven cooling of workpiece due to medium cooling characteristics. Uneven cooling is the root cause of workpiece distortion.
1. Uneven cooling caused by workpiece structure
A kind of double gear. The distortion of the inner hole of the gear after carburizing and quenching is shown in the table. From the data, it can be seen that the hardness, effective hardening depth and microstructure of the surface and center after heat treatment are all qualified, but due to the structural factors, the inner hole distortion is not consistent, the overall shape is a bell mouth, and the grinding allowance of each part is very different.
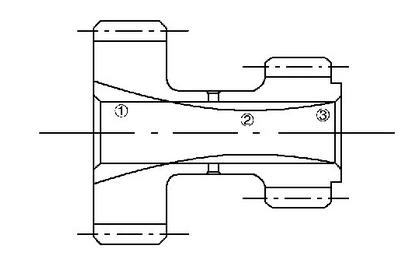
2. Uneven cooling caused by workpiece clamping
After simulating the flow field of the quenching tank, it is found that the flow field of the production quenching tank is uniform when it is empty (not put into the workpiece), but when it is quenched into the workpiece, the flow field of the quenching liquid in the tank changes depending on the workpiece and the fixture, so that the distribution of the flow field around the workpiece is uneven. Through the test, the distribution of the quenching intensity everywhere is obviously uneven, This is one of the reasons why the distortion of workpiece is hard to control.
3. Uneven cooling caused by characteristics of cooling medium
As you can imagine, if only one workpiece is placed in the quenching tank, without the influence of other substances, the workpiece will surely get uniform cooling, which is not the case in fact. The following are the test observations of various shapes of samples.
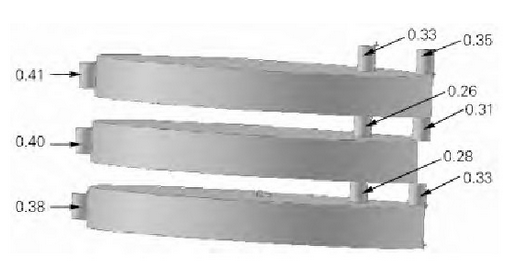
1) Conical specimen
It shows the quenching and cooling condition of a conical sample with small upper and large lower parts in water. The upper part of the workpiece has entered the boiling cooling stage, while the lower part is still in the cooling stage of the steam film. At the boundary between the boiling cooling zone and the steam film enveloping zone, the cooling rate of the workpiece surface is very different. If the difference of cooling speed is assumed to be the difference of effective thickness, the thick part of workpiece will become thicker, thus further increasing the nonuniformity of workpiece cooling.
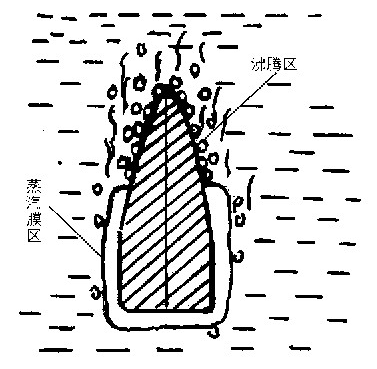
2) Square sample
Figure 12 shows the gas flow in the laminar layer of the vapor film when the square sample is quenched and cooled. The vapor film moves up along the surface of the sample from bottom to top, and the upper and lower surfaces of the cylinder are covered by the vapor film, so the cooling is very slow.
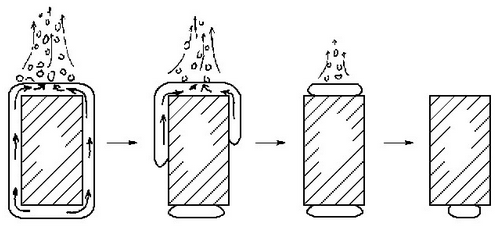
3) Spherical specimen
Figure shows the cooling of the spherical specimen in the base oil. From the expansion line of the steam film in FIG, it can be seen that the temperature difference will occur during the whole cooling process even if the uniform spherical sample is quenched and cooled under the long-term cover of the steam film, which will cause the uneven distortion.
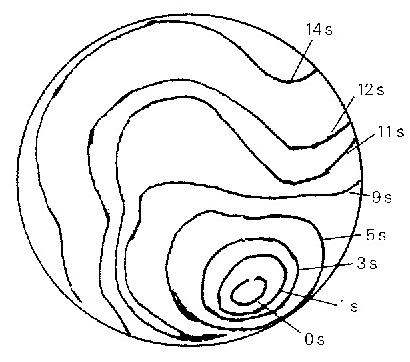