The dynamic characteristics of the main influencing factors of helical gear vibration and noise are studied. Considering the dynamic characteristics of helical gear transmission with tooth surface friction, the following main conclusions are obtained:
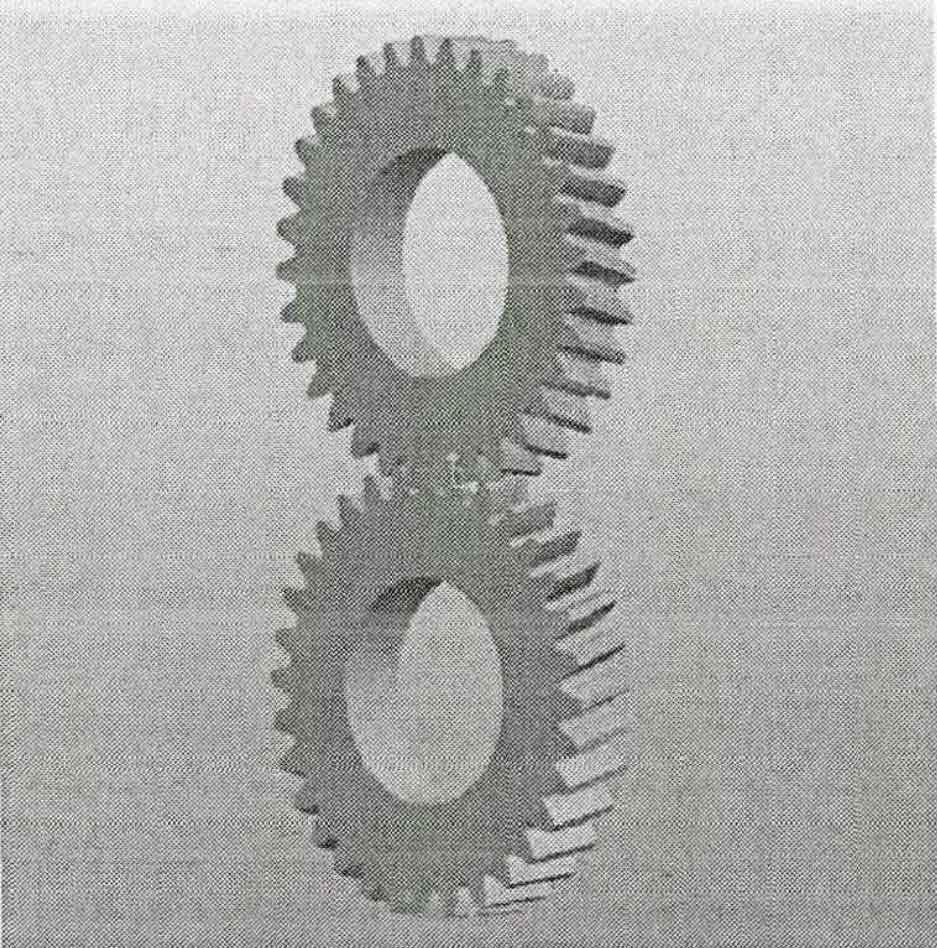
- It breaks through the limitation that the calculation of time-varying contact line length is limited by the shape of meshing area and the number of contact lines engaged at the same time, and expands the application scope of numerical calculation of contact line. The algorithm is accurate, convenient and practical. It is revealed that the minimum condition for the change of the total length of the contact line of the helical gear: at the initial time, when L1 (the shortest distance from the upper end of the contact line to the right end of the meshing area at the meshing starting time) and the tooth pitch of the end face are equal, and L2 (the shortest distance from the upper end of the contact line to the left end of the meshing area at the meshing starting time) and L4 (the shortest distance from the lower end of the contact line to the right end of the meshing area at the meshing starting time) are equal, the total length of the contact.
- Based on the improved algorithm of time-varying contact line length, a refined algorithm of tooth friction and tooth friction torque is constructed by using the piecewise spur gear method and considering the friction effect of helical gear under mixed elastohydrodynamic lubrication. After analyzing the fluctuation of tooth surface friction and tooth surface friction torque, it is found that the fluctuation of time-varying contact line length is an important reason for the fluctuation of tooth surface friction and tooth surface friction torque. Within the parameter range selected in this paper, the fluctuation of time-varying contact line length, tooth surface friction and tooth surface friction torque is the smallest at 20 °, which provides a theoretical basis for helical gear parameter design and engineering optimization.
- Based on the principle of minimum energy, a theoretical model for calculating the load distribution along the contact line of involute gears is established, which is suitable for calculating the load distribution along the contact line of spur and helical gears. The load distribution rate of spur gear varies from 0.33 to 0.67 when two teeth mesh. The load distribution of helical gear along the time-varying contact line, and the load at the node is the largest.
- The influence of tooth surface friction is considered in the deformation analysis of gear teeth. The sudden change of deformation at the joint caused by tooth surface friction is up to 12%. The time-varying meshing stiffness of the helical gear is calculated by using the deformation of the helical gear node and the change law of the time-varying contact line. The results show that the meshing stiffness of the helical gear increases when the friction is considered, and the meshing stiffness has an obvious effect on the increase of the axial vibration displacement of the driven gear.
- The tooth surface friction can inhibit the resonance amplitude. As the friction coefficient increases, the resonance amplitude decreases and the resonance frequency increases slightly. When considering the tooth friction, the amplitude of vibration response caused by static load is significantly lower than that without friction, and the frequency of resonance changes greatly when the static load is larger than that without friction; The resonance amplitude caused by dynamic load and damping is obviously reduced compared with that without friction, and the resonance frequency is slightly increased, but the damping has little effect on the 1/2 order frequency resonance when considering friction.
- Considering the overall error and tooth surface friction, the dynamic equation of helical gear is constructed. In the case of variable speed, the effects of load and damping on the maximum transmission error, maximum meshing force, maximum meshing acceleration and dynamic factor of helical gear are analyzed. The influence of error excitation on the dynamic response of heavy-duty helical gears becomes smaller, and the influence of error excitation on the dynamic response becomes larger at high speed. The effect of damping on reducing error excitation on dynamic response is obvious. Considering the overall error on the time-varying contact line of the helical gear, the dynamic analysis of the gear can determine the specific position of the error on the tooth surface, and provide a theoretical basis for the modification design of the helical gear.