The research on the gear failure of involute helical gear is carried out, focusing on the engineering problems of uneven stress distribution and vibration noise of helical gear. It is proposed to improve the bearing capacity of helical gear from its own structural parameters, and establish the parametric model of standard helical gear. Through the modal analysis of helical gear and the dynamic contact analysis before and after modification, The following conclusions are drawn:
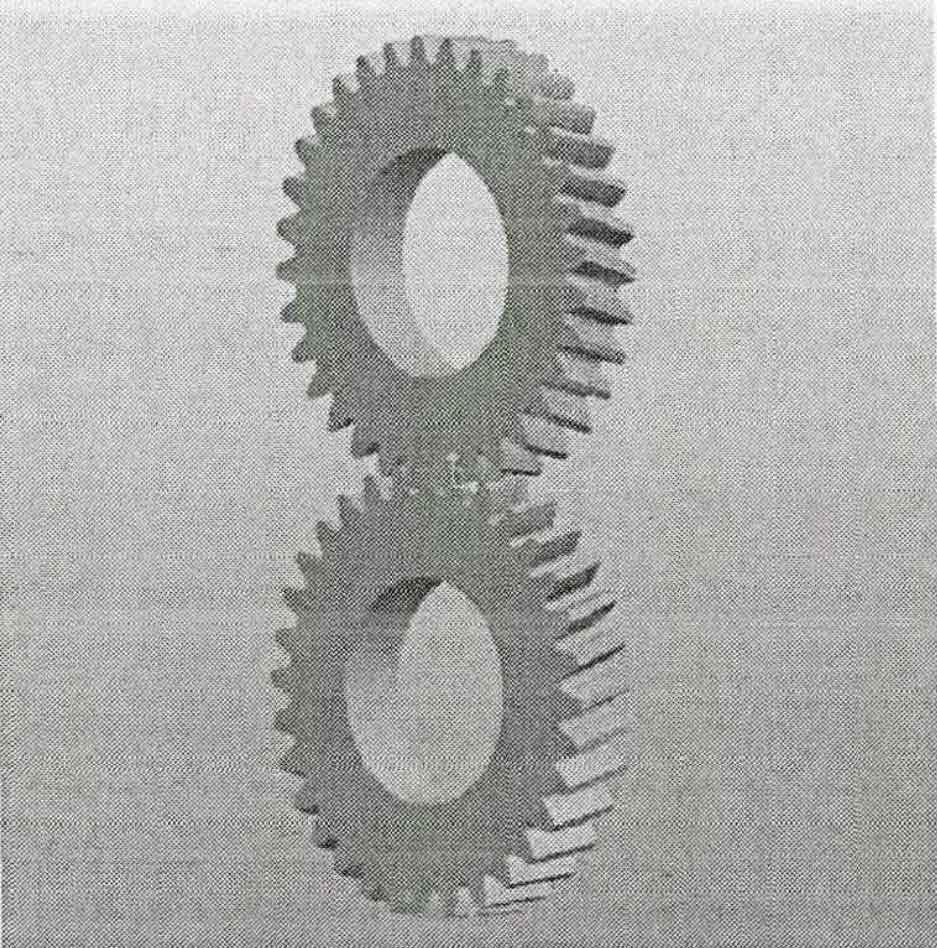
(1) Taking the generation mechanism of helical gear involute as the starting point, and according to the structural characteristics of helical gear, the relationship between the basic parameters of helical gear end face and normal face is analyzed. Based on this as the theoretical background, the involute equation and tooth root transition curve equation of helical gear are established. According to the structural characteristics of the helical gear, the parametric feature model of the helical gear is established. Through the pro parametric modeling tool, the driving relationship between the basic parameters of the helical gear and the dimensions of the helical gear is defined. By changing the basic parameters of the helical gear, the parametric feature model of the helical gear can be regenerated to facilitate the subsequent establishment of the helical gear model, At the same time, it also provides a model basis for subsequent finite element analysis.
(2) The finite element software ANSYS / workbench is used to solve the calculation problem. The modal analysis of helical gear assembly is carried out by using workbench software. The 20th order i-state value of helical gear assembly model is obtained by solving, and the corresponding modal shape diagram is obtained at the same time. In view of the specific problems, the transient dynamic calculation and analysis of the helical gear are carried out. The transient dynamic contact analysis of the helical gear is carried out by using the workbench software. The equivalent stress 5 diagram of the helical gear in the meshing process, the contact pressure nephogram of the meshing surface, and the structural stiffness of the helical gear are obtained and analyzed. By changing the boundary conditions, the contact stress of helical gears at different speeds is studied. The dynamic contact analysis of the gear is carried out by the method of heat engine friction, and the stress state of the gear considering friction and temperature is obtained.
(3) Determine the modification scheme. The principle of gear modification is discussed deeply, and the modification amount is calculated theoretically. The repaired helical gear is re modeled and assembled by using proe software, and the dynamic contact analysis of helical gear is carried out by using the finite element software ANSYS. Analyze and compare the results before and after reshaping. Through the comparison before and after modification, the conclusion is drawn that the problem of uneven load distribution of helical gear teeth is solved.