The vibration response of spur gear pairs during meshing varies with boundary conditions. This section establishes a finite element model of spur gear dynamics with different center distance deviations, different rotational speeds, and different load torques. Through transient dynamic finite element simulation analysis, the impact of different parameters on the dynamic vibration characteristics of spur gears is studied.
The model used has been modified based on the static finite element model, mainly reflected in:
(1) The torque application method is modified to gradually increase from 0s, reach a stable value T at 0.03s, and continue until the end of the simulation;
(2) The constraint condition for the rigid body shell of the inner ring of the spur gear driving wheel is modified to constrain all degrees of freedom except for the freedom of axial rotation, and the rotational speed is applied. The rotational speed needs to be applied after the torque is applied to a stable value, and gradually increases to a stable value n.
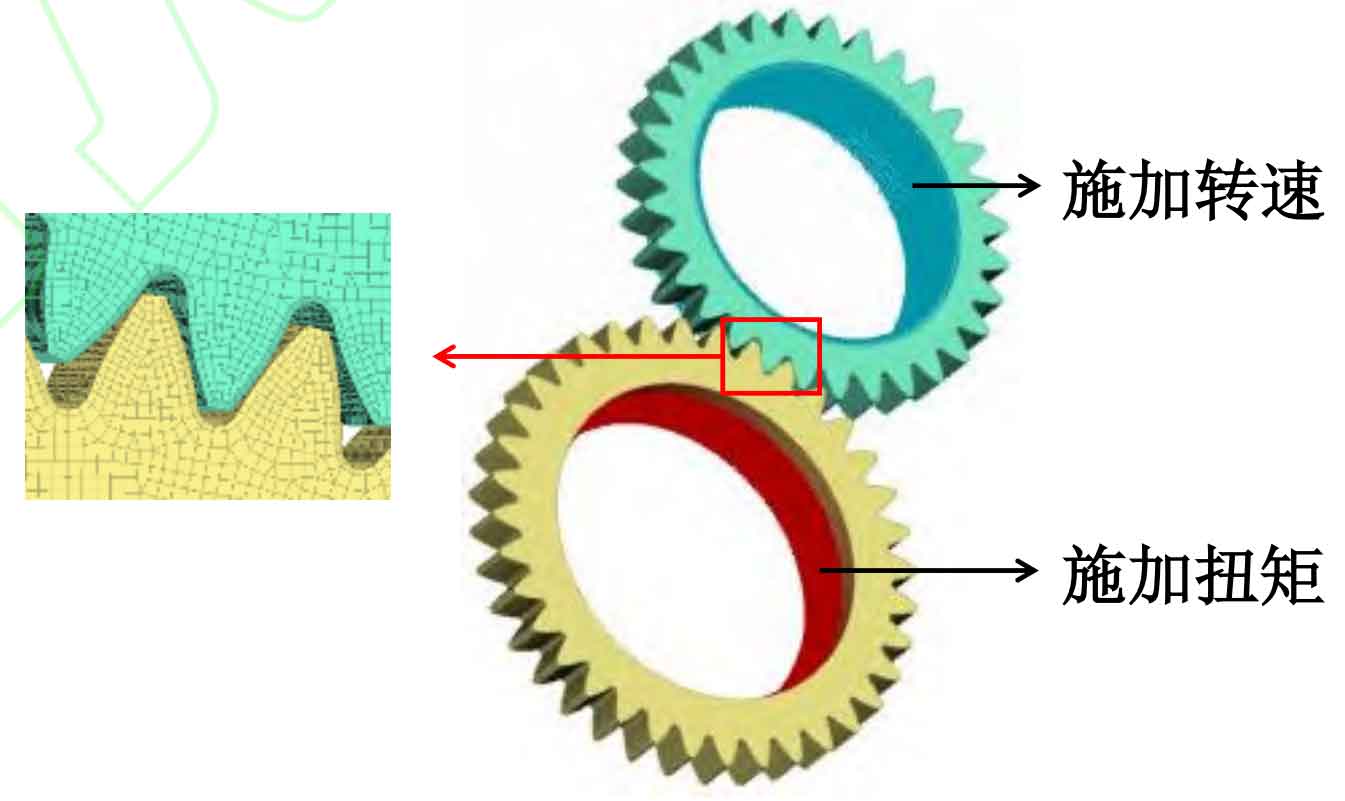
The dynamic meshing finite element model of spur gear pair is shown in the figure.