At present, there are more researches on the vibration of gear pair under the action of nonlinear excitation, and there are also many researches on the dynamics of gear transmission system, but there is little research on the mechanism of compound fault of gear transmission system. In this paper, the gear pair dynamic model and the rolling bearing system dynamic model are combined by using the lumped parameter method, and a 36 DOF gear transmission system complex fault dynamic model is established. The research objects of this model are gears and bearings, and the rotor is regarded as rigid. The vibration signal can reflect the fault characteristics of gear and rolling bearing, so this chapter obtains the vibration signal of gear and bearing through dynamic simulation, and then analyzes the vibration signal of the system by using statistical characteristic parameters, so as to explore the influence of compound fault of gear transmission system on system vibration characteristics.
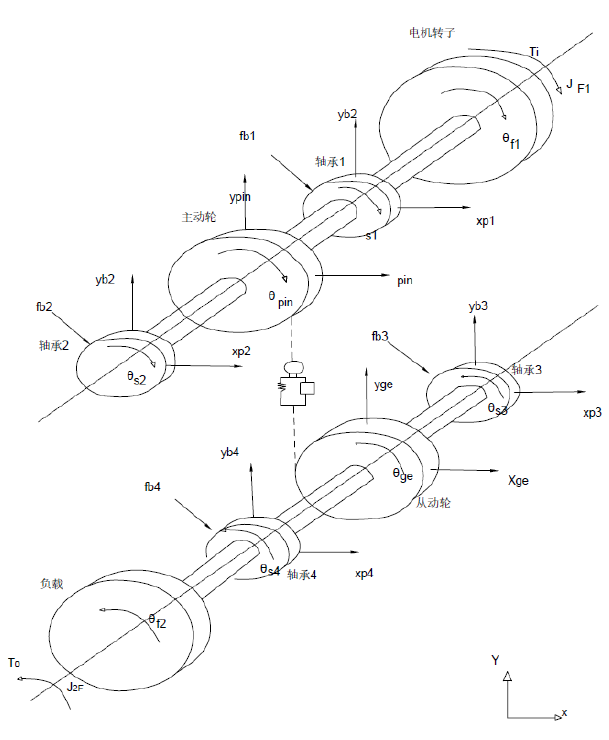
Combining the dynamic model of gear pair and rolling bearing, the dynamic model of gear transmission system shown in Fig. 1 is established. The motion control equation is as follows:
1) Motion control equation of motor input shaft

2) Motion control equation of driving wheel support bearing 1
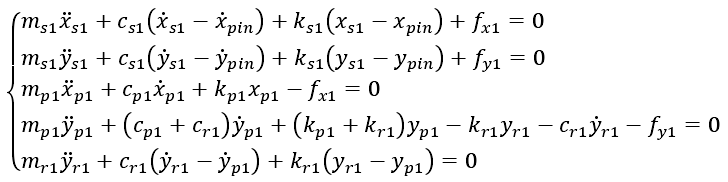
3) Motion control equation of driving wheel
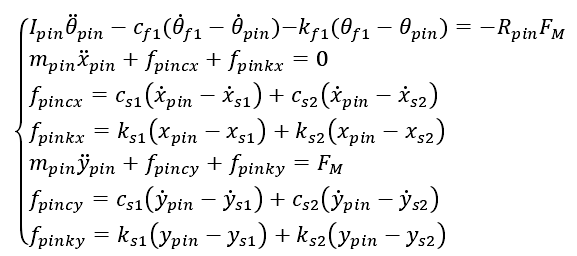
4) Motion control equation of driving wheel support bearing 2
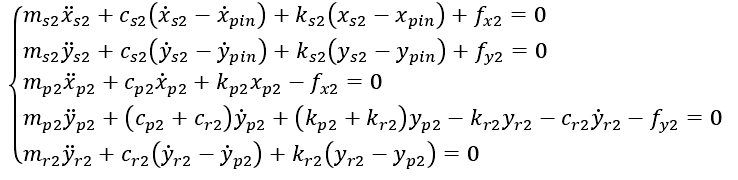
5) Motion control equation of driven wheel bearing 3
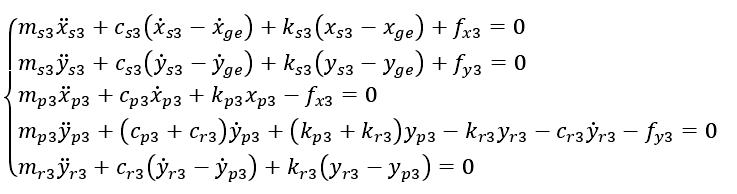
6) Motion control equation of driven wheel
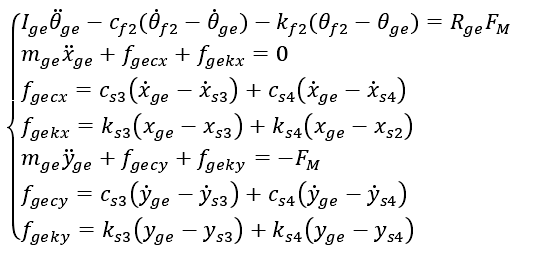
7) Motion control equation of driven wheel bearing 4
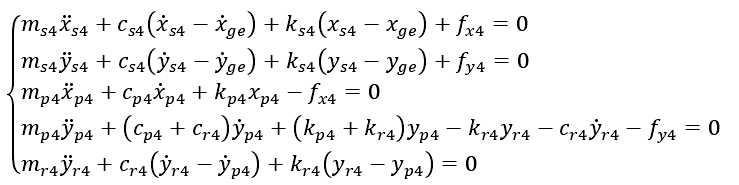
8) Motion control equation of load output shaft

Among them, the meaning of the parameters in the above equation is consistent with the relevant contents in the previous two chapters, and will not be repeated here.