This study investigates the dynamic excitation characterization and robust optimization of high-speed herringbone gear transmission systems. Through systematic modeling and analysis, we propose methodologies to minimize vibration responses while considering manufacturing uncertainties. Key innovations include resonance point identification criteria and a 6σ robust design framework validated through experimental verification.
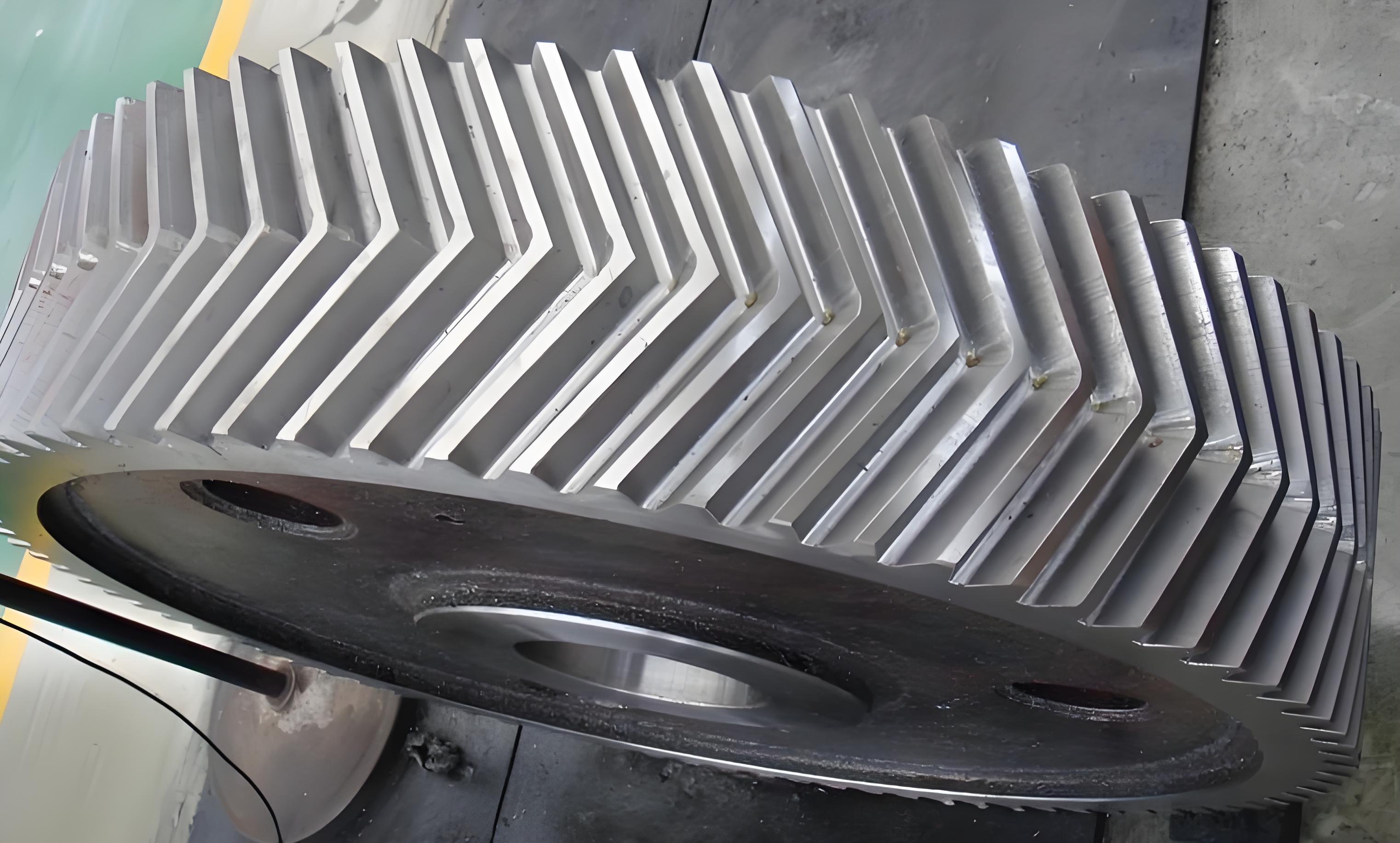
1. Dynamic Excitation Characterization
The time-varying meshing stiffness of herringbone gears is calculated using energy method and validated through FEM. The potential energy components include:
$$U_h = \frac{F^2}{2K_h},\ U_b = \int_0^d \frac{[F_b(d-x) – F_ah]^2}{2EI_x}dx$$
Comparative results show excellent agreement between analytical and numerical methods:
Method | Average Stiffness (N/m) | Computation Time |
---|---|---|
Analytical | 2.68×107 | 15 min |
FEM | 2.72×107 | 4.5 hr |
Transmission error and backlash are modeled as:
$$TE(t) = 0.5f_p \sin(\omega_p t + \phi_p) + 0.5f_m \sin(\omega_m t + \phi_m)$$
$$b(t) = \begin{cases}
b_{max} – \delta(t) & \delta(t) < -b \\
0 & |\delta(t)| \leq b \\
b_{max} + \delta(t) & \delta(t) > b
\end{cases}$$
2. Dynamic Modeling and Vibration Analysis
The flexible multibody dynamics model reveals critical modal characteristics:
Mode | Frequency (Hz) | Damping Ratio | Energy Distribution |
---|---|---|---|
1 | 131.16 | 0.622 | Y-axis swing |
2 | 164.98 | 0.696 | X-axis swing |
3 | 202.49 | 0.645 | Z-axis extension |
Resonance identification criteria are established:
- Frequency principle: $f_{excite} \leq 6f_{shaft}$
- Damping principle: $0 < \zeta < 1$
- Energy principle: $\sum E_{rot} < 1$
3. Robust Optimization Design
The 6σ optimization model minimizes vibration acceleration variance:
$$Minimize\ F = w_1\left(\frac{\mu_y – M}{\Delta M}\right)^2 + w_2\left(\frac{\sigma_y}{\Delta S}\right)^2$$
Design Variable | Initial (mm) | Optimal (mm) | Δ Mass (kg) |
---|---|---|---|
Cover thickness | 14 | 12.5 | -8.2 |
Base thickness | 24 | 22.1 | -12.7 |
Stiffener thickness | 10 | 11.4 | +3.6 |
Optimization results demonstrate significant vibration reduction:
$$a_{RMS}^{optim} = 0.55a_{RMS}^{initial}\ \pm 0.02σ$$
4. Experimental Validation
Prototype testing confirms theoretical predictions:
Parameter | 6000 rpm | Specification |
---|---|---|
Max shaft vibration | 19.1 μm | ≤25 μm |
Noise level | 106.5 dB(A) | ≤110 dB(A) |
Efficiency | 98.86% | ≥98.5% |
The proposed methodology successfully addresses the dynamic challenges in herringbone gear systems through:
- Comprehensive excitation modeling
- Resonance avoidance strategy
- Uncertainty-aware optimization
Future research will focus on thermal-structural coupling effects and multi-objective reliability optimization for enhanced herringbone gear performance in extreme operating conditions.