The splitting angle thickness is one of the important process parameters in the design of tooth concave die, which has an important influence on the cold extrusion forming quality and forming load of spur gear. In order to study the influence of splitting angle thickness t on the forming of spur gear, the numerical simulation is carried out when the splitting angle thickness t is 1mm, 2.5mm, 4mm, 5.5mm and 7mm respectively. The other process parameters are tooth top fillet r = 1.2mm and molding angle α= 45 ° and length of sizing band L = 5mm.
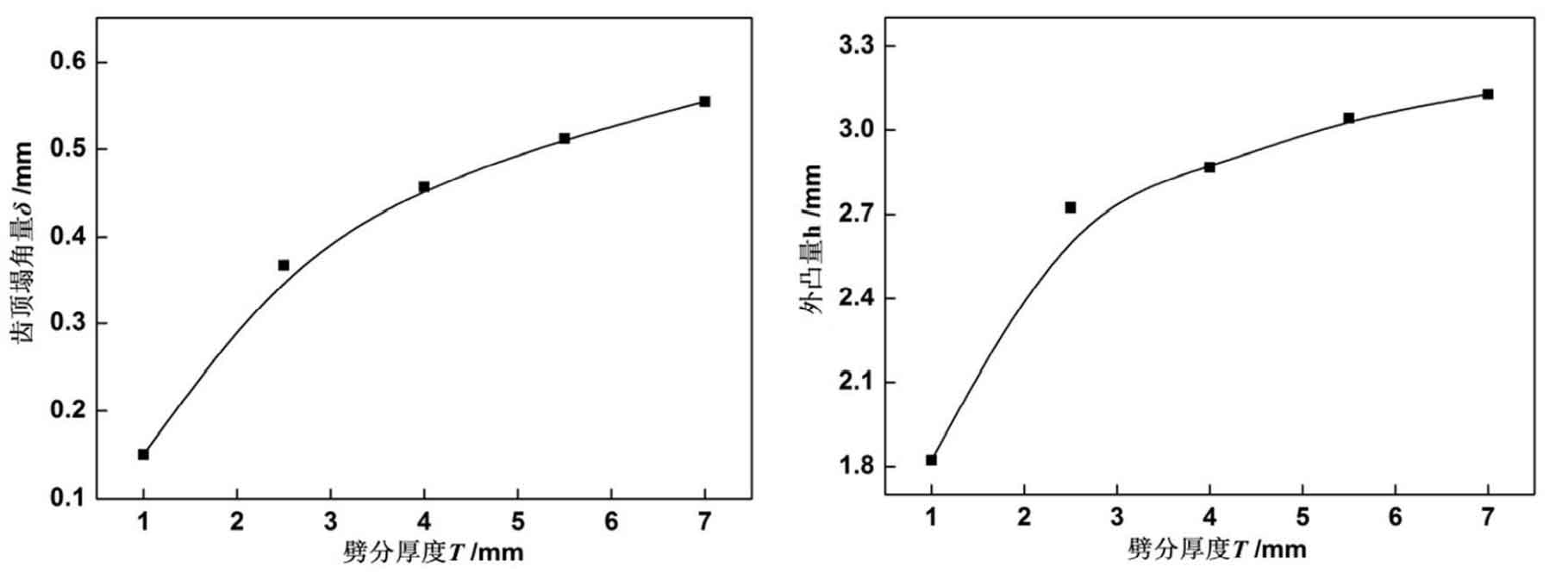
(b) Variation curve of convexity with splitting angle thickness T
Fig. 1 shows the effect of different splitting angle thickness on the forming quality of cold extruded spur gear. The amount of tooth tip collapse angle and end face convexity increase with the increase of splitting angle thickness. That is, with the increase of splitting angle thickness, the forming quality of cold extruded spur gear becomes worse.
Fig. 2 shows the z-direction velocity distribution of cold extrusion forming of spur gear when the splitting angle thickness t = 1mm and 7mm. Cold extrusion forming of spur gear is a complex plastic forming process. The metal flow in the forming process can be divided into radial flow and axial flow according to the flow direction. When the splitting angle thickness is small, the outer metal is easy to be split and enter the tooth shape area of spur gears on both sides, and the axial flow velocity difference between the inner and outer metal is small, as shown in Fig. 2 (a). When the thickness of the splitting angle is large, a conical surface is formed at the die inlet, which has a resistance effect on the axial flow of the metal, and becomes stronger with the increase of the thickness of the splitting angle, so that the flow speed of the outer metal becomes slower and the axial flow speed difference between the inner and outer metal becomes larger, as shown in Fig. 2 (b). The axial flow of the inner and outer metal is uneven, and the inner metal with fast flow has a radial pulling effect on the slower outer metal, resulting in the corner collapse defect of the top of the teeth squeezed into the end first. It can be seen from figure 2 that when the splitting angle thickness t = 1mm, the metal Z-direction flow velocity at the tooth top of spur gear is 27.6mm/sec, the metal Z-direction flow velocity at the inner hole is 33.1mm/sec, and the z-direction flow velocity difference between inner and outer metal is 5.5mm/sec; When the splitting angle thickness t = 7mm, the z-direction flow velocity of metal at the tooth top of spur gear is 24.6mm/sec, the z-direction flow velocity of inner metal is 33.5mm/sec, and the z-direction flow velocity difference of inner and outer metal is 8.9mm/sec. Therefore, the amount of tooth tip collapse and end face convexity of spur gears increase with the increase of splitting angle thickness.
Figure 3 shows the influence law of splitting angle thickness on cold extrusion forming load. The forming load increases with the increase of splitting angle thickness. When the splitting angle thickness t = 1mm, the maximum forming load is about 2171kn, when the splitting angle thickness t = 7mm, the maximum forming load is about 2303kn, and the forming load increases by 5.7%.
To sum up, when the splitting angle thickness is small, the forming quality of spur gear is good and the forming load is small, but too narrow the head of the die inlet will cause insufficient strength at the joint and prone to crushing defects; When the splitting angle thickness is large, the forming load increases and the forming quality is poor. Therefore, the splitting angle thickness should be considered in combination with die service life and forming quality.