When analyzing the performance of worm gears in heavy machinery, two critical factors to consider are efficiency and load capacity. Both of these aspects play a significant role in determining the suitability of worm gears for heavy-duty applications.
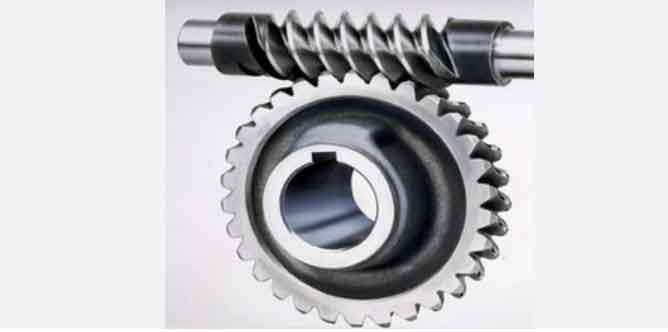
1. Efficiency:
Efficiency refers to the ability of a gear system to transmit power with minimal energy loss. In worm gear systems, there are inherent efficiency losses due to the sliding action between the worm and the gear. This sliding action generates friction, leading to energy dissipation in the form of heat. As a result, worm gears tend to have lower efficiency compared to other gear types, such as spur or helical gears.
In heavy machinery, where power transmission is critical, it’s essential to evaluate the efficiency of the worm gear system. Manufacturers often incorporate measures like high-quality materials, precision manufacturing, and proper lubrication to improve efficiency and reduce energy losses.
2. Load Capacity:
Load capacity is a crucial consideration in heavy machinery, as these applications involve transmitting high levels of torque and loads. The load capacity of a worm gear system depends on factors such as the gear materials, tooth design, and lubrication.
Worm gears are known for their excellent load-carrying capacity in applications with shock loads and heavy-duty requirements. The large contact area between the worm and gear teeth allows for higher load distribution, enhancing the overall strength of the gear set.
However, it’s crucial to consider factors like tooth wear and potential pitting due to high loads and sliding motion. Adequate lubrication and material selection can help improve the load-carrying capacity and overall durability of the worm gear system.
Performance Optimization:
To optimize the performance of worm gears in heavy machinery, several strategies can be employed:
- Material Selection: Choosing high-strength and wear-resistant materials for the worm and gear can enhance load-carrying capacity and overall durability.
- Tooth Profile Optimization: The design of the worm gear teeth can significantly impact its performance. Ensuring proper tooth geometry, such as helix angle and tooth profile, can help minimize friction and improve efficiency.
- Lubrication: Proper lubrication is critical for reducing friction and wear between the worm and gear. The right lubricant and maintenance schedule can significantly affect the longevity and efficiency of the worm gear system.
- Manufacturing Precision: Precision manufacturing processes ensure accurate tooth profiles and gear meshing, resulting in smoother operation and reduced wear.
- Backlash Compensation: Backlash, the play between the worm and gear teeth, can be minimized through proper design and manufacturing to improve precision and performance.
Worm gears have proven to be effective in heavy machinery applications due to their load-carrying capacity, compact design, and ability to transmit power at right angles. However, engineers should carefully assess factors like efficiency and load capacity, and employ appropriate optimization strategies to ensure the worm gear system meets the demanding requirements of heavy machinery.