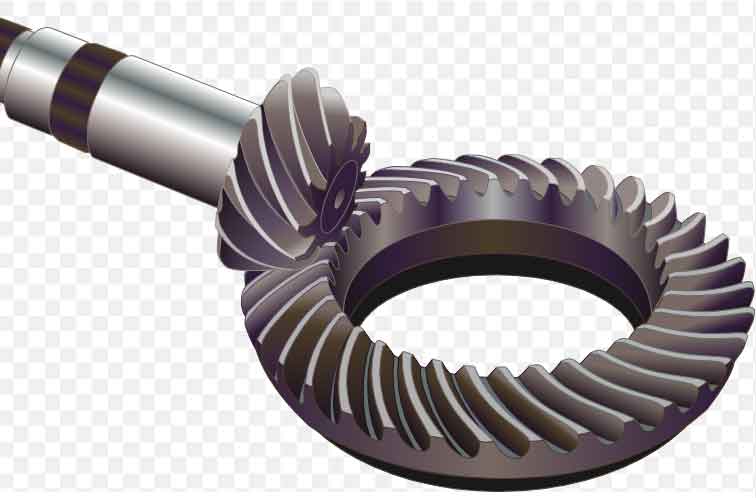
Efficiency and load capacity are critical performance factors in spiral bevel gear drives. Spiral bevel gears are designed to transmit power between intersecting shafts at right angles and must efficiently handle the loads applied to them. Let’s explore how efficiency and load capacity are influenced in spiral bevel gear drives:
1. Efficiency:
Efficiency is a measure of how well a gear drive converts input power to output power, with minimal energy losses due to friction and other factors. Several factors affect the efficiency of spiral bevel gear drives:
- Tooth Profile Design: The tooth profile of spiral bevel gears allows for gradual tooth engagement, resulting in smoother meshing compared to straight bevel gears. This reduces impact loads and friction, contributing to higher efficiency.
- Manufacturing Quality: High-precision manufacturing techniques, such as gear grinding and CNC machining, ensure tight tolerances and smooth gear surfaces. Properly machined gears result in improved efficiency due to reduced friction and more accurate tooth contact.
- Lubrication: Proper lubrication is essential for minimizing friction between gear teeth and promoting smooth gear operation. Adequate lubrication reduces power losses due to friction, enhancing gear efficiency.
- Backlash Control: Tight control of backlash, the space between meshing gear teeth, reduces energy losses due to clearance in the gear system, improving efficiency.
- Alignment: Accurate alignment of spiral bevel gears ensures proper tooth engagement, reducing unnecessary energy losses and improving overall efficiency.
2. Load Capacity:
Load capacity refers to a gear’s ability to handle the applied loads without failure or excessive wear. Spiral bevel gears are known for their high load-carrying capacity, making them suitable for heavy-duty applications. Several factors influence the load capacity of spiral bevel gear drives:
- Curved Tooth Design: The curved tooth profile of spiral bevel gears increases tooth contact area compared to straight bevel gears. This allows for better load distribution and higher load-carrying capacity.
- Material Selection: Choosing high-strength materials and applying proper heat treatment processes enhances gear strength and wear resistance, increasing load capacity.
- Surface Hardening: Surface-hardening processes like carburizing and quenching create a harder surface layer on the gear teeth, improving their resistance to wear and fatigue under high loads.
- Gear Quality: Precision manufacturing techniques ensure the gears have accurate tooth profiles and smooth surfaces, which are essential for reliable performance under heavy loads.
- Tooth Filleting: Incorporating fillets at the tooth roots reduces stress concentrations, enhancing the gear’s resistance to bending and fatigue failure.
- Gearbox Design: The overall gearbox design and system integration play a role in load distribution across multiple gears, ensuring balanced loading and increasing the overall load capacity of the system.
By focusing on efficiency and load capacity considerations during the design and manufacturing processes, engineers can optimize spiral bevel gear drives for their intended applications, delivering high-performance and reliable power transmission solutions.