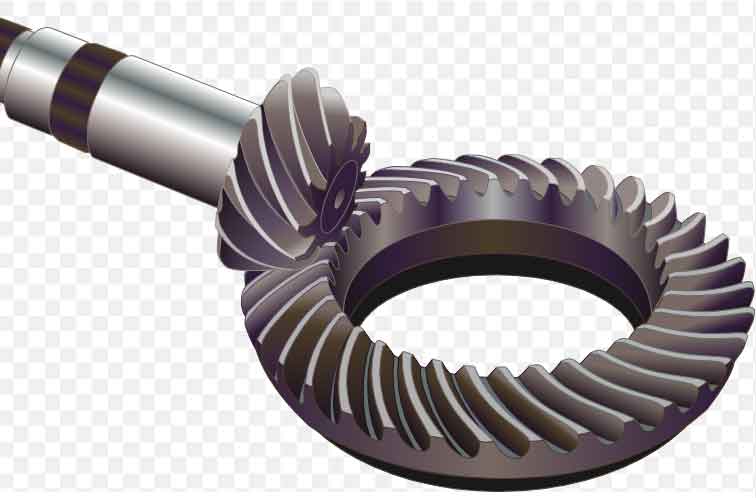
Spiral bevel gears offer several advantages, particularly in terms of efficiency and noise reduction, making them a preferred choice in various high-performance gear systems. Let’s explore these advantages in detail:
1. Efficiency:
- Smooth Tooth Engagement: Spiral bevel gears have a curved tooth design that allows for gradual tooth engagement during meshing. This gradual engagement reduces impact and sliding friction between gear teeth, leading to higher gear meshing efficiency compared to straight bevel gears. The smooth tooth engagement minimizes energy losses and enhances overall system efficiency.
2. Load Distribution and Strength:
- The spiral tooth design enables multiple teeth to be in contact simultaneously, resulting in improved load distribution across the gear teeth. This load-sharing capability enhances the gear’s load-carrying capacity and strength, making spiral bevel gears suitable for heavy-duty applications with high torque and radial loads.
3. Noise Reduction:
- Smooth and Quiet Operation: The gradual tooth engagement of spiral bevel gears reduces noise and vibration during meshing. The curved tooth profile allows for a more uniform distribution of forces, leading to smoother operation and quieter gear performance compared to straight bevel gears. This makes them particularly suitable for applications where noise reduction is essential, such as in automotive differentials, robotics, and aerospace systems.
4. Misalignment Tolerance:
- Forgiving to Misalignments: Spiral bevel gears are more forgiving to misalignments compared to straight bevel gears. The spiral tooth design compensates for minor misalignments between gear shafts, reducing the likelihood of gear tooth interference and increasing the overall reliability of the gear system.
5. Versatility:
- Various Tooth Forms: Spiral bevel gears can be designed with various tooth forms, such as Gleason and Klingelnberg systems, to accommodate different manufacturing methods and specific application requirements. This versatility allows for customization and optimization of gear designs based on the intended use.
6. Aerospace and Automotive Applications:
- In aerospace and automotive applications, where efficiency, noise reduction, and precision are critical, spiral bevel gears are commonly used. They provide reliable and efficient power transmission, contributing to improved performance, handling, and comfort in aircraft, helicopters, and automobiles.
7. High Torque Transmission:
- Spiral bevel gears can handle high torque loads, making them suitable for applications that require robust power transmission capabilities, such as heavy machinery, mining equipment, and high-performance robotic systems.
Spiral bevel gears offer distinct advantages in terms of efficiency and noise reduction. Their smooth tooth engagement, load-carrying capacity, and misalignment tolerance make them efficient and reliable choices for various high-performance gear systems. Additionally, their versatility and ability to handle high torque loads make them well-suited for a wide range of applications in industries like aerospace, automotive, robotics, and industrial machinery.