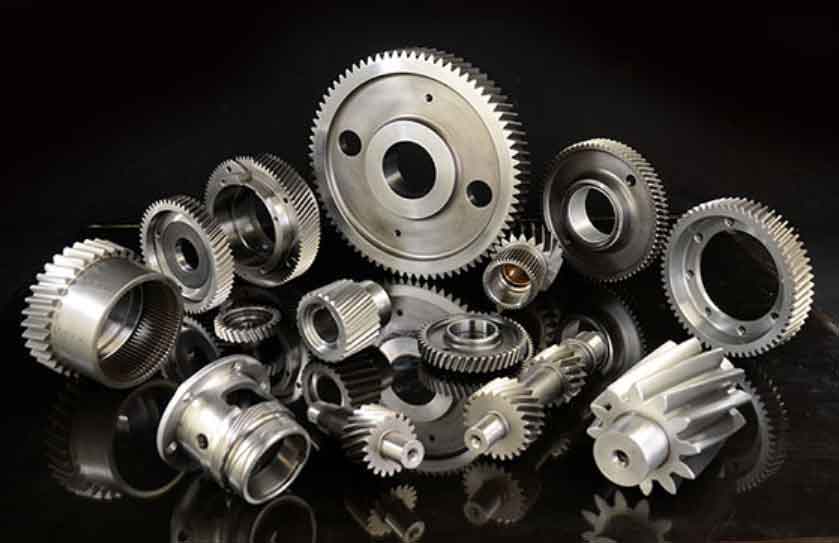
Helical gears offer several advantages, including increased efficiency and noise reduction, which make them a popular choice in various mechanical applications. Let’s explore these advantages in more detail:
1. Efficiency:
- Smooth Tooth Engagement: The helical tooth profile allows for gradual contact between the gear teeth, resulting in smoother meshing compared to spur gears. This smooth engagement minimizes impact and vibration, leading to reduced energy losses and improved efficiency.
- Load Distribution: The helix angle of helical gears enables multiple teeth to be in contact at the same time, distributing the load across more teeth. This load-sharing characteristic enhances the gear’s load-carrying capacity and reduces stress on individual teeth, leading to improved efficiency.
- Reduced Sliding Contact: Unlike spur gears, helical gears have a sliding contact between the teeth during meshing. This sliding motion is less prevalent in helical gears due to the helix angle, resulting in lower friction and energy losses, further contributing to increased efficiency.
2. Noise Reduction:
- Gradual Tooth Engagement: The helical tooth profile reduces the impact of tooth engagement, resulting in less noise during gear meshing compared to spur gears. The gradual meshing reduces the abrupt contact between teeth, thereby minimizing noise.
- Overlapping Teeth: Helical gears have overlapping teeth, which increases the number of teeth in contact at any given moment. This overlap distributes the load and helps to spread noise more evenly, contributing to noise reduction.
- Helix Angle Direction: In some cases, using opposite helix angles in paired helical gears (e.g., right-hand and left-hand helical gears) can further cancel out noise and vibration.
3. Lubrication and Maintenance:
- Proper lubrication is essential for the efficient operation of helical gears. Adequate lubrication reduces friction, wear, and heat generation, ensuring smooth operation and preventing premature failure.
- Regular maintenance, including gear inspection and proper alignment, helps maintain the efficiency and longevity of helical gear systems.
4. Applications:
- Helical gears are commonly used in applications where smooth and efficient power transmission is crucial, such as automotive transmissions, industrial machinery, robotics, and marine propulsion systems.
- They are particularly suitable for applications requiring high torque, precision motion control, and quiet operation.
While helical gears offer numerous advantages, it’s important to note that they also have some limitations, such as the axial thrust generated due to the helix angle, which requires appropriate thrust bearings for proper gear alignment. However, overall, their efficiency, load-carrying capacity, and noise reduction capabilities make helical gears an excellent choice for various engineering and mechanical systems.