Spiral bevel gears offer several advantages, including efficiency and noise reduction, making them a popular choice in various engineering applications. Let’s explore these advantages in detail:
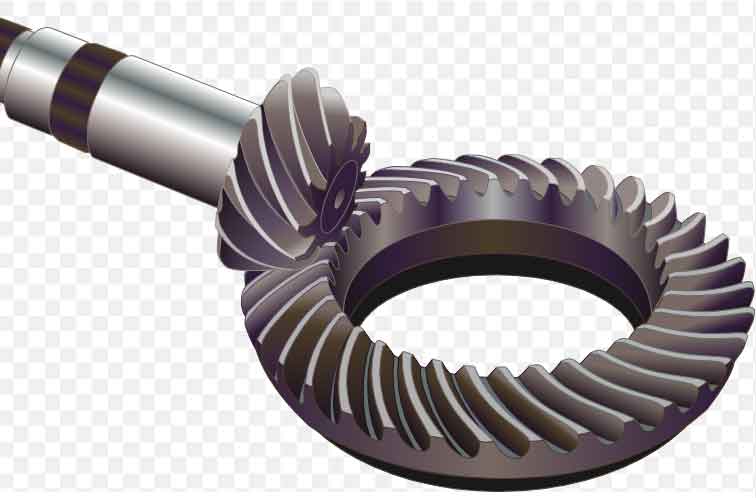
1. Efficiency:
The helical tooth design of spiral bevel gears allows for a larger contact area between gear teeth during meshing. This increased contact area results in a smoother and more gradual transfer of power, reducing the risk of tooth impact and improving power transmission efficiency. Compared to straight bevel gears, spiral bevel gears can handle higher loads and transmit power more efficiently.
2. Load Distribution:
The spiral design of the teeth in spiral bevel gears enables better load distribution along the tooth face during operation. This helps to minimize concentrated stress points and improves the gear’s ability to handle heavy loads. As a result, spiral bevel gears are often preferred for high-torque applications, such as in automotive differentials and industrial gearboxes.
3. Noise Reduction:
The gradual meshing action of spiral bevel gears reduces impact and vibration, leading to quieter gear operation. The helical teeth engagement spreads the load over multiple teeth, reducing noise levels compared to straight bevel gears, which can experience higher impact forces during meshing. The noise reduction is especially advantageous in applications where noise levels need to be minimized, such as in automotive drivetrains and precision machinery.
4. Smoother Operation:
The helical design of the teeth in spiral bevel gears results in smoother and more continuous gear engagement. This results in reduced gear chatter and vibration during operation, leading to smoother gear motion and improved overall system performance.
5. High Precision:
Spiral bevel gears are known for their high precision and accuracy. The design allows for precise gear tooth profiling and alignment, ensuring smooth meshing and consistent performance.
6. Versatility:
Spiral bevel gears can be designed with various helix angles to suit specific application requirements. This makes them versatile for a wide range of gear ratios and torque requirements in different engineering applications.
7. Durability:
Due to their enhanced load-carrying capacity and reduced tooth impact, spiral bevel gears are generally more durable and have a longer service life compared to other gear types.
8. Heat Dissipation:
The helical tooth design facilitates better heat dissipation, reducing the risk of overheating during prolonged operation, which is particularly crucial in high-power applications.
These advantages make spiral bevel gears a preferred choice in many critical applications, including automotive transmissions, industrial gearboxes, aerospace systems, and more. The combination of efficiency, noise reduction, and smooth operation ensures optimal gear performance, contributing to the overall reliability and functionality of the systems they are integrated into.