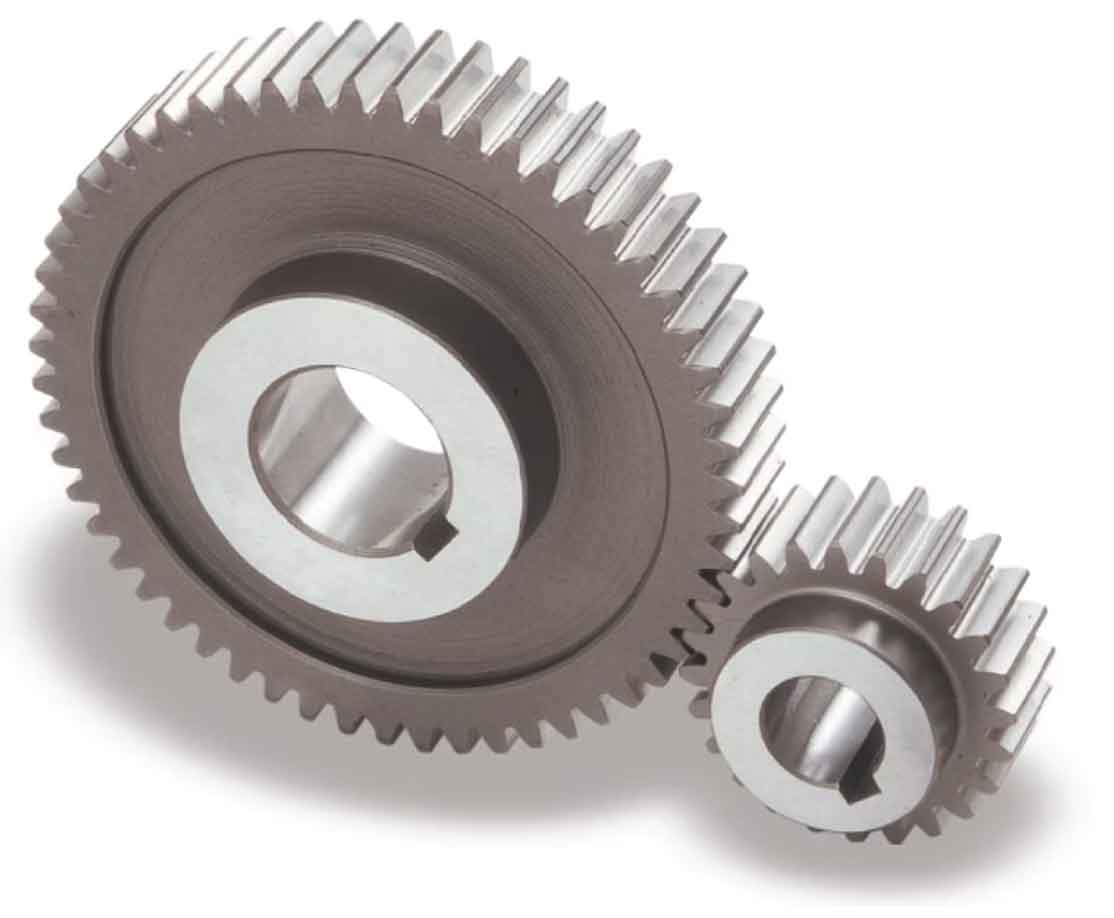
Spur gears offer several advantages in terms of efficiency and power transmission, making them a popular choice for various industrial applications. Here are the key advantages of spur gears:
- Simple Design: Spur gears have a straightforward and uncomplicated design with straight teeth that are parallel to the axis of rotation. This simplicity makes them easy to manufacture and assemble, resulting in lower production costs.
- High Efficiency: Spur gears have high mechanical efficiency, typically ranging from 94% to 98%. This efficiency is due to their straight teeth and smooth meshing, resulting in minimal energy loss during power transmission.
- Constant Speed Ratio: Spur gears maintain a constant speed ratio between the driving and driven shafts, ensuring accurate and consistent motion transfer.
- Linear Motion Transfer: The teeth of spur gears mesh along the line of action, which provides a smooth and uniform transfer of power between the gears.
- No Axial Thrust: Spur gears do not generate axial thrust, as the teeth are parallel to the axis of rotation. This characteristic reduces the need for additional bearings or thrust washers in gearboxes, simplifying the design.
- Wide Range of Applications: Spur gears are used in a broad range of applications, from simple machinery to heavy industrial equipment, clocks, and watches. Their versatility makes them suitable for various speed and torque requirements.
- Cost-Effective: Due to their straightforward manufacturing process and common use, spur gears are cost-effective and readily available in the market.
- Customization Options: While spur gears have a standard tooth profile, they can be customized to fit specific application requirements by altering the tooth pitch, module, pressure angle, and number of teeth.
- Easy Maintenance: Spur gears are relatively easy to inspect, replace, and maintain, which contributes to their overall reliability and serviceability.
- Quiet Operation: Spur gears can operate quietly when designed and lubricated correctly. They produce less noise compared to other gear types such as bevel gears.
Despite their numerous advantages, spur gears also have limitations. They are not suitable for transmitting power between non-parallel shafts, and they may exhibit a relatively high amount of backlash, which can affect precision in some applications. Additionally, when transmitting high torque or operating at high speeds, designers often consider other gear types, such as helical gears or bevel gears, to address specific application requirements.
Spur gears are an excellent choice for power transmission in many applications due to their simplicity, efficiency, and ability to handle moderate loads and speeds effectively.