Precision forging techniques can be employed to enhance gear strength and achieve even higher levels of performance. These techniques involve careful control of the forging process to optimize the material properties, grain structure, and dimensional precision of the gears. Here are some precision forging techniques that can be used to enhance gear strength:
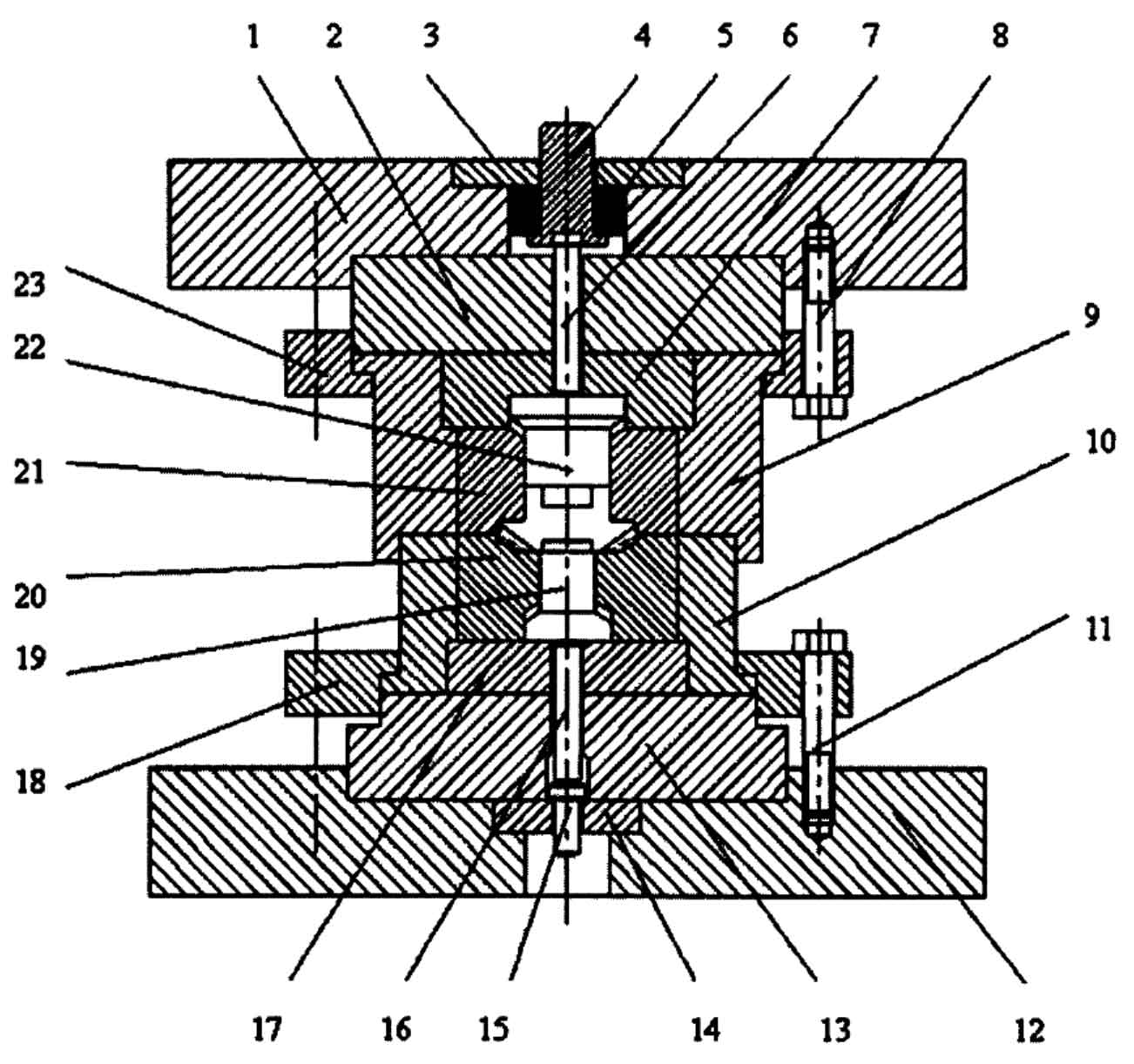
- Closed-Die Forging: Closed-die forging, also known as impression-die forging, is a precision forging technique that involves the use of shaped dies to impart the desired gear shape. This technique allows for better control over the forging process, resulting in improved dimensional accuracy and tighter tolerances. The use of closed-die forging ensures that the gear achieves precise tooth profiles and accurate dimensions, enhancing its overall strength and performance.
- Warm Forging: Warm forging involves forging the gear at a temperature below the recrystallization temperature of the material but above room temperature. This technique allows for better material flow and deformation during forging, resulting in refined grain structure and improved mechanical properties. Warm forging can increase the strength and toughness of the gear, making it more resistant to wear, fatigue, and other forms of mechanical stress.
- Isothermal Forging: Isothermal forging is a precision forging technique that involves maintaining the workpiece and dies at a constant temperature throughout the forging process. This helps in minimizing temperature variations and thermal gradients within the material, leading to improved consistency in the microstructure and mechanical properties of the gear. Isothermal forging can result in gears with enhanced strength, fatigue resistance, and dimensional stability.
- Grain Flow Optimization: Precision forging techniques focus on optimizing the grain flow of the material during forging. This involves controlling the direction and orientation of the grain structure to align it with the principal stress directions experienced by the gear during operation. By ensuring a favorable grain flow, the gear’s strength, fatigue resistance, and load-carrying capacity can be significantly enhanced.
- Post-Forging Heat Treatment: After precision forging, heat treatment processes such as quenching and tempering can be applied to further enhance the gear’s strength and hardness. Heat treatment helps in refining the microstructure, relieving internal stresses, and achieving the desired material properties. It improves the gear’s resistance to wear, fatigue, and other forms of mechanical degradation.
- Process Monitoring and Control: Precision forging techniques often involve advanced process monitoring and control systems to ensure consistent and optimized production. Real-time feedback on process parameters such as temperature, pressure, and deformation can be utilized to adjust and fine-tune the forging conditions. This helps in maintaining the desired material properties, dimensional precision, and overall gear strength.
By employing these precision forging techniques, gear manufacturers can achieve gears with enhanced strength, improved fatigue resistance, and higher performance capabilities. These techniques enable the production of gears that can withstand demanding operating conditions, provide efficient power transmission, and have an extended operational lifespan.