For the process of precision forging the driven spiral bevel gear of automobile rear axle at different temperatures, the distribution law of equivalent stress is basically the same. After the upper die starts moving, the part with the largest equivalent stress is mainly distributed in the part where the blank is in contact with the upper and lower dies. With the downward movement of the upper die, the equivalent stress in the middle part gradually increases and enters the stage dominated by upsetting deformation. In this process, the equivalent stress is evenly distributed, And the value of equal effect force is relatively large. After the upsetting process, it enters the deformation stage dominated by tooth formation. In this process, the metal in the tooth shape flows from the small end of spiral bevel gear to the big end of gear, and the equivalent stress at the tooth shape is large. When the metal flows to the big end, the blank basically fills the whole die cavity. At this time, it enters the stage of forming flash, and the excess metal flows to the flash groove under large compressive stress, At this time, the equivalent pressure of the metal outside the whole blank is basically the same, but the equivalent stress of the metal inside the blank is small.
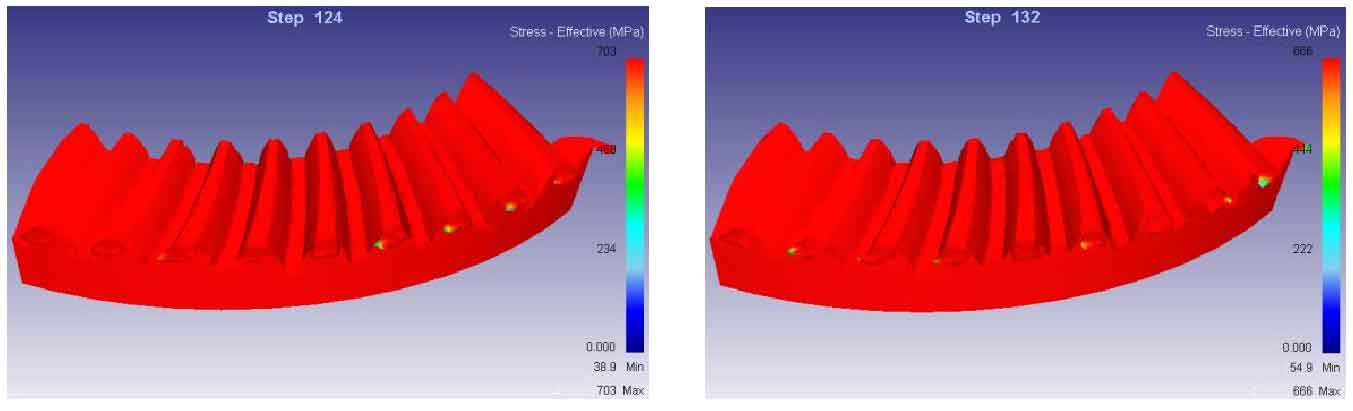
(c) Equivalent stress distribution diagram of final step when forming temperature is 400 ℃
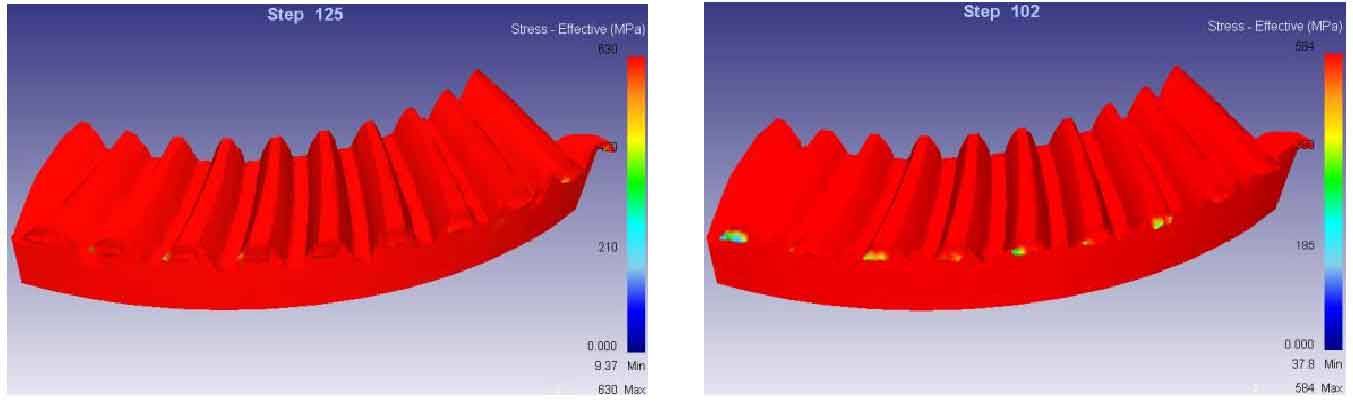
(e) Equivalent stress distribution diagram of final step when forming temperature is 600 ℃
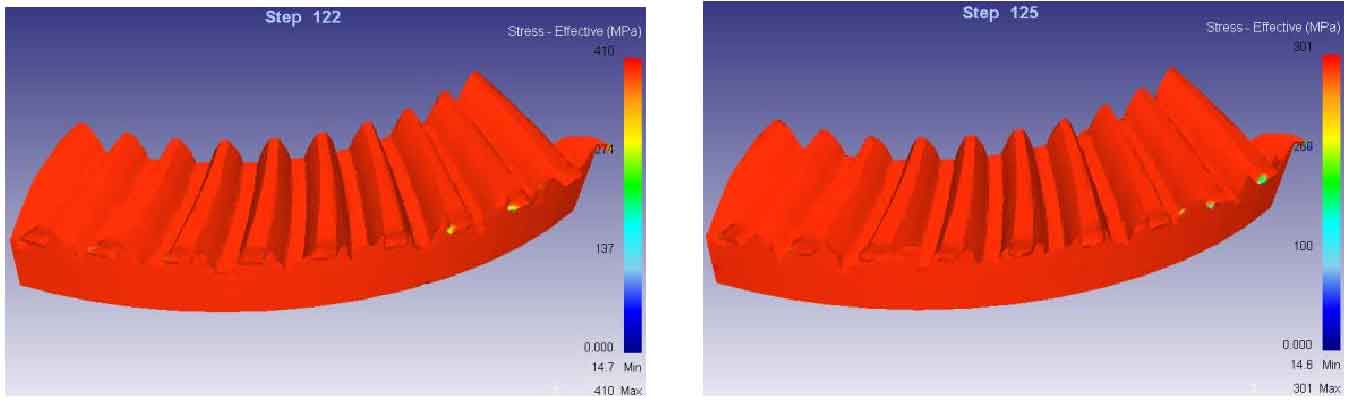
(g) Equivalent stress distribution diagram of final step when forming temperature is 800 ℃
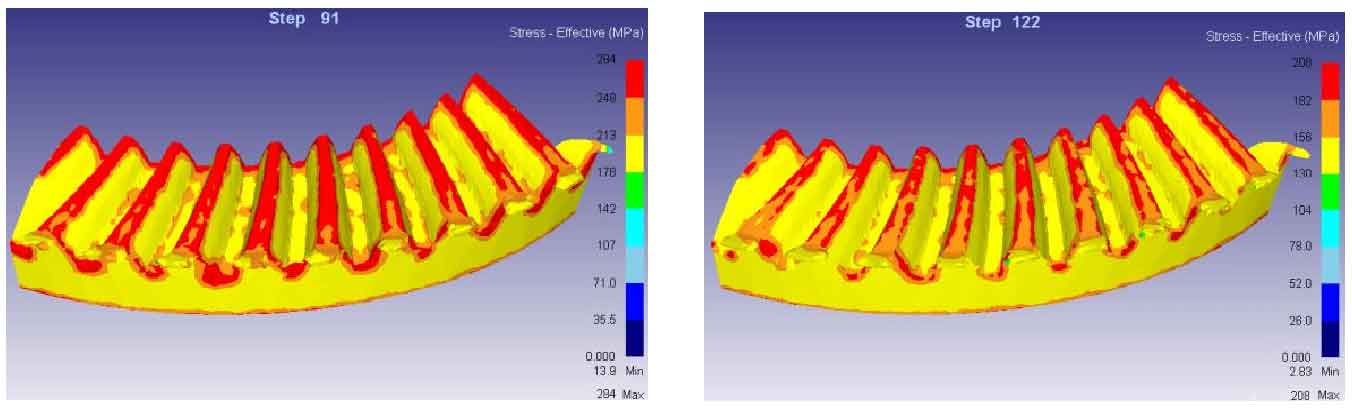
(i) Equivalent stress distribution diagram of final step when forming temperature is 1000 ℃
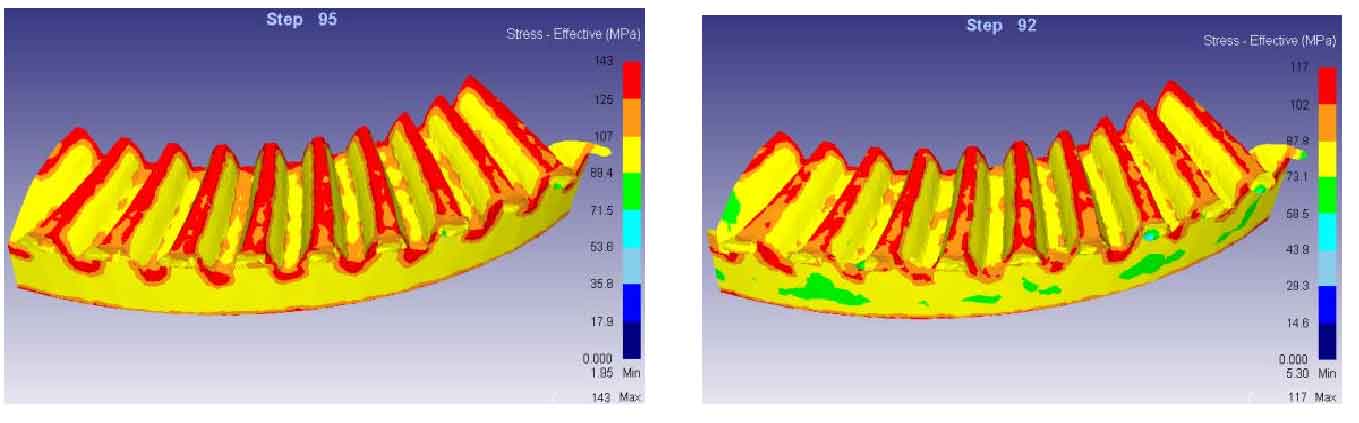
(k) Equivalent stress distribution diagram of final step when forming temperature is 1200 ℃
The maximum equivalent stress under different forming temperatures is different. For cold machining and warm machining, the maximum equivalent stress basically occurs when the mold is closed, that is, the final step of simulation. Figure 1 shows the equivalent stress distribution diagram of the final step at different temperatures, in which (a) is the equivalent stress distribution diagram of the final step of cold machining, (b) (c) (d) (E) (f) (g) is the equivalent stress distribution diagram of the final step at different temperatures of warm machining, and (H) (I) (J) (k) is the equivalent stress distribution diagram of the final step at different temperatures of hot machining. It can be seen from Figure 1 that the equivalent stress distribution in the final step of cold machining and warm machining is relatively uniform, while in terms of hot machining, the place with the largest equivalent stress in the final step is mainly distributed on the tooth top surface of spiral bevel gear, and the equivalent stress in the rest is relatively small.
Fig. 2 is the relationship curve between the maximum equivalent stress and temperature of spiral bevel gear. It can be seen from Fig. 2 that the maximum equivalent stress decreases gradually with the increase of temperature. There is a basically linear relationship between the maximum equivalent stress and temperature at 20 ~ 600 ℃, and the maximum equivalent stress at 600 ~ 800 ℃ decreases rapidly with the increase of temperature. The slope of the curve is much greater than that at 20 ~ 600 ℃. 900 ~ 1200 ℃ belongs to the hot working stage. At this time, the maximum equivalent stress also decreases with the increase of temperature, and its downward trend decreases slightly. With the increase of temperature, the plasticity of metal will gradually increase and its yield strength will gradually decrease, so the equivalent stress will be reduced, making the forming easier. It can be seen from the figure that the maximum equivalent stress decreases most obviously at 600 ~ 800 ℃ in the warm processing stage, while the processing temperature of warm processing is relatively low compared with hot processing, so it is not easy to produce the phenomenon that the metal of spiral bevel gear blank is oxidized.