In the field of mechanical manufacturing, the accuracy of gear processing is of great significance for the performance and reliability of mechanical equipment. Helical gears are widely used in various mechanical transmissions due to their advantages such as smooth transmission, high load-carrying capacity, and low noise. However, the processing of helical gears is more complex than that of straight gears, and the synchronization error in the processing process has a significant impact on the machining accuracy. Therefore, it is essential to study the error compensation method for helical gear hobbing processing to improve the machining accuracy and quality of helical gears.
The background and significance of this research lie in the need to improve the machining accuracy of helical gears in the high-speed dry hobbing process. The traditional error compensation methods have certain limitations, and the complex motion relationship and unstable processing conditions of helical gear processing make it difficult to achieve effective error compensation. The wavelet packet algorithm can perform multi-resolution analysis of signals, which provides a new approach for error compensation in helical gear processing.
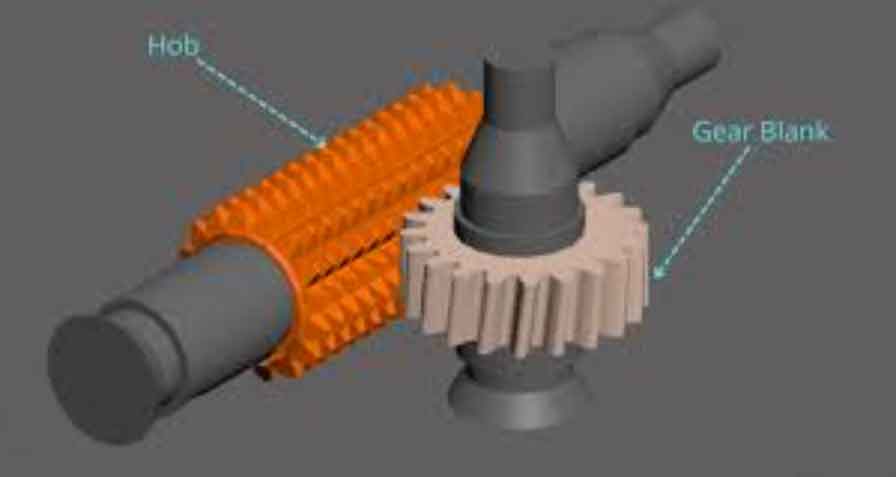
Previous studies on gear processing error compensation have mainly focused on the establishment of error models and the use of neural networks or other methods for error prediction and compensation. However, these methods often do not consider the multi-resolution characteristics of the error signals and the influence of complex processing conditions. The application of wavelet packet algorithms in gear processing error compensation is still in its initial stage, and further research is needed to explore its effectiveness and feasibility.
The main content of this research includes the analysis of the structure and motion relationship of the hobbing machine, the composition and acquisition of the synchronization error signal, the reconstruction and decoupling of the synchronization error using the wavelet packet algorithm, and the test and verification of the error compensation.
- Hobbing Machine Structure and Axis Motion Relationship
- Machine Structure: The YK3126 vertical CNC hobbing machine consists of 6 control axes, including 3 moving axes (X, Y, Z) and 3 rotating axes (A, B, C). Each axis is driven by a separate motor, and the functions of each servo axis are described.
- Motion Relationship in Helical Gear Processing: When processing helical gears, in addition to the B – C axis linkage, the Z – C axis linkage is also required. The linkage relationship of the driven axis C in helical gear processing is given by Equation (1), and the specific parameters and values are shown in Table 1.
Table 1 | Helical Gear and Hob Processing Related Parameters | ||
---|---|---|---|
Parameter | Value | Parameter | Value |
Normal Module (mm) | 3 | Number of Gear Teeth | 59 |
Number of Hob Heads | 3 | Cutting Speed (mm·r⁻¹) | 1.5 |
Pressure Angle (°) | 20 | Feed Amount (mm) | 6.45 |
Hob Rotation Direction | Right – Hand | Hob Speed (r·min⁻¹) | 680 |
Gear Rotation Direction | Right – Hand | Hobbing Method | Reverse Hobbing |
- Synchronization Error Signal Composition and Acquisition
- Error Signal Composition: The synchronization error in helical gear processing is defined as the difference between the coupled theoretical rotational angular displacement of the additional rotation of the C axis caused by the rotational motion of the B axis and the axial movement of the Z axis and the actual rotational angular displacement of the C axis.
- Signal Acquisition: The absolute encoder (Encoder – C) installed on the C axis is used to measure the angular displacement of the C axis. The synchronization error data (register number D50) is collected using the HNC – SSTT software, which is a signal acquisition software developed by Huazhong CNC Group. The data is transmitted to the PC for real – time display and monitoring of the processing state.
- Synchronization Error Reconstruction and Compensation Test Verification
- Definition of Wavelet Packet: The wavelet packet analysis is a time – frequency localization analysis method that can subdivide the frequency of the wavelet subspace Wj in a binary manner to improve the frequency resolution. The orthogonal wavelet packet is defined based on the sequence {hn} and the scale function φ(t) and the wavelet function φ(t).
- Synchronization Error Reconstruction and Decoupling: The collected synchronization error signal is decomposed and reconstructed using the wavelet packet algorithm. After error feature identification, the error components containing valid information are extracted for synchronization error reconstruction. The signal is decomposed into 8 sub – frequency bands, and the main error components are concentrated in the 0th and 3rd nodes. The reconstructed synchronization error signal has a significantly lower amplitude than the original signal. According to the linear superposition principle, the synchronization error is decoupled to the B axis and the Z axis, and the error is redistributed for compensation.
- Test and Verification of Synchronization Error Compensation: The synchronization error compensation model using the wavelet packet decomposition and reconstruction algorithm is shown in Figure 7. The electronic gearbox code is written, and the NC code is modified for error compensation. The gear accuracy after processing is detected using the Klingelnberg gear measuring center, and the comparison of tooth profile and tooth direction accuracy before and after error compensation is shown in Table 3. The results show that the machining accuracy of the gear is improved after error compensation.
Table 3 | Comparison of Tooth Profile and Tooth Direction Accuracy Before and After Error Compensation | ||
---|---|---|---|
Error Fα (μm) | Error Fβ (μm) | ||
Left Tooth Surface | 17.8 | 23.0 | |
Before Compensation | 12.1 | 18.0 | |
8.3 | 17.0 | ||
7.7 | 10.0 | ||
Right Tooth Surface | 7.1 | 5.8 | |
13.0 | 12.9 | ||
Left Tooth Surface | 8.9 | 9.3 | |
After Compensation | 11.5 | 15.3 | |
10.4 | 15.1 | ||
5.4 | 6.2 | ||
Right Tooth Surface | 8.1 | 4.8 | |
6.2 | 4.5 |
The main conclusions of this research are as follows:
- The wavelet packet decomposition and reconstruction algorithm is proposed for multi – resolution analysis of the synchronization error of helical gear processing collected by Huazhong HNC – SSTT.
- The reconstructed synchronization error is decoupled to the servo axis according to the linear superposition principle, and the NC code is modified for processing verification on the Qinchuan YK3126 CNC hobbing machine. The error compensation effect is obvious.
- The use of the wavelet packet method provides a new approach for error compensation in the processing of high – speed dry helical gears.
However, this research also has some limitations. For example, the selection of the wavelet packet basis function and the decomposition level may affect the accuracy of the error reconstruction. Future research could focus on optimizing these parameters and further improving the performance of the error compensation model.
In conclusion, this research provides a valuable method for improving the machining accuracy of helical gears, which has important implications for the development of the gear manufacturing industry. Further research in this area can lead to more advanced and effective error compensation techniques.