Through theoretical calculation and finite element analysis, the bearing capacity of the double pressure angle asymmetrical spiral bevel gear with modulus of 4.0 and the symmetrical spiral bevel gear with modulus of 4.5 are discussed in this paper. Due to the limited space, the calculation methods of the bending stress of the asymmetric dedendum and the contact stress of the tooth surface are not introduced in this paper, only the calculation results are listed.
Through theoretical calculation and finite element simulation, the tooth surface contact stress and root bending stress of asymmetric spiral bevel gear with module 4 are lower than those of symmetrical gear with module 4.5, so the lightweight asymmetric spiral bevel gear can completely replace the original symmetrical gear.
In order to further verify the fatigue life of unsymmetrical spiral bevel gears, a mechanical double ring closed gear life test-bed is used, and the experimental equipment is shown in the figure.
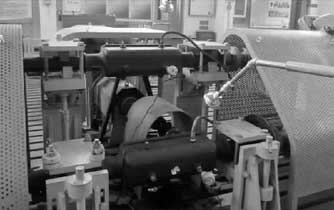
The bench test method of the unsymmetrical spiral bevel gear with double pressure angle is adopted in QC / T 533-1999 standard of the Ministry of mechanical industry of the people’s Republic of China.
The test results are shown in Table 3. It can be seen from table 3 that the minimum life and median life of the double pressure angle asymmetric spiral bevel gear meet the standard requirements through bench test, and the fatigue life is not lower than the original mine reducer symmetrical gear. It is proved that the lightweight asymmetric spiral bevel gear can replace the original symmetrical gear, providing a feasible method for the lightweight technology of mine reducer.
(1) In this paper, the meshing transmission principle and the tooth surface equation of the double pressure angle asymmetric spiral bevel gear are derived. The influence of the asymmetric design on the pressure angle range of the working tooth surface is analyzed. By using the double pressure angle technology wheel, the pressure angle range of the working tooth surface can be effectively increased by about 30%. The tooth shape of spiral bevel gear in reducer is calculated, and the driving wheel and passive wheel of symmetric and asymmetric spiral bevel gear are compared.
(2) The unsymmetrical single-sided cutter head and double-sided cutter head are designed and manufactured, and the unsymmetrical spiral bevel gear with double pressure angle is manufactured. The load-carrying capacity of the unsymmetrical spiral bevel gear is calculated, simulated and tested by the analytical method, the finite element method and the closed gear test-bed, and it is proved that the lightweight unsymmetrical spiral bevel gear can replace the original symmetrical gear.
(3) The results show that the lightweight effect of the unsymmetrical spiral bevel gear is obvious. The weight of the driven wheel is reduced by 37% and that of the driving wheel is reduced by 10%. Considering other parts such as the bearing seat and the case, the total lightweight value is very considerable, which provides a feasible method for the lightweight technology of the mine reducer.