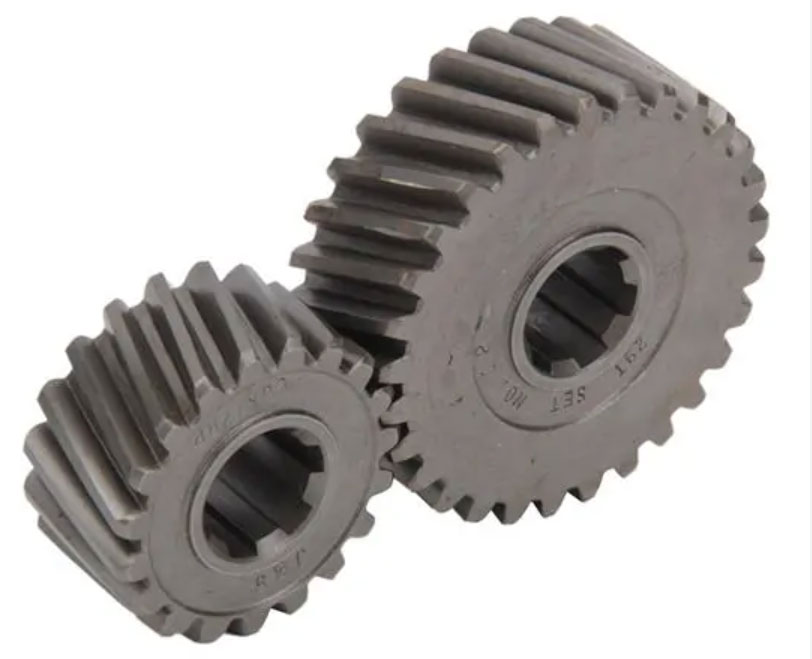
Helical gears are a type of cylindrical gears with angled teeth that form a helix shape around the gear axis. They are widely used in mechanical systems due to their unique design and functionality. Let’s explore the key aspects of the design and functionality of helical gears in mechanical systems:
1. Tooth Profile:
Helical gears have teeth with an angled profile that forms a helix shape around the gear axis. The helix angle is the angle between the tooth’s leading edge and a line perpendicular to the gear axis. The angled teeth allow for gradual tooth engagement and provide smoother gear meshing compared to spur gears.
2. Helix Angle:
The helix angle in helical gears determines the degree of the tooth helix and affects the gear characteristics. A higher helix angle results in a greater helix shape and a larger contact area between the teeth. This increases the load-carrying capacity and improves gear meshing characteristics. However, a higher helix angle can also generate more axial thrust and may require additional measures to counteract the thrust.
3. Gear Geometry:
Helical gears have specific geometry that influences their functionality:
- Addendum: The addendum is the radial distance from the gear pitch circle to the top of the gear tooth. It determines the strength and tooth profile of the gear.
- Dedendum: The dedendum is the radial distance from the gear pitch circle to the bottom of the gear tooth. It provides clearance between the mating gear teeth.
- Pitch Diameter: The pitch diameter is the imaginary circle that passes through the midpoint of the gear teeth. It determines the gear ratio and is used for gear calculations.
- Pressure Angle: The pressure angle is the angle between the gear tooth profile and a line perpendicular to the gear axis at the point of contact. Common pressure angles for helical gears are 14.5° and 20°.
4. Contact Ratio:
Helical gears have a higher contact ratio compared to spur gears. The contact ratio refers to the number of teeth in contact at any given time during gear meshing. The increased contact ratio improves load distribution and reduces stress on individual teeth, resulting in smoother operation and improved overall gear performance.
5. Functionality:
Helical gears function by transmitting rotational motion and torque between parallel or intersecting shafts. They offer advantages such as:
- Power Transmission: Helical gears efficiently transmit power from one shaft to another, allowing for speed reduction or torque multiplication.
- Smooth Operation: The inclined tooth engagement of helical gears provides smoother and quieter operation compared to spur gears, reducing noise and vibration.
- Load Distribution: The helical tooth profile distributes the load over multiple teeth, resulting in higher load-carrying capacity and improved gear performance.
- Precise Speed Control: The gradual tooth engagement enables precise speed control, facilitating accurate gear shifting and motion control in mechanical systems.
- Efficiency: The inclined tooth engagement reduces sliding friction, leading to higher gear efficiency compared to other gear types.
Helical gears are widely used in mechanical systems where smooth operation, higher load-carrying capacity, and efficient power transmission are essential. They find application in various industries, including automotive, manufacturing, aerospace, and more. Understanding the design and functionality of helical gears enables engineers to optimize their use and achieve reliable and high-performance mechanical systems.