The manufacturing process of straight bevel gears involves several stages, starting from gear design and culminating in the production of the final gears. Here is an overview of the typical manufacturing process for straight bevel gears:
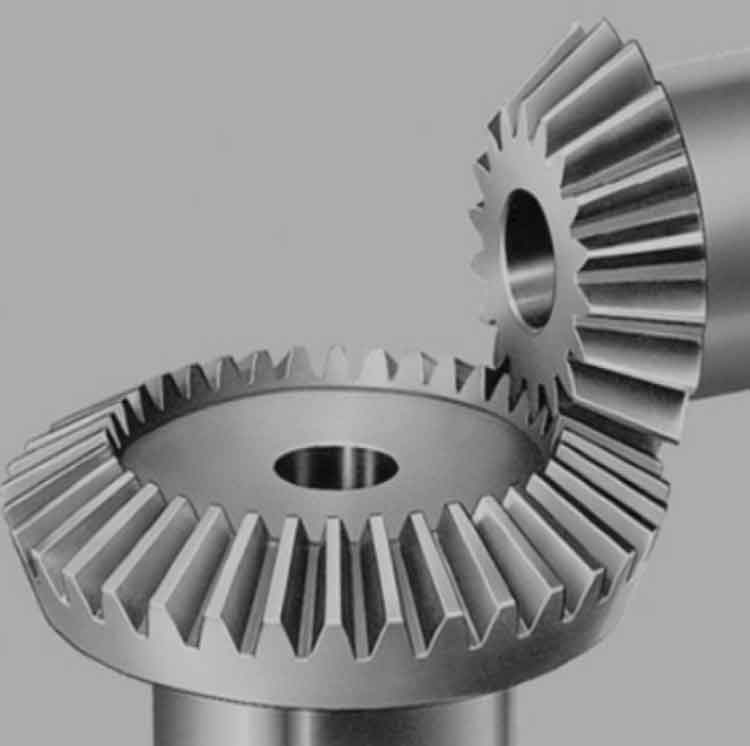
- Gear Design: The first step in manufacturing straight bevel gears is the design phase. This involves determining the gear specifications, such as the gear ratio, tooth size, pitch angle, and material selection. Gear design software or specialized gear design engineers can assist in creating the gear geometry and tooth profiles.
- Material Selection: The choice of material for straight bevel gears depends on the application requirements, load capacity, and operating conditions. Commonly used materials for straight bevel gears include alloy steels, such as 8620 or 9310, as well as stainless steel or other high-strength materials.
- Gear Cutting: The gear cutting process is where the gear teeth are formed on the gear blank. There are several methods used for cutting straight bevel gears:
- Hobbing: Hobbing is a widely used method where a gear hob, a cutting tool with the desired tooth profile, is used to cut the gear teeth. The gear blank and hob rotate in opposite directions, and the hob progressively cuts the teeth into the blank.
- Milling: Milling involves using a milling machine with a specially designed cutter to cut the gear teeth. The gear blank and cutter are mounted on the machine, and the cutter is moved along the gear blank to create the tooth profile.
- Grinding: Gear grinding is a precise method that uses grinding wheels to remove material and shape the gear teeth. This process is often used for high-precision gears where tight tolerances and surface finish are crucial.
- Heat Treatment: After the gear teeth are cut, the gears undergo heat treatment to enhance their hardness, strength, and wear resistance. Heat treatment processes, such as carburizing, quenching, and tempering, are applied to achieve the desired material properties.
- Finishing Operations: Once the gears have undergone heat treatment, they undergo various finishing operations to achieve the required dimensional accuracy and surface finish. These operations may include gear deburring, grinding, honing, and lapping to remove any imperfections and improve the gear quality.
- Quality Control: Throughout the manufacturing process, quality control measures are implemented to ensure the gears meet the specified requirements. This involves inspecting the gear teeth for dimensional accuracy, tooth profile, surface finish, and hardness. Advanced metrology tools, such as coordinate measuring machines (CMMs) and gear measuring instruments, are used for precise measurements and quality assurance.
- Assembly and Testing: After the gears have passed the quality control checks, they are assembled into the gear system, such as gearboxes or transmissions. The assembled gear system may undergo further testing, including load testing, noise testing, and performance evaluation, to ensure proper functionality and performance.
It’s important to note that the manufacturing process for straight bevel gears may vary depending on the specific requirements, gear size, production volume, and the capabilities of the manufacturing facility. Advanced manufacturing technologies, such as computer numerical control (CNC) machining and gear cutting machines, are often utilized to achieve high precision and efficiency in the production of straight bevel gears.