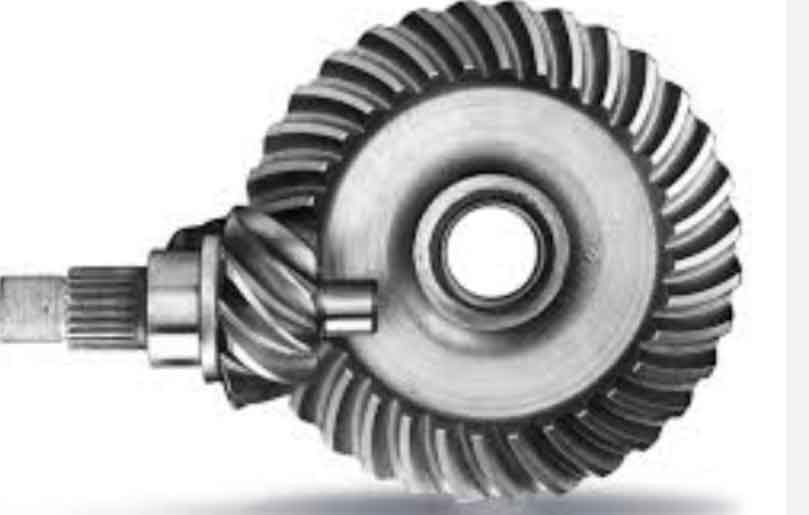
The mechanics of hypoid gear meshing involve the interaction of the gear teeth as they come into contact during operation. The unique characteristics of hypoid gears, such as their helical and spiral bevel teeth and offset configuration, influence the meshing process and contact patterns. Here’s an exploration of the mechanics of hypoid gear meshing and contact patterns:
1. Helical and Spiral Bevel Teeth:
- Hypoid gears have helical teeth, which are cut at an angle to the gear axis, and spiral bevel teeth, which are cut in a spiral pattern. The helical and spiral tooth forms contribute to smoother and gradual tooth engagement compared to straight-cut bevel gears, reducing impact and noise during meshing.
2. Offset Configuration:
- The primary characteristic of hypoid gears is their offset configuration, where the axes of the pinion and the ring gear do not intersect. This offset introduces an angular misalignment between the mating gear axes, which results in hypoid gear teeth sliding across each other during meshing.
3. Line and Point Contact:
- During meshing, hypoid gears experience line contact and point contact. The line contact occurs along the gear teeth’s length as they mesh, while the point contact happens at specific contact points where the teeth first come into contact.
4. Contact Pattern Analysis:
- The contact pattern analysis is a critical step in the design and manufacturing of hypoid gears. It involves inspecting the contact pattern formed by the mating gear teeth during meshing. The objective is to achieve a well-centered and uniform contact pattern on the gear teeth surfaces to ensure proper load distribution.
5. Load Distribution:
- Hypoid gears distribute the transmitted load over a larger area of the gear tooth flank compared to straight-cut bevel gears. The offset configuration, combined with the helical and spiral tooth forms, results in a more gradual and even load distribution along the gear teeth, reducing stress concentrations and enhancing load-carrying capacity.
6. Backlash and Clearance:
- The angular offset and sliding action during meshing contribute to the gear backlash, which is the clearance between mating gear teeth when they are not engaged. Properly controlling the backlash is essential to achieving the desired gear performance and minimizing noise.
7. Sliding Motion:
- The sliding motion between the hypoid gear teeth during meshing creates relative movement and can generate friction. Proper lubrication and surface treatments are employed to reduce friction and wear, ensuring smooth gear operation and longevity.
8. Minimizing Edge Loading:
- Edge loading occurs when the contact pattern is too close to the gear tooth’s edge, leading to localized high stresses and potential gear failure. Careful gear design and setup adjustments are performed to avoid edge loading and achieve optimal load distribution.
The mechanics of hypoid gear meshing and contact patterns are complex, but they play a crucial role in determining the performance, efficiency, and durability of the gear system. By carefully designing and manufacturing hypoid gears with appropriate tooth profiles, offset angles, and contact patterns, engineers can ensure the smooth and efficient operation of gear drives in various industrial applications.