Smart automation is revolutionizing gear manufacturing by integrating advanced technologies such as artificial intelligence (AI), robotics, and the Internet of Things (IoT). These innovations are transforming traditional gear manufacturing processes, leading to increased efficiency, precision, and cost-effectiveness. Let’s delve into how smart automation is shaping the future of gear production.
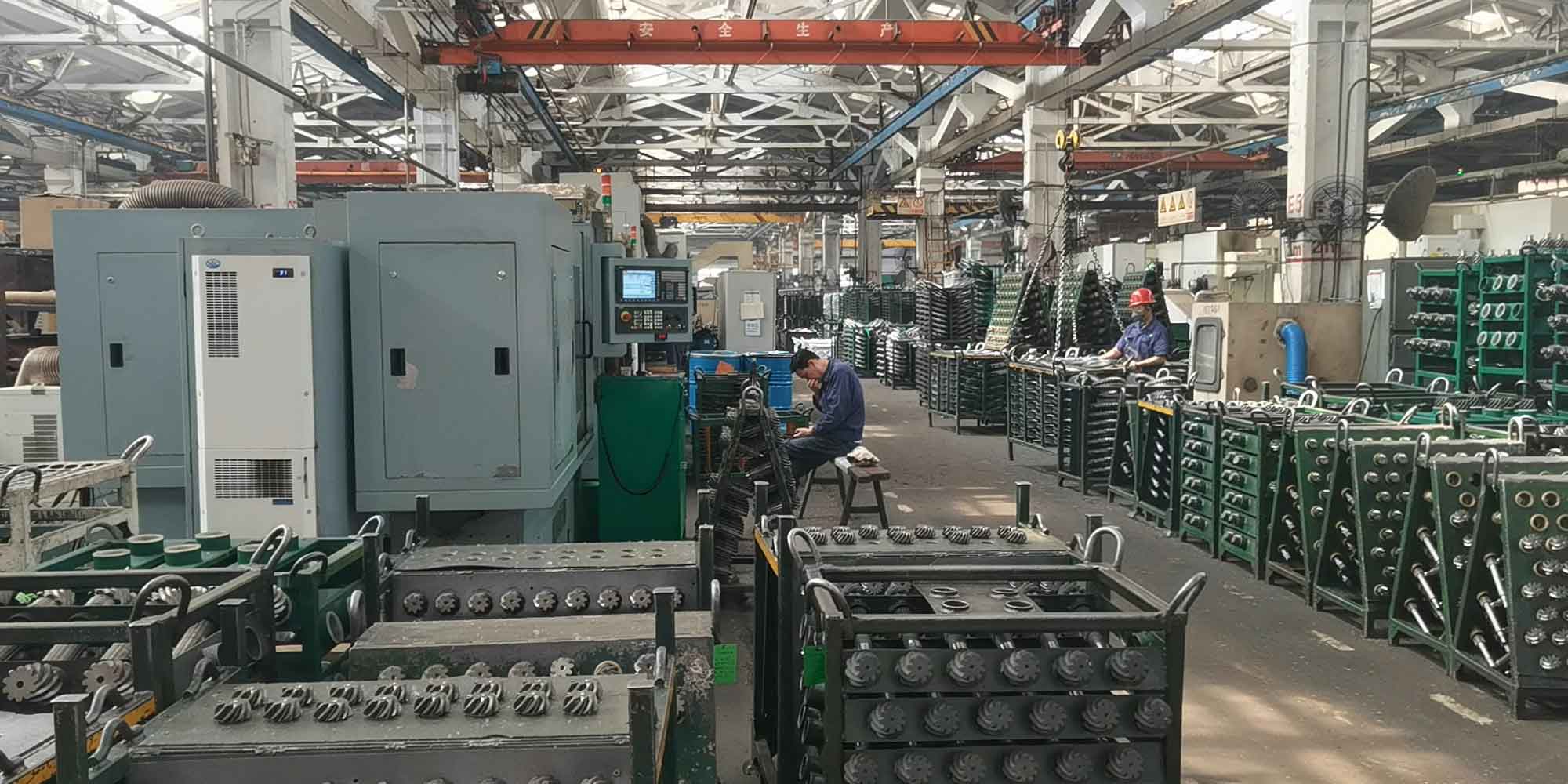
Key Technologies Driving Smart Automation
- Artificial Intelligence and Machine Learning: AI and machine learning algorithms are used to optimize gear manufacturing processes, predict maintenance needs, and enhance quality control. In gear manufacturing, AI can analyze vast amounts of data from production runs to detect patterns and predict potential failures before they occur.
- Robotics: Robots have been a staple in gear manufacturing for decades, but modern robots are more versatile, capable of performing complex tasks with high precision. In gear manufacturing, robots are used for tasks such as loading and unloading materials, assembly, and even complex machining, all with minimal human intervention.
- Internet of Things (IoT): IoT technology enables machinery and equipment to communicate in real-time. Sensors can track everything from machine performance to environmental conditions, providing a comprehensive view of the production floor. This connectivity allows for real-time monitoring and adjustments, further optimizing production efficiency.
Benefits of Smart Automation in Gear Manufacturing
- Increased Efficiency: Automated systems can operate continuously, reducing downtime and increasing production rates.
- Improved Precision and Quality: Smart machines can maintain extremely high precision over long production periods, reducing the margin of error and improving the overall quality of the gears produced.
- Cost Reduction: Although the initial investment in smart automation technologies can be high, the long-term savings in labor, maintenance, and waste reduction can be significant.
- Enhanced Flexibility: Automated systems can be quickly reconfigured for different types of gear production, allowing gear manufacturers to adapt to changing market demands without significant downtime.
Challenges and Considerations
While the benefits are significant, the shift towards smart automation also presents challenges:
- High Initial Investment: The cost of implementing advanced automated systems can be prohibitive for smaller gear manufacturers.
- Skill Gap: There is a growing need for skilled workers who can operate and maintain these sophisticated systems, leading to a skills gap in the workforce.
- Cybersecurity Concerns: With increased connectivity comes greater risk of cyber attacks, which can disrupt production and compromise sensitive data.
The Future Outlook
As technology continues to advance, the integration of even more sophisticated AI, along with advancements in materials science and digital twin technologies, will further enhance the capabilities of gear manufacturers. This could lead to even greater efficiencies, customizations, and new business models centered around smart gear manufacturing ecosystems.
In conclusion, smart automation is setting a new standard in gear manufacturing, driven by technological advancements that promise not only to improve efficiency and quality but also to redefine the industry. As gear manufacturers continue to adopt these technologies, they will likely see significant transformations in their production processes and business models.