Spur gear is critical components in heavy machinery, where they are subjected to substantial loads and rigorous operating conditions. The failure of spur gear can lead to significant downtime, costly repairs, and even catastrophic failures in heavy machinery. Understanding the common failure modes and implementing effective prevention strategies is essential to ensure the reliability and longevity of spur gear. This article explores the causes of spur gear failure in heavy machinery and presents strategies for preventing these failures.
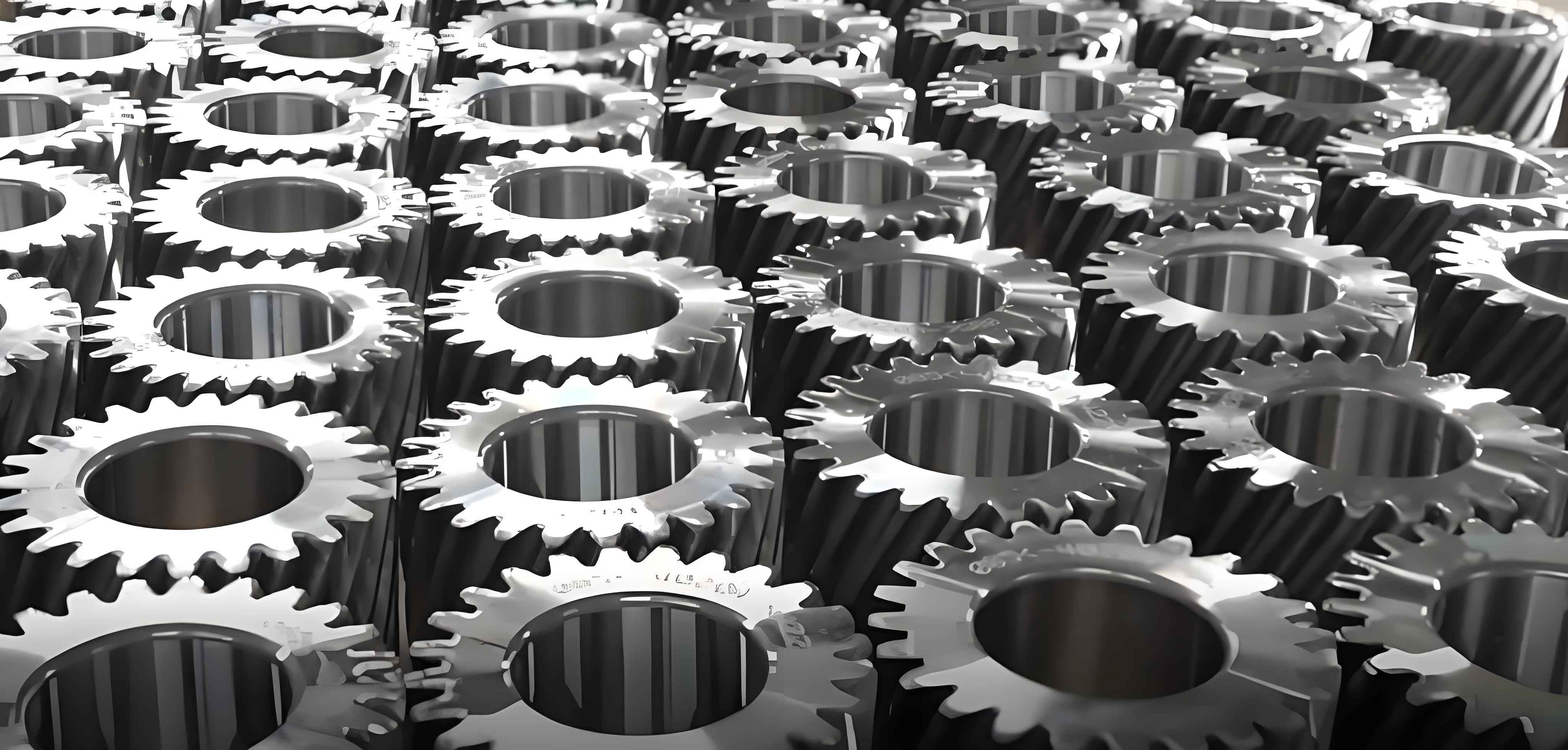
Common Failure Modes of Spur Gear
Spur gear in heavy machinery are prone to various types of failures due to the extreme conditions they operate under. The most common failure modes include:
1. Tooth Wear: Tooth wear occurs due to the continuous sliding contact between gear teeth. This wear can be exacerbated by inadequate lubrication, abrasive contaminants, and excessive loads.
2. Pitting: Pitting is the formation of small pits on the gear tooth surface due to surface fatigue. It typically occurs when the contact stress exceeds the material’s fatigue strength, leading to the removal of small particles from the surface.
3. Spalling: Spalling is a more severe form of surface fatigue where larger flakes of material are removed from the gear tooth surface. It is often the result of prolonged pitting and excessive loading.
4. Tooth Bending Fatigue: Tooth bending fatigue is caused by repeated cyclic loading, leading to cracks at the tooth root and eventual tooth breakage. This type of failure is common in spur gear subjected to fluctuating loads.
5. Scuffing: Scuffing is a severe form of adhesive wear that occurs when there is metal-to-metal contact between gear teeth. It is usually caused by insufficient lubrication, high loads, and high surface temperatures.
6. Corrosion: Corrosion of spur gear can occur in environments with high humidity or exposure to corrosive substances. This leads to the deterioration of the gear material and reduced load-carrying capacity.
Table 1: Common Failure Modes of Spur Gear
Failure Mode | Cause | Symptoms | Consequences |
---|---|---|---|
Tooth Wear | Inadequate Lubrication, Contaminants | Surface Roughness, Noise | Reduced Efficiency, Increased Heat |
Pitting | Surface Fatigue, High Contact Stress | Small Surface Pits | Material Loss, Increased Noise |
Spalling | Prolonged Pitting, Excessive Loading | Large Surface Flakes | Severe Material Loss, Gear Failure |
Tooth Bending Fatigue | Cyclic Loading | Cracks at Tooth Root | Tooth Breakage, Catastrophic Failure |
Scuffing | Insufficient Lubrication, High Loads | Surface Scoring | Metal Transfer, Surface Damage |
Corrosion | Humidity, Corrosive Substances | Surface Deterioration | Reduced Load Capacity, Structural Weakening |
Failure Prevention Strategies for Spur Gear
Preventing the failure of spur gear in heavy machinery involves implementing a combination of design, material selection, lubrication, and maintenance strategies. Here are some effective strategies for preventing spur gear failures:
1. Optimal Material Selection: Using high-strength materials with good fatigue resistance and wear properties can significantly reduce the likelihood of gear failures. Materials such as high-strength alloy steels, stainless steels, and surface-hardened steels are commonly used for high-performance spur gear.
2. Advanced Heat Treatment: Heat treatment processes like carburizing, nitriding, and induction hardening can improve the hardness and wear resistance of gear teeth, enhancing their durability and resistance to failure.
3. Proper Lubrication: Ensuring adequate lubrication is critical for preventing wear, pitting, and scuffing. Using high-quality lubricants with appropriate viscosity and additives can reduce friction and wear between gear teeth.
4. Regular Maintenance and Inspection: Implementing a regular maintenance schedule that includes inspection for signs of wear, pitting, and other failure modes can help identify potential issues before they lead to catastrophic failures.
5. Surface Coatings: Applying advanced surface coatings, such as titanium nitride or diamond-like carbon, can enhance the wear resistance and surface hardness of gear teeth, reducing the risk of wear and scuffing.
6. Proper Gear Design: Designing gears with optimal tooth profiles, pressure angles, and load distribution can reduce stress concentrations and improve the load-carrying capacity, minimizing the risk of bending fatigue and surface fatigue.
7. Environmental Control: Protecting spur gear from corrosive environments by using corrosion-resistant materials and coatings can prevent corrosion-related failures.
List: Key Strategies for Preventing Spur Gear Failures
- Optimal Material Selection: Choose materials with high strength and fatigue resistance.
- Advanced Heat Treatment: Enhance hardness and wear resistance through heat treatment.
- Proper Lubrication: Use high-quality lubricants to reduce friction and wear.
- Regular Maintenance and Inspection: Schedule regular inspections to identify early signs of failure.
- Surface Coatings: Apply wear-resistant coatings to gear teeth.
- Proper Gear Design: Optimize gear design to reduce stress concentrations.
- Environmental Control: Protect gears from corrosive environments.
Table 2: Failure Prevention Strategies for Spur Gear
Strategy | Primary Benefit | Typical Application | Implementation Cost | Long-Term Benefit |
---|---|---|---|---|
Optimal Material Selection | Enhanced Durability | High-Load, High-Stress Gears | Moderate | High |
Advanced Heat Treatment | Improved Hardness | Heavy Machinery, Industrial Equipment | Moderate | High |
Proper Lubrication | Reduced Friction and Wear | All Spur Gears | Low | High |
Regular Maintenance | Early Failure Detection | Heavy Machinery, Automotive | Moderate | Very High |
Surface Coatings | Increased Wear Resistance | High-Performance Gears | High | Very High |
Proper Gear Design | Reduced Stress Concentration | Custom Gear Applications | Moderate | High |
Environmental Control | Prevention of Corrosion | Marine, Chemical Processing | Variable | High |
Conclusion
The failure of spur gear in heavy machinery can have severe consequences, including costly downtime and repairs. By understanding the common failure modes and implementing effective prevention strategies, it is possible to enhance the reliability and longevity of spur gear. Optimal material selection, advanced heat treatments, proper lubrication, regular maintenance, surface coatings, proper gear design, and environmental control are all critical strategies for preventing spur gear failures. By adopting these measures, manufacturers and operators can ensure that their spur gear perform efficiently and reliably, even under the most demanding conditions.