Helical gears are widely used in various mechanical systems due to their excellent performance, such as good meshing performance, large overlap ratio, compact structure, low noise, and high load-carrying capacity. Understanding the contact characteristics of helical gears is crucial for improving their reliability and performance. In this article, we will discuss the finite element analysis of the contact characteristics of helical gears, including the effects of plastic deformation, tooth surface friction, temperature, and material linear strengthening on the meshing performance.
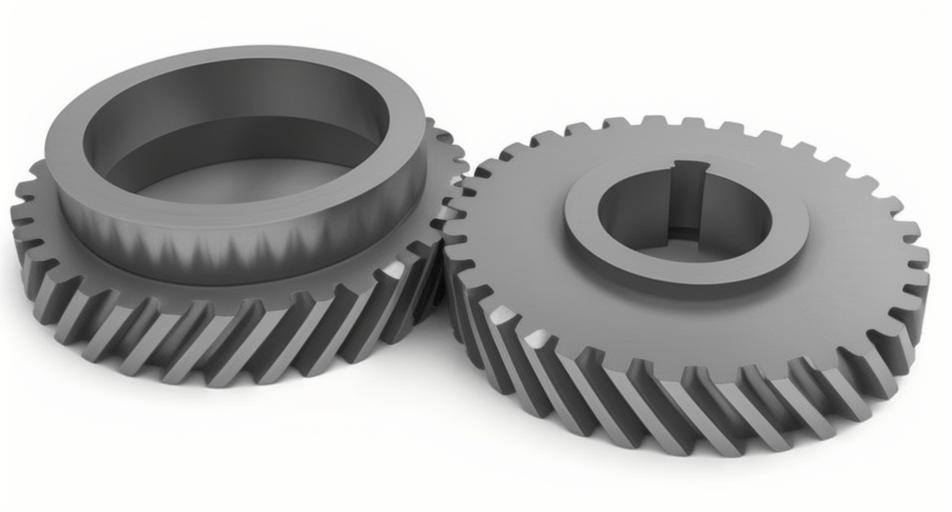
Introduction
Helical gears have many advantages, making them suitable for high-speed and heavy-duty transmissions. Studying the load distribution on the tooth surface and the stress distribution at the tooth root during a complete meshing cycle is essential for researching gear cracks and fatigue life. Finite element analysis is one of the main methods to solve such problems.
Many scholars have conducted research on gear contact analysis. They have studied the influence of factors such as tooth surface friction, temperature, and material properties on the meshing performance of gears. However, there is a lack of systematic research on the effects of plastic deformation, tooth surface friction, temperature, and linear strengthening on the tooth surface contact force.
Three-Dimensional Modeling of Helical Gears
The involute curve equation of the helical gear in processing can be obtained by combining the basic involute equation with the involute in the gear processing coordinate system. The equation is as follows:
where is the base circle radius, is the pressure angle at any point on the involute, is the number of teeth, is the pressure angle, and is the involute function.
The tooth profile parameters of the rack-type tool for processing the tooth root transition curve of the gear are expressed as follows:
where is the radius of the fillet at the tooth root of the processed gear, is the distance from the center to the centerline, is the distance from the center to the centerline, is the normal module, is the radial modification coefficient, is the normal pressure angle, and is the normal addendum coefficient.
The parameter equation of the tooth root transition curve can be obtained based on the involute equation and the tooth profile parameters:
where is the angle between and the tool processing pitch line, and is an auxiliary variable.
The basic geometric parameters of the helical gear are shown in Table 1.
Parameter | Value |
---|---|
Number of teeth (z1/z2) | 18/27 |
Normal modulus (m) / mm | 4 |
Normal pressure angle (α) / ° | 20 |
Helix angle (β) / ° | 12 |
Tooth width (B) / mm | 20 |
Normal addendum coefficient (h_a) | 1 |
Radial modification coefficient (c_x) | 0.25 |
Based on the above tooth profile curve, tooth root curve, and related parameters of the helical gear, the three-dimensional modeling of the helical gear is completed in SolidWorks, as shown in Figure 3.
Tooth Contact Analysis
Elastic Model Contact Analysis
By inputting two different strain curves, the elastic and elastoplastic models can be obtained. For the elastic model, only the linear elastic strain curve needs to be added, while for the elastoplastic model, only the yield strength needs to be added (other parameters remain the same as the elastic model). Then, the curve ① in Figure 4 can be input.
If the material does not reach the yield strength, the curve ② shows a linear elastic relationship. When the stress exceeds the yield strength ( MPa), it shows a linear strengthening relationship. When setting the material properties, the curve ② in Figure 4 is added: the oblique straight line approximates the stress-strain relationship of different strengthening degrees, so that the linear strengthening elastoplastic model can be obtained, which is expressed as:
where is the stress, is the yield strength, is the stress-strain, is the strain corresponding to the stress reaching the yield strength, and is the material strengthening modulus.
When , it is the ideal elastoplastic model.
The convection heat transfer coefficients for the gear end face and the meshing face are calculated as follows:
where is the kinematic viscosity of the lubricating oil, is the thermal conductivity, is the radius of the contact point on the tooth surface, is the angular velocity of the gear, is the Nusselt index, is the Prandtl index, is the index constant, and is taken. is the height of the gear at any contact point, and are the density and kinematic viscosity of the lubricating oil, and are the specific heat and thermal conductivity of the lubricating oil, is the thermal diffusion coefficient, is the standardized total cooling capacity, is the centrifugal acceleration, and is the total time of the ejection process.
The friction heat flux density of the gear is calculated as follows:
The average heat flux densities on the contact tooth surfaces of the driving and driven wheels are and , respectively, which are expressed as:
where is the friction heat flux density distribution factor, is the coefficient of converting friction energy into thermal energy, is the friction coefficient, is the relative sliding speed of the contact point on the meshing line of the driving wheel, is the average contact pressure, is the time for the friction heat flux density in the contact area of the driving wheel to pass through the contact width, and is the time for the driving wheel to mesh for one week.
Heat flux density is applied to the meshing contact tooth surfaces, and convection heat transfer coefficients are applied to the tooth top surface, tooth root surface, and gear end face. The tooth top and tooth root surface convection heat transfer coefficients can be equivalent to 1/3 of the convection heat transfer coefficient of the gear meshing face. The load boundary conditions for the temperature field are shown in Figure 5.
To reduce the calculation amount, six teeth of the large and small gears are intercepted for meshing, and four teeth of the driving wheel are studied and analyzed. The hexahedral C38R is selected for mesh division, and the mesh is encrypted at the tooth contact surface and the tooth root position. Now, an angular velocity of r/s is applied to the driven wheel, and a torque of N·m is applied to the driving wheel, as shown in Figure 5.
It can be seen from Figure 6 that the contact state of the tooth surface in the helical gear transmission is always in the alternating state of two teeth – three teeth – two teeth. Figure 6(a) shows the two-tooth meshing, Figure 6(b) shows the beginning of the three-tooth meshing, Figure 6(c) shows the end of the one-tooth meshing, and Figure 6(d) shows the beginning of the four-tooth meshing.
The tooth surface contact load of the helical gear always moves and distributes along the spiral line during the meshing transmission, and the tooth surface contact load moves from the tooth root to the tooth top gradually. Due to the continuous alternation of two-tooth and three-tooth meshing during the meshing process, the length of the contact line also changes continuously, resulting in the corresponding change of the contact load on the gear teeth with the meshing position of the gear. The total contact force calculated by the simulation is approximately 42,111.7 N, while the theoretical calculation value is approximately 42,597.5 N, and the error between the simulation and the theoretical calculation is 1.14%, which verifies the correctness of the established simulation contact model.
Influence of Plastic Deformation
Considering the tooth surface contact force under different loads (400, 1000, 1500, 2000 N·m) based on the elastoplastic model, as shown in Figure 7.
It can be clearly observed from Figure 7 that when the plastic parameters of the material are considered, the contact force of the target tooth surface in the stable length stage of the contact line (when the contact load is stable) is greater than the tooth surface contact force of the elastic model under the same conditions. Compared with the elastic model, the tooth surface contact force of the elastoplastic model increases by approximately 0.11%, 1.84%, 2.01%, and 3.13%, respectively, and the greater the torque, the more obvious the difference.
As shown in Figure 5, the 2 teeth of the driving wheel are cut along the x – y section, and the subsurface stress change along the x – y section at the node under a load of 1500 N·m is extracted, as shown in Figure 8.
Within a certain depth range, the subsurface stress of the elastic model is always greater than that of the elastoplastic model, and the subsurface stress of both models will decrease with the increase of the depth. The rate of stress reduction of the elastoplastic model is lower than that of the elastic model. Because the material will produce plastic deformation after being loaded, part of the external load energy is converted into the potential energy between the microscopic grains of the material, and this potential energy will be converted into plastic deformation and exist in the material, resulting in residual stress. Therefore, as the load increases, the stress will also continue to increase. To study the change of subsurface plastic deformation, the plastic deformation regions on the x – y section under four working conditions at the same moment are extracted, as shown in Figure 9.
As the load increases, the plastic deformation region will gradually expand, and the area of the maximum plastic deformation region will also increase. Because when the stress of the gear reaches the yield strength, the plastic deformation will increase with the increase of the load. Therefore, considering the plastic parameters of the material has a non-negligible influence on the tooth surface contact characteristics.
Influence of Tooth Surface Friction
The friction coefficient of the tooth surface in gear meshing is less than or equal to 0.2. Combining relevant research and the parameters of the helical gear in this article, the friction coefficient of the tooth surface in this simulation calculation is selected in the range of 0.01 to 0.2. In the elastic model, the tooth surface is set as a friction contact model without considering friction, and the change curve of the contact force of the 2 teeth under three different friction coefficients (0.05, 0.10, 0.15) is studied, as shown in Figure 10.
When the contact line is in a stable length, the greater the friction coefficient, the greater the contact force. When there is friction on the contact tooth surface, the tooth surface friction state is sliding friction, so the contact area will decrease. Therefore, the tooth surface contact force is greater than the contact force without considering friction.
The tooth root stress under four friction coefficients is shown in Figure 11. It can be seen that as the friction coefficient increases, the tooth root stress also increases. Because the friction force on the tooth surface during gear meshing will change the contact stress and the deformation of the gear teeth, the tooth root stress will also change. Therefore, the influence of tooth surface friction on the contact load of the gear teeth cannot be ignored.
Influence of Temperature
To study the influence of temperature on the tooth surface contact force, the friction coefficient of the tooth surface is set to 0.1, other parameters remain unchanged, and the change curve of the torque of 1500 N·m is shown in Figure 12.
After considering the friction heat between the gear teeth in the helical gear contact analysis model, the gear tooth surface will generate heat due to the mutual contact friction, resulting in an increase in the tooth surface temperature. Since the average kinetic energy between the molecules of the material increases when the temperature rises, the molecules will move relatively, resulting in a decrease in the interaction force between the molecules, and ultimately a relative reduction in the yield stress of the material and a decrease in the contact pressure. Then, the material begins to soften, and the contact area will gradually expand, so the tooth surface contact force will decrease accordingly. In summary, the maximum value of the tooth surface contact force considering the temperature is lower than the maximum value without considering the temperature, indicating that the tooth surface contact temperature has a certain influence on the contact force, but the influence is not obvious.
Tooth surface friction will cause the contact surface to soften and lead to an increase in the contact area. Due to the extrusion of the molecules in the body and the transfer of temperature to the gear body, thermal stress is generated on the subsurface, resulting in the subsurface stress being greater than that without considering the temperature within a certain depth, as shown in Figure 13, and both stresses will gradually decrease with the increase of the depth. To study the influence of temperature on plastic deformation, Figure 14(a) and Figure 14(b) show the plastic regions without considering temperature and considering temperature, respectively.
The expansion direction of the center of the plastic deformation region considering the temperature shifts, which is due to the distortion of the subsurface stress caused by the uneven temperature distribution on the subsurface. Within a certain depth, the stress considering the temperature is higher than that without considering the temperature, so the area of the corresponding plastic deformation will also increase accordingly.
The temperature field distribution of the 2 tooth surface of the driving wheel is shown in Figure 15, and the temperature change curves of four paths along the tooth height and tooth width directions are extracted. It can be seen that the highest temperature on the contact surface is about 67.61°C, near the tooth root, and the second-highest temperature is 58.82°C, near the tooth top. Since the relative sliding speed at the alternation of two-tooth and three-tooth meshing is larger, and the heat flux generated by friction is positively correlated with the relative sliding speed, the heat flux increases when the gear teeth alternate, so there are two local temperature peak regions on the contact tooth surface. From Routes 1, 2, and 3, it can be seen that the temperature in the middle of the temperature field along the tooth width direction is high, and the temperature at both ends is low, which is caused by the convective heat dissipation of the gear end face and the lubricating oil mixture.
Influence of Linear Strengthening
To study the stress changes on the contact surface of three different linear strengthening models (that is, the material hardening degree is 0, 1% , and 3% , respectively, where is the elastic modulus) under different working conditions, the maximum stress on the surface of the 2 teeth of the driving wheel is extracted, as shown in Figure 16.
Before reaching the yield stress, the hardening degrees of the three models are different, so the linear elastic strain curves are not consistent. Within a certain torque range, the stress of the model is significantly greater than that of the and models because its material hardening degree is lower than that of the other two models, so the deformation is the largest, that is, the stress is the largest. After reaching the yield stress, the stress of the model is not greater than that of the other two models because it is an ideal elastoplastic model, and the stress will not change with the increase of the load. When the torque reaches 1700 N·m, the stress values of the two models are the same. Due to the different material hardening degrees, the deformation of is smaller than that of under the same load. When the torque is less than 1700 N·m, the stress of is lower than that of . When the torque reaches 1700 N·m, the stress values of the two models are higher than the yield stress, and the slope of the oblique straight line in the strengthening stage of is greater than that of , so its stress change rate is greater than that of , and therefore its stress is higher than that of .
The subsurface stress and the corresponding plastic deformation changes of the same node on the x – y section of the 2 teeth of the driving wheel in the three strengthening models under the 1000 N·m working condition are selected, as shown in Figure 17.
The subsurface stress of the model is significantly smaller than that of the other two models, but its corresponding plastic deformation is the largest. Because when the stress is greater than the yield stress, under the same stress, the plastic deformation will decrease with the increase of linear strengthening. In summary, the selection of material strengthening parameters under different working conditions has different effects on the contact stress, so a more realistic material strengthening model should be selected for theoretical research.
Experimental Verification
The experiment is carried out using the MCL – 1A gear wear testing machine, which is driven by the spindle motor. Through the driving gearbox, elastic shaft, and test gearbox, the rotation speed is applied to the experimental gear. The target value of the experimental torque is set on the main control console, and it is added by the loading clutch. The torque value is displayed in the main control console through the (dynamic) torque sensor, and the loading stops when the target value is reached. Then, the rotation speed and running time are set in the main control console, and the test starts by clicking send. Figure 18(a) shows the principle diagram of the MCL – 1A, and Figure 18(b) shows the physical picture of the MCL – 1A on site.
Temperature Rise Test Experiment
Due to the temperature generated by the friction of the contact tooth surface during gear meshing, the contact load distribution will be affected. In this experiment, the temperature is transmitted to the multi – temperature inspection instrument for real – time monitoring through the thermocouple temperature sensor, and the test site is shown in Figure 18(c). To simulate the quasi – static working condition, the gear speed is set to 33 r/min, and the temperature in the measurement area under different working conditions is taken. To reduce the experimental error, the test bench is allowed to run for a period of time to reach thermal equilibrium before the experiment starts and the measurement is taken.
The temperature rise distribution curves of the simulation and the experiment under different torques are shown in Figure 19. The simulation and experimental results of the tooth root and tooth top contact areas both take the average temperature. Due to the different heat dissipation effects at different locations and the inconsistent oil inlet distribution of the lubricating oil on the tooth surface during gear meshing, the cooling effect is uneven, resulting in different temperature distributions at the tooth top and tooth root. Since the tooth top measurement area in the experiment is near the tooth top circle, the lubrication effect is poor, while the tooth root measurement area is close to the tooth root circle, the contact area is small, and the heat dissipation effect is good, so the temperature will be lower than that at the tooth top. Because the temperature field simulation is in an ideal environment, and in the experiment, due to factors such as the difference in the ambient temperature and the heat dissipation of the gear itself, the experimental results are lower than the simulation results. Moreover, the temperature increases with the increase of the load, but the temperature change trend in the experiment and the simulation is basically the same, and the relative error is also within an acceptable range, which illustrates the correctness of the simulation model.
Strain Test Experiment
To study the bending stress at the tooth root, the experiment will be carried out under three working conditions, with a rotation speed of 33 r/min and loading torques of 600, 800, and 1500 N·m, respectively, which are Working Condition 1, Working Condition 2, and Working Condition 3. The test site is shown in Figure 18(d). The experimental results are compared with the simulation results to calculate the relative error and verify the simulation model. Due to the certain deviation of the input torque of the experimental bench and the influence of installation errors, tooth profile errors, transmission errors, and meshing impact, there will be errors in the experimental results.
Since the measured gear is squeezed by the impact of the previous pair of teeth exiting and the subsequent pair of teeth entering, the bending stress in Figure 20 shows a trend of first convex and then concave. The maximum tensile stress appears near the double – tooth meshing position, and the strain values in other areas are basically zero because the measured gear exits the meshing and is not subjected to the load.
The maximum bending stress in the experiment and the simulation does not occur at the same moment because the frequency of point selection in the strain test in the experiment is different from the time step setting in the simulation calculation, and there is a certain deviation between the position of the strain gauge patch and the node position extracted in the simulation. However, the change curves of the two are basically the same, indicating that the loading state of the gear in the simulation and the experiment is consistent.
The comparison between the simulation and the experimental maximum bending stress is shown in Table 2. The experimental results in all three working conditions are slightly larger than the simulation results, but the error of the experimental stress value relative to the simulation stress value does not exceed 20%, indicating that the experimental results are within the ideal range and verifying the accuracy of the above contact model.
Working Condition | Simulation Result / MPa | Experimental Result / MPa | Error /% |
---|---|---|---|
1 | 113.52 | 133.58 | 17.67 |
2 | 146.22 | 173.78 | 18.85 |
3 | 262.63 | 295.47 | 12.50 |
Conclusion
A three – dimensional model of the helical gear is established, and the gear is subjected to contact analysis using the finite element method. The effects of plastic deformation, tooth surface friction, temperature, and material linear strengthening on the contact characteristics are studied. Finally, the experimental results are compared with the simulation results through experiments to verify the simulation model. The following conclusions are drawn:
- Under four loads (400, 1000, 1500, 2000 N·m), the tooth surface contact force of the elastoplastic model at the stable length of the contact line increases by approximately 0.11%, 1.84%, 2.01%, and 3.13% compared with the elastic model, respectively, and the effect is more obvious with the increase of the load. Within a certain subsurface depth range, the stress of the elastoplastic model is always not greater than that of the elastic model, but its reduction rate is smaller than that of the elastic model with the increase of the depth, and the plastic deformation area of the subsurface will expand with the increase of the load.
- After considering the tooth surface friction, the tooth surface contact force in the stable length stage of the contact line is greater than the tooth surface contact force without considering the friction coefficient. Moreover, the greater the friction coefficient, the greater the tooth root stress.
- Considering the influence of the tooth surface temperature on the contact load, the maximum value of the tooth surface contact force considering the temperature will be smaller than the contact force without considering the temperature, indicating that the temperature has a certain influence on the tooth surface contact force distribution.
- The surface maximum stress change trends of the three strengthening models in different load ranges are different, so the subsurface stress and plastic deformation are also different. This shows that selecting the appropriate material strengthening degree has an important influence on the contact surface stress.
- Through the temperature rise experiment, it can be known that due to the poor heat dissipation effect at the tooth top, the temperature in the tooth top area is higher than that in the tooth root area in both the experiment and the simulation, and the experimental results are lower than the simulation results, but the change trend is consistent, indicating the reliability of the simulation model. In the strain test, the change trend of the tooth root bending stress is basically the same as that of the simulation curve, and the relative error between the two maximum bending stresses is within 20%, which is within an acceptable range, thus verifying the accuracy of the simulation model.
In future research, we can further explore the influence of other factors on the contact characteristics of helical gears, such as the surface roughness of the tooth surface, the lubrication conditions, and the manufacturing errors of the gears. Additionally, developing more accurate and efficient finite element analysis methods and experimental techniques can provide more reliable results for the design and optimization of helical gears.