Forging precision and achieving tight tolerances in gear manufacturing is a critical aspect of producing high-quality gears. Tight tolerances ensure proper gear meshing, precise transmission of motion, and optimal performance. Here’s how gear forging achieves tight tolerances in gear manufacturing:
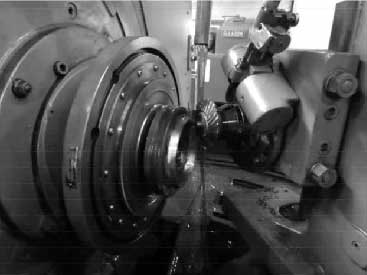
- Near-Net Shape Forging: Gear forging starts with a near-net shape approach, where the initial forging process shapes the gear blank as close as possible to the final dimensions. This near-net shape forging minimizes the amount of material that needs to be removed in subsequent machining operations. By reducing material removal, tight tolerances can be achieved more efficiently, resulting in cost savings and improved productivity.
- Die Design and Tooling: The design and precision of the forging dies and tooling used in the gear forging process play a crucial role in achieving tight tolerances. The dies are designed to accurately shape the gear blank and maintain the desired dimensional accuracy throughout the forging process. High-quality tooling ensures consistent and precise shaping of the gear teeth, minimizing dimensional variations and achieving tight tolerances.
- Process Control and Monitoring: Gear forging processes incorporate advanced process control and monitoring techniques to ensure dimensional accuracy and tight tolerances. Real-time monitoring systems track important parameters such as temperature, pressure, and force during forging. By closely monitoring these variables, any deviations from the desired specifications can be identified and corrected, leading to improved precision and tighter tolerances.
- Heat Treatment Optimization: Heat treatment is an integral part of gear forging to enhance the mechanical properties of the forged gears. Proper heat treatment processes, such as quenching and tempering, are applied to achieve the desired hardness, strength, and dimensional stability. By carefully controlling the heat treatment parameters, such as time, temperature, and cooling rates, the dimensional changes during heat treatment can be minimized, ensuring the gears maintain tight tolerances.
- Precision Machining: Although gear forging achieves near-net shape, some gears may still require post-forging machining to achieve the final desired dimensions and surface finish. Precision machining techniques, such as grinding, honing, or lapping, are employed to achieve tight tolerances on critical gear features like tooth profile, pitch, and concentricity. CNC machining processes with advanced measuring and control systems ensure the precise removal of material, resulting in gears that meet the required tolerances.
- Inspection and Quality Control: To ensure the gears meet the desired tolerances, rigorous inspection and quality control procedures are employed throughout the gear forging process. Advanced metrology techniques, such as coordinate measuring machines (CMMs), optical scanners, and gear measurement systems, are used to measure gear profiles, tooth dimensions, and other critical parameters. These inspection tools enable the identification of any deviations from the specified tolerances, allowing for corrective actions and ensuring high precision in gear manufacturing.
By integrating these techniques and processes, gear forging achieves tight tolerances and dimensional precision in gear manufacturing. The near-net shape forging, optimized die design, process control, heat treatment, precision machining, and thorough inspection ensure that gears meet or exceed the specified tolerances, resulting in high-performance gears that deliver optimal performance and reliability in various applications.